The PVD (Physical Vapor Deposition) coating process is a sophisticated method used to apply thin, durable, and high-performance coatings to various substrates. It involves a series of well-defined steps that ensure the coating adheres strongly to the substrate, providing enhanced properties such as improved hardness, oxidation resistance, and reduced friction. The process is conducted under vacuum conditions, making it environmentally friendly and precise. The key steps include cleaning the substrate, vaporizing the target material, transporting the vaporized atoms, reacting them with gases if necessary, and depositing them onto the substrate. Each step is critical to achieving a uniform, high-quality coating.
Key Points Explained:
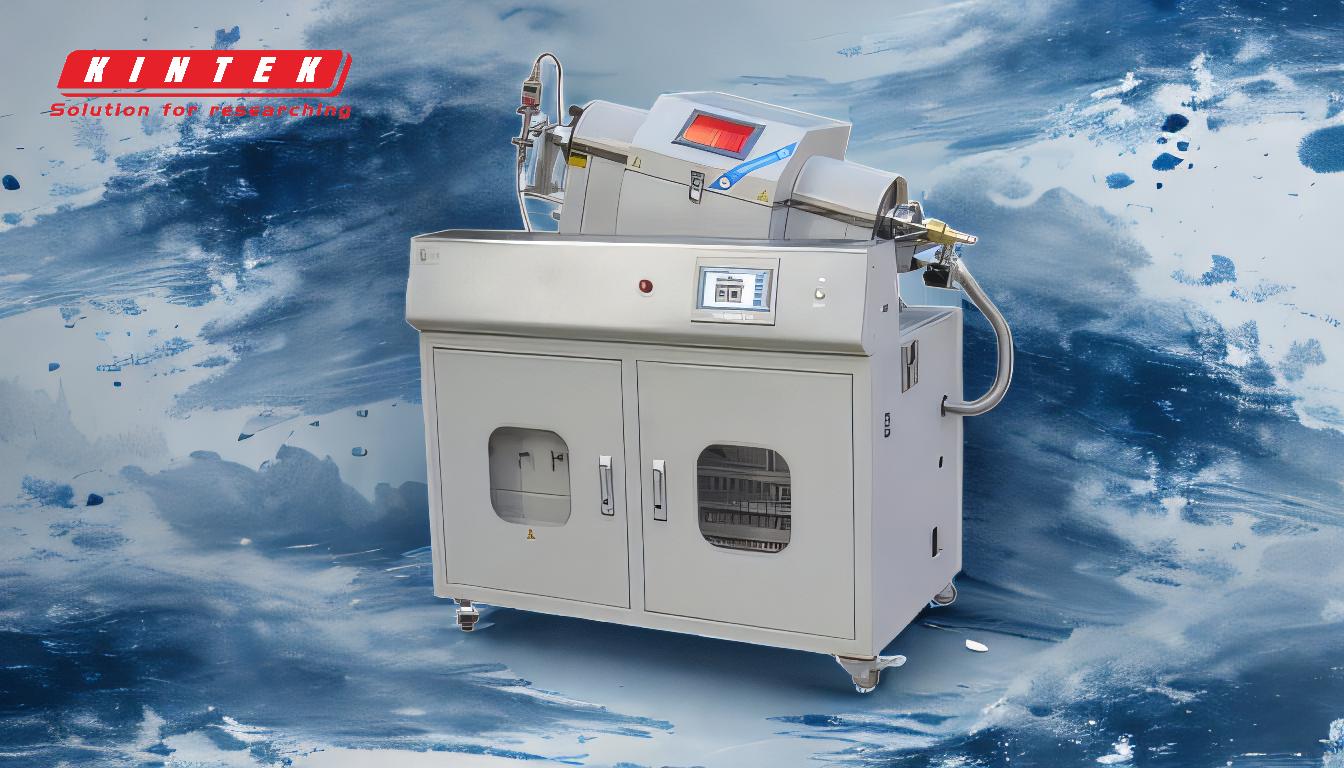
-
Substrate Cleaning:
- The first step in the PVD coating process is thoroughly cleaning the substrate. This is crucial to remove any contaminants, such as oils, dust, or oxides, that could interfere with the adhesion of the coating. A clean surface ensures a strong bond between the substrate and the coating, which is essential for the durability and performance of the final product.
-
Vaporization of the Target Material:
- In this step, the target material (usually a metal or ceramic) is vaporized. This is achieved by creating an electrical arc in a vacuum chamber or by bombarding the target with a beam of electrons. The energy from the arc or electron beam causes the target material to release atoms, which then enter the vapor phase. This process is known as ablation.
-
Transport of Vaporized Atoms:
- Once the target material is vaporized, the atoms are transported through the vacuum chamber to the substrate. This transportation occurs in a controlled environment to ensure that the atoms reach the substrate uniformly. The vacuum conditions prevent contamination and allow for precise control over the deposition process.
-
Reaction with Gases (if applicable):
- Depending on the desired coating properties, the vaporized atoms may react with gases introduced into the chamber. For example, oxygen or nitrogen can be used to form metal oxides or nitrides, respectively. This reaction step is crucial for creating coatings with specific chemical compositions and properties, such as enhanced hardness or corrosion resistance.
-
Deposition onto the Substrate:
- The final step is the deposition of the vaporized atoms onto the substrate. This occurs atom by atom, resulting in a very thin and uniform coating. The substrate may be rotated or moved to ensure even coverage. The thickness of the coating can range from a few atoms to several microns, depending on the application. Tools like a quartz crystal microbalance are often used to monitor the deposition rate and ensure consistency.
-
Quality Control and Testing:
- After the coating process, each batch of coated components undergoes rigorous testing to ensure consistency and quality. Techniques such as X-ray fluorescence (XRF) and spectrophotometry are used to determine the composition, thickness, and color of the coating. This step is essential to verify that the coating meets the required specifications and performance standards.
The PVD coating process is a highly controlled and precise method that results in coatings with superior properties. Each step, from cleaning to deposition, plays a critical role in ensuring the final product's quality and performance.
Summary Table:
Step | Description |
---|---|
Substrate Cleaning | Remove contaminants to ensure strong coating adhesion. |
Vaporization | Vaporize target material using electrical arcs or electron beams. |
Atom Transport | Transport vaporized atoms in a vacuum to the substrate. |
Reaction with Gases | React atoms with gases (e.g., oxygen, nitrogen) for desired properties. |
Deposition | Deposit atoms onto the substrate for a thin, uniform coating. |
Quality Control | Test coatings for composition, thickness, and performance standards. |
Discover how PVD coating can enhance your products—contact our experts today for more details!