Chemical vapor deposition (CVD) is a widely used process for depositing thin films of materials onto substrates. It involves a series of steps that transform gaseous precursors into solid films through chemical reactions. The process is highly valued for its ability to produce high-quality, pure, and durable coatings. The steps in CVD can be broadly categorized into three main stages: precursor delivery and vaporization, chemical reaction and decomposition, and film deposition and byproduct removal. Each stage is critical to ensuring the formation of a uniform and high-quality film. Below, the key steps and their significance in the CVD process are explained in detail.
Key Points Explained:
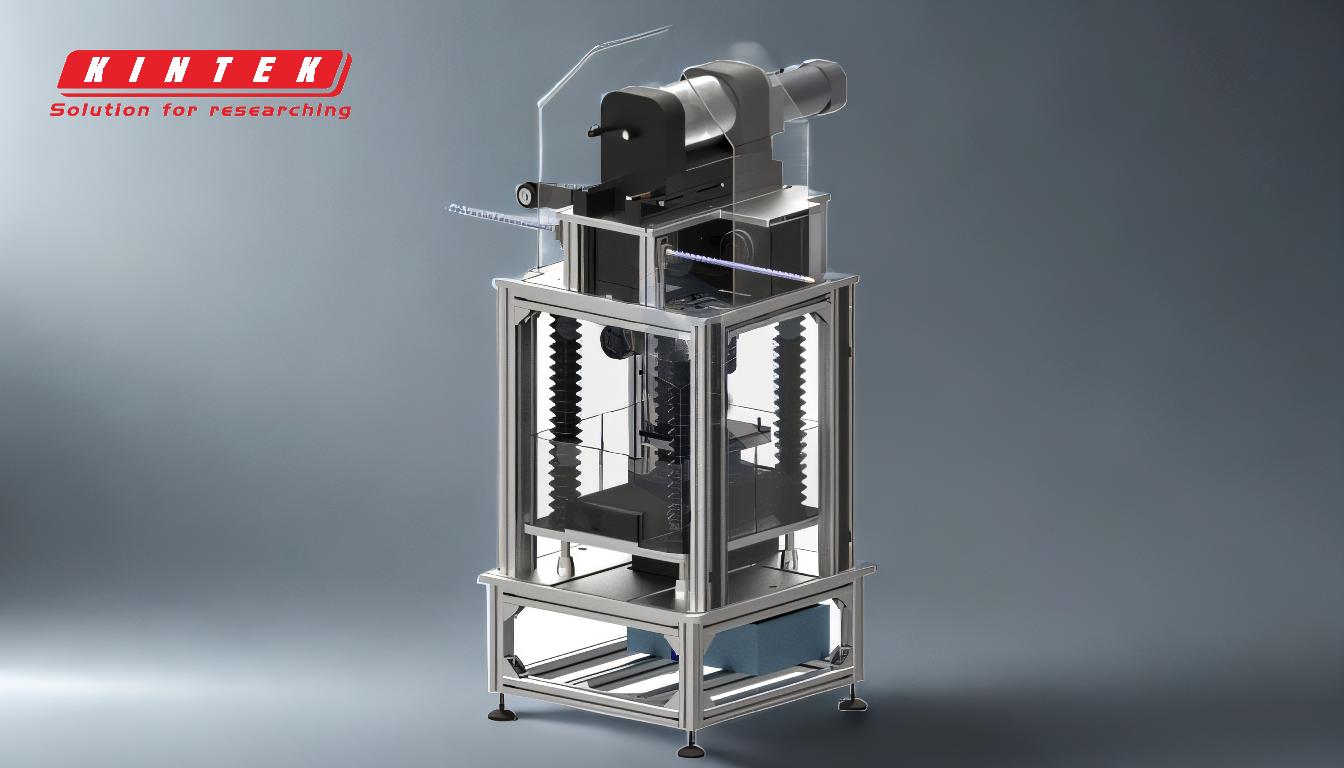
-
Precursor Delivery and Vaporization
- The first step in CVD involves the delivery of volatile precursor compounds to the reaction chamber. These precursors are typically in a gaseous or vapor state.
- The precursors are often mixed with carrier gases to facilitate their transport to the substrate surface.
- The vaporization of these compounds is crucial, as it ensures that the reactants are in a form that can easily interact with the substrate.
- This step sets the foundation for the subsequent chemical reactions by providing the necessary reactants in a controlled manner.
-
Transport of Reacting Species to the Substrate Surface
- Once vaporized, the gaseous species are transported to the substrate surface. This transport is influenced by factors such as gas flow rates, pressure, and temperature within the reaction chamber.
- Proper transport ensures that the reactants reach the substrate uniformly, which is essential for achieving a consistent film thickness.
- This step also involves the diffusion of the gaseous species through the boundary layer near the substrate surface, which can affect the deposition rate.
-
Adsorption of Reacting Species on the Substrate Surface
- Upon reaching the substrate, the gaseous species adsorb onto its surface. Adsorption is a critical step as it determines the availability of reactants for the subsequent chemical reactions.
- The adsorption process can be influenced by the substrate's surface properties, such as roughness and chemical composition, as well as the temperature and pressure conditions.
- Effective adsorption ensures that the reactants are in close proximity to the substrate, facilitating the formation of the desired film.
-
Chemical Reaction and Decomposition
- The adsorbed species undergo chemical reactions, which may involve thermal decomposition or interactions with other gases, vapors, or liquids present in the reaction chamber.
- These reactions break down the precursor molecules into atoms or smaller molecules, which then form the building blocks of the thin film.
- The chemical reactions are often surface-catalyzed, meaning they are facilitated by the substrate's surface properties.
- This step is critical for determining the composition, structure, and properties of the deposited film.
-
Nucleation and Growth of the Film
- After the chemical reactions, the resulting atoms or molecules nucleate on the substrate surface, forming small clusters that grow into a continuous film.
- Nucleation is influenced by factors such as surface energy, temperature, and the concentration of reacting species.
- The growth of the film proceeds as more atoms or molecules are deposited, leading to the formation of a uniform and dense coating.
- This step determines the final quality, thickness, and morphology of the deposited film.
-
Desorption of Byproducts and Their Removal
- As the chemical reactions proceed, gaseous byproducts are often generated. These byproducts must be desorbed from the substrate surface and transported away from the reaction zone.
- Efficient removal of byproducts is essential to prevent contamination of the film and ensure the purity of the deposited material.
- The desorption process is influenced by the reaction conditions, such as temperature and pressure, as well as the flow dynamics within the reaction chamber.
- Proper management of byproducts is crucial for maintaining the quality and reproducibility of the CVD process.
-
Control of Process Parameters
- Throughout the CVD process, various parameters such as temperature, pressure, gas flow rates, and precursor concentrations must be carefully controlled.
- These parameters influence the rate of deposition, the uniformity of the film, and its final properties.
- Advanced CVD systems often incorporate real-time monitoring and feedback mechanisms to ensure precise control over these parameters.
- Proper control is essential for achieving high-quality films with desired characteristics, such as thickness, density, and stoichiometry.
By following these steps, the CVD process enables the deposition of high-quality thin films with excellent purity, hardness, and resistance to damage. The ability to control each step precisely makes CVD a versatile and reliable method for producing a wide range of materials, including advanced coatings and nanomaterials like graphene.
Summary Table:
Step | Description |
---|---|
1. Precursor Delivery and Vaporization | Volatile precursors are delivered and vaporized, mixed with carrier gases for transport. |
2. Transport to Substrate | Gaseous species are transported to the substrate surface, influenced by flow rates and temperature. |
3. Adsorption on Substrate | Reacting species adsorb onto the substrate, influenced by surface properties and conditions. |
4. Chemical Reaction | Adsorbed species undergo thermal decomposition or reactions to form film-building blocks. |
5. Nucleation and Growth | Atoms or molecules nucleate and grow into a continuous, uniform film. |
6. Desorption of Byproducts | Gaseous byproducts are removed to ensure film purity and prevent contamination. |
7. Control of Process Parameters | Temperature, pressure, and gas flow rates are controlled for precise film properties. |
Discover how CVD can revolutionize your material coatings—contact our experts today to learn more!