Molten metal handling is an inherently hazardous process that requires strict adherence to safety protocols to prevent accidents, injuries, and damage to equipment. The key to safe molten metal operations lies in using proper tools, wearing appropriate safety equipment, and following established procedures. By understanding the risks and implementing safety measures, workers can minimize the dangers associated with high-temperature metal casting and handling.
Key Points Explained:
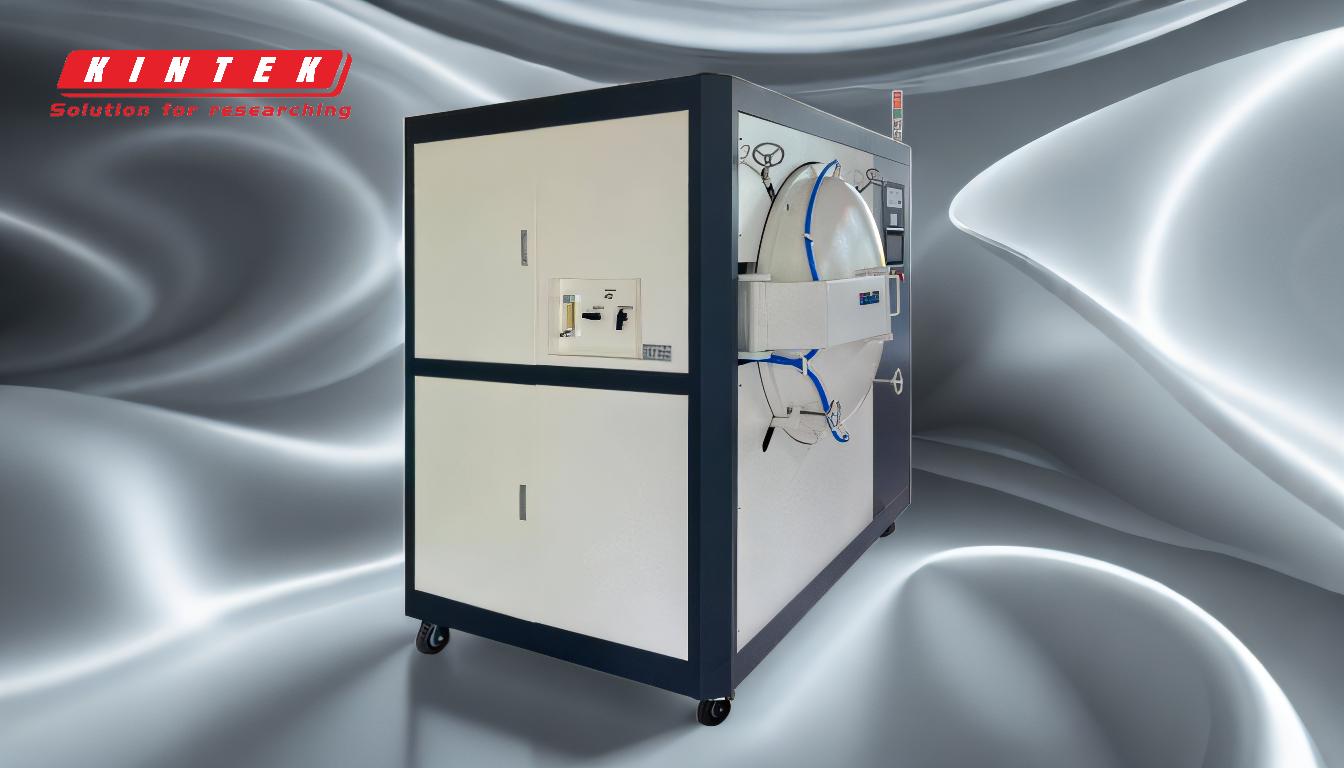
-
Use of Proper Tools for Handling Molten Metal
- Always use tools specifically designed for molten metal handling, such as ladles, crucibles, and tongs. These tools are made from materials that can withstand high temperatures and are designed to securely hold and transport molten metal.
- Ensure that tools are in good condition, free from cracks, and properly maintained. Damaged tools can fail under the stress of high temperatures, leading to spills or accidents.
- Use tools with insulated handles to protect hands from heat and to provide a secure grip during pouring or transporting.
-
Importance of Personal Protective Equipment (PPE)
- Wear heat-resistant gloves, aprons, and face shields to protect against burns and splashes. Molten metal can cause severe injuries, and PPE acts as the first line of defense.
- Use safety goggles or face shields to protect eyes from radiant heat and potential splashes. Molten metal can emit intense light and heat, which can harm unprotected eyes.
- Wear flame-resistant clothing and steel-toed boots to protect against accidental spills and falling objects.
-
Safe Handling and Pouring Techniques
- Always pour molten metal slowly and steadily to avoid splashing. Rapid pouring can cause turbulence, increasing the risk of spills or splashes.
- Ensure the workspace is clear of obstacles and that the path for transporting molten metal is free from tripping hazards.
- Never overfill ladles or crucibles, as this can lead to spills and accidents. Always leave sufficient space to account for movement during transport.
-
Environmental and Workspace Safety
- Ensure proper ventilation in the workspace to prevent the buildup of harmful fumes or gases produced during the melting process.
- Keep the workspace clean and free of flammable materials. Molten metal can ignite nearby combustibles, leading to fires.
- Use barriers or shields to protect other workers and equipment from radiant heat and potential splashes.
-
Emergency Preparedness
- Have fire extinguishers and first aid kits readily available in the workspace. Ensure that all workers know their locations and how to use them.
- Train workers on emergency procedures, including how to respond to spills, burns, or fires. Regular drills can help ensure everyone is prepared for potential incidents.
- Establish clear communication protocols to quickly alert others in case of an emergency.
By following these safety precautions, workers can significantly reduce the risks associated with molten metal handling. Proper training, the use of appropriate tools and equipment, and adherence to safety protocols are essential for creating a safe and efficient working environment.
Summary Table:
Category | Key Safety Precautions |
---|---|
Proper Tools | Use high-temperature-resistant tools like ladles, crucibles, and tongs. Inspect for damage. |
Personal Protective Equipment (PPE) | Wear heat-resistant gloves, aprons, face shields, safety goggles, and flame-resistant clothing. |
Handling and Pouring | Pour slowly, avoid overfilling, and ensure a clear workspace to prevent spills and splashes. |
Workspace Safety | Maintain proper ventilation, remove flammable materials, and use barriers for protection. |
Emergency Preparedness | Keep fire extinguishers and first aid kits accessible. Train workers on emergency procedures. |
Ensure your molten metal operations are safe and efficient—contact our experts today for tailored safety solutions!