Sintering additives play a crucial role in enhancing the sintering process, which is essential for transforming powdered materials into dense, strong, and functional components. These additives improve the efficiency of sintering by lowering the required temperature, enhancing particle bonding, and controlling microstructure formation. They also help in reducing porosity, improving mechanical properties, and achieving desired material characteristics. By optimizing the sintering process, additives enable the production of high-quality components with tailored properties for various industrial applications.
Key Points Explained:
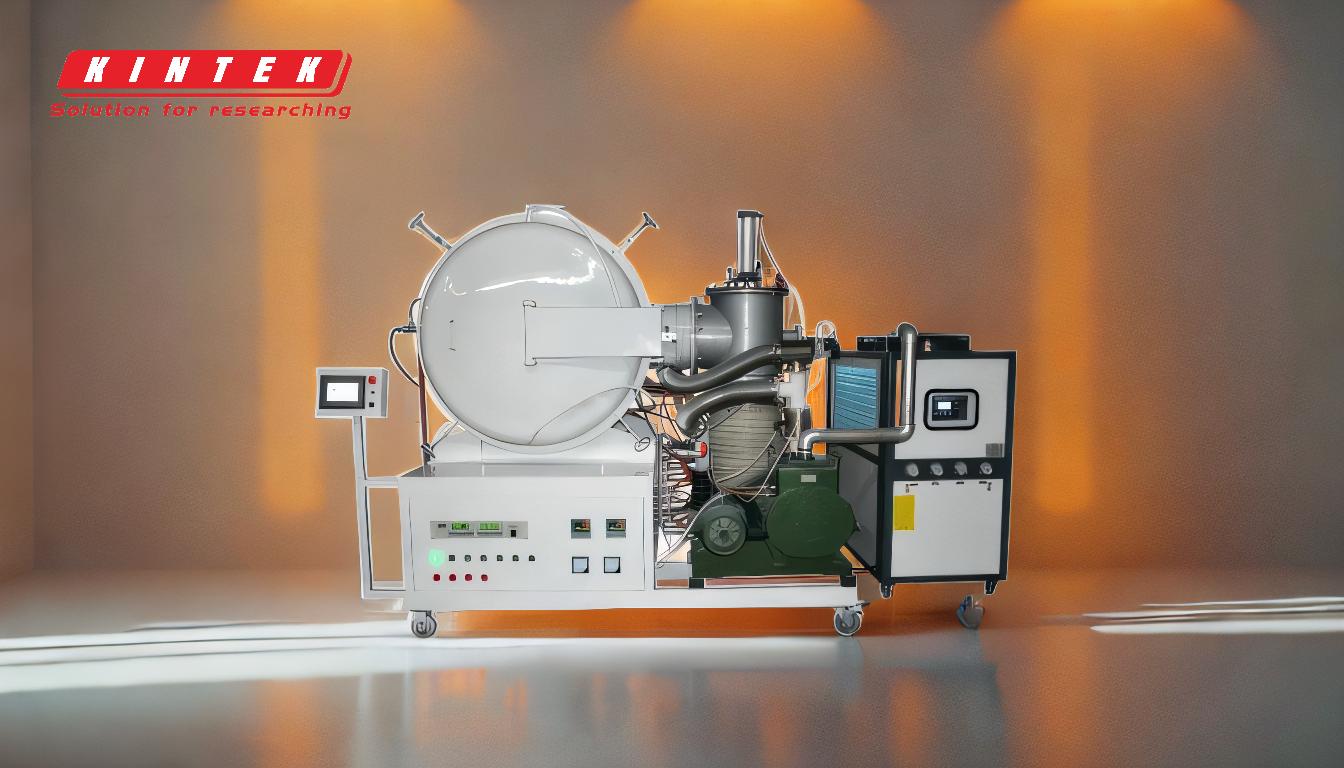
-
Lowering Sintering Temperature:
- Sintering additives reduce the temperature required for the sintering process, which is typically below the melting point of the main material. This is particularly beneficial for materials with high melting points, as it saves energy and reduces thermal stress on the equipment.
- Example: Additives like boron or silicon can lower the sintering temperature of ceramics or metals, making the process more cost-effective and efficient.
-
Enhancing Particle Bonding:
- Additives promote better bonding between particles by facilitating material transfer and diffusion at the grain boundaries. This results in stronger and more durable sintered components.
- Example: In ceramic sintering, additives like magnesium oxide (MgO) or yttrium oxide (Y₂O₃) improve grain boundary mobility, leading to denser and more uniform structures.
-
Controlling Microstructure Formation:
- Sintering additives influence the growth of grains and the elimination of pores, which directly impacts the final microstructure of the sintered material. A controlled microstructure ensures optimal mechanical, thermal, and electrical properties.
- Example: In metal sintering, additives like copper or nickel can refine grain size and improve the uniformity of the sintered part.
-
Reducing Porosity:
- Additives help in minimizing porosity by filling gaps between particles and promoting densification. Lower porosity enhances the mechanical strength, wear resistance, and overall performance of the sintered component.
- Example: In powder metallurgy, additives like graphite or wax are used to reduce porosity and improve the density of the final product.
-
Improving Mechanical Properties:
- By optimizing the sintering process, additives contribute to better mechanical properties such as hardness, tensile strength, and fracture toughness. This is critical for components used in demanding applications.
- Example: In the production of cutting tools, additives like cobalt or tungsten carbide improve hardness and wear resistance.
-
Tailoring Material Characteristics:
- Sintering additives allow for the customization of material properties to meet specific application requirements. This includes adjusting thermal conductivity, electrical conductivity, and corrosion resistance.
- Example: In electronic components, additives like silver or alumina can be used to achieve desired electrical and thermal properties.
-
Facilitating Complex Shapes and Designs:
- Additives enable the sintering of complex geometries by improving the flow and compaction of powders during the green stage. This flexibility is essential for manufacturing intricate parts.
- Example: In automotive components, additives help in producing gears and bearings with precise dimensions and shapes.
-
Cost and Energy Efficiency:
- By reducing sintering temperatures and improving process efficiency, additives contribute to lower production costs and energy consumption. This makes sintering a more sustainable manufacturing option.
- Example: In the production of industrial ceramics, additives like zirconia reduce energy requirements while maintaining high-quality outputs.
In summary, sintering additives are indispensable for optimizing the sintering process, enhancing material properties, and enabling the production of high-performance components across various industries. Their role in lowering temperatures, improving bonding, controlling microstructure, and reducing porosity ensures that sintered materials meet the stringent demands of modern applications.
Summary Table:
Key Benefit | Description | Example |
---|---|---|
Lowering Sintering Temperature | Reduces energy use and thermal stress by lowering required sintering temperatures. | Boron or silicon in ceramics/metals. |
Enhancing Particle Bonding | Improves material transfer and diffusion for stronger, more durable components. | Magnesium oxide (MgO) or yttrium oxide (Y₂O₃) in ceramics. |
Controlling Microstructure | Influences grain growth and pore elimination for optimal material properties. | Copper or nickel in metal sintering. |
Reducing Porosity | Minimizes gaps between particles to improve density and mechanical strength. | Graphite or wax in powder metallurgy. |
Improving Mechanical Properties | Enhances hardness, tensile strength, and fracture toughness for demanding uses. | Cobalt or tungsten carbide in cutting tools. |
Tailoring Material Characteristics | Customizes thermal, electrical, and corrosion properties for specific needs. | Silver or alumina in electronic components. |
Facilitating Complex Shapes | Enables precise manufacturing of intricate parts with improved powder flow. | Additives in automotive gears and bearings. |
Cost and Energy Efficiency | Lowers production costs and energy consumption for sustainable manufacturing. | Zirconia in industrial ceramics. |
Unlock the full potential of sintering additives for your materials—contact our experts today!