The sieving test is a systematic process used to determine the particle size distribution of granular materials. It involves several critical steps, including sampling, preparation, sieving, data collection, and equipment maintenance. Each step must be executed with precision to ensure accurate and reproducible results. Below is a detailed breakdown of the key steps involved in a sieving test, along with explanations of their importance and execution.
Key Points Explained:
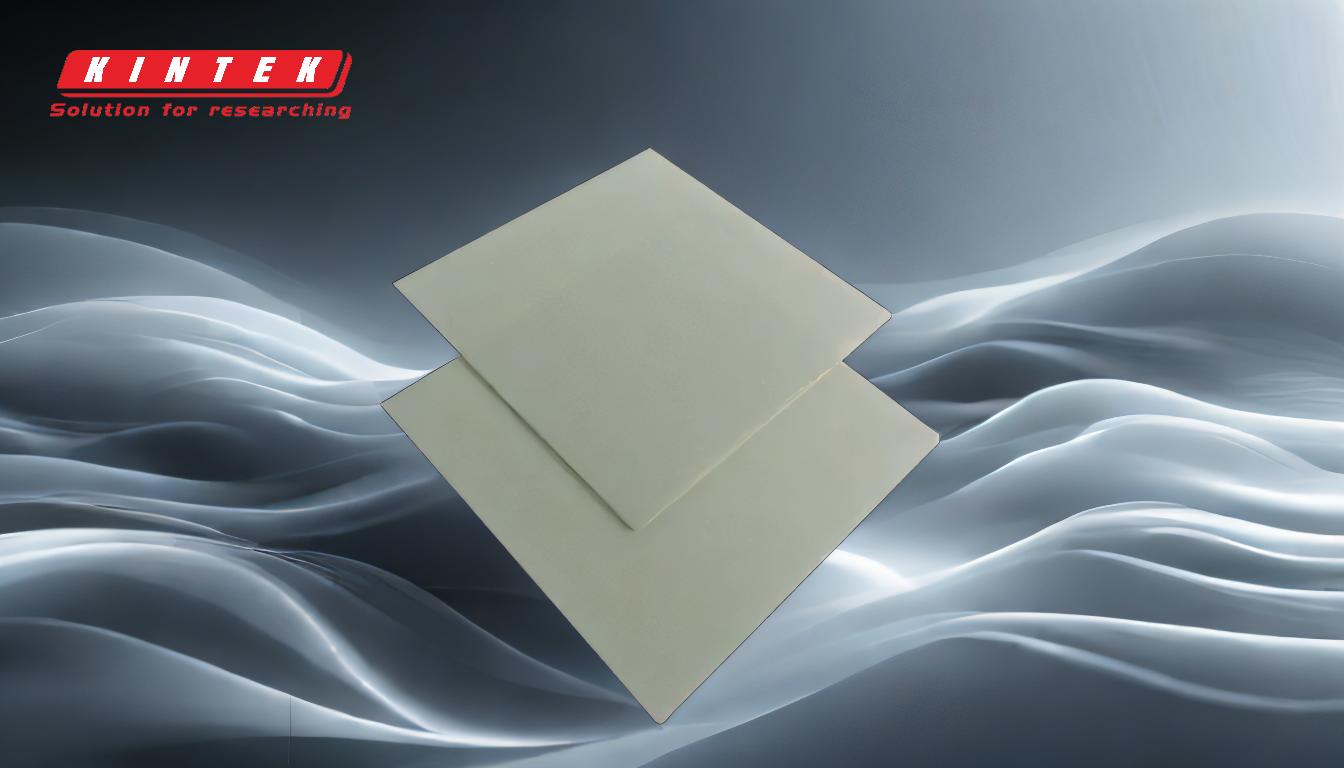
-
Sampling
- Purpose: To obtain a representative sample of the material being tested.
- Process: A sample is collected from the bulk material in a way that ensures it accurately reflects the entire batch. This may involve random sampling or using a sample divider to reduce larger quantities.
- Importance: Inaccurate sampling can lead to skewed results, making the entire analysis unreliable.
-
Sample Division (if required)
- Purpose: To reduce the sample size for testing while maintaining its representativeness.
- Process: Tools like a sample splitter or quartering method are used to divide the sample into smaller, manageable portions.
- Importance: Ensures that the sample size is appropriate for the sieves and equipment being used.
-
Selection of Suitable Test Sieves
- Purpose: To choose sieves with appropriate mesh sizes for the material being analyzed.
- Process: Sieves are selected based on the expected particle size distribution of the material. A stack of sieves with progressively smaller mesh sizes is prepared.
- Importance: Using the wrong sieve sizes can result in inaccurate particle size distribution data.
-
Selection of Sieving Parameters
- Purpose: To define the conditions under which the sieving will occur.
- Process: Parameters such as sieving time, amplitude (for mechanical shakers), and sample size are determined.
- Importance: Consistent parameters ensure reproducibility and comparability of results.
-
Actual Sieve Analysis
- Purpose: To separate the sample into different size fractions.
- Process: The sample is placed on the top sieve of the stack, and the stack is shaken either manually or using a mechanical sieve shaker. Particles pass through the sieves according to their size.
- Importance: This step directly determines the particle size distribution of the material.
-
Recovery of Sample Material
- Purpose: To collect and weigh the material retained on each sieve.
- Process: After sieving, the material on each sieve is carefully transferred to a weighing pan and weighed.
- Importance: Accurate weighing is critical for calculating the percentage of material in each size fraction.
-
Data Evaluation
- Purpose: To analyze and interpret the results of the sieve analysis.
- Process: The mass of material retained on each sieve is recorded, and the percentage retained is calculated. A cumulative percentage passing or retained is often plotted to visualize the particle size distribution.
- Importance: Proper data evaluation provides insights into the material's properties and suitability for specific applications.
-
Cleaning and Drying the Test Sieves
- Purpose: To maintain the accuracy and longevity of the sieves.
- Process: After use, sieves are cleaned by gently brushing the mesh, washing with warm water and mild detergent, and allowing them to dry completely before reuse.
- Importance: Dirty or clogged sieves can lead to inaccurate results and reduce the lifespan of the equipment.
Additional Considerations:
- Preparation of Sieves: Before use, sieves should be weighed empty (tare weight) to ensure accurate measurements of the retained material.
- Method Development: Selecting an appropriate standard method (e.g., ASTM or ISO) ensures consistency and compliance with industry standards.
- Sample Preparation: Pre-drying or conditioning the sample may be necessary to remove moisture or other factors that could affect the results.
- Result Interpretation: The final data should be analyzed in the context of the material's intended use, such as quality control in manufacturing or research applications.
By following these steps meticulously, the sieving test provides reliable and actionable data about the particle size distribution of granular materials, which is essential for quality control, research, and industrial applications.
Summary Table:
Step | Purpose | Importance |
---|---|---|
Sampling | Obtain a representative sample of the material. | Ensures the sample reflects the entire batch for reliable results. |
Sample Division | Reduce sample size while maintaining representativeness. | Prepares an appropriate sample size for sieving. |
Selection of Test Sieves | Choose sieves with suitable mesh sizes. | Prevents inaccurate particle size distribution data. |
Sieving Parameters | Define sieving conditions (time, amplitude, sample size). | Ensures reproducibility and comparability of results. |
Sieve Analysis | Separate the sample into size fractions. | Determines the particle size distribution directly. |
Recovery of Material | Collect and weigh material retained on each sieve. | Critical for calculating percentage distribution. |
Data Evaluation | Analyze and interpret sieving results. | Provides insights into material properties and suitability. |
Cleaning and Drying | Maintain sieve accuracy and longevity. | Prevents inaccurate results and extends equipment lifespan. |
Need help with sieving tests or particle size analysis? Contact our experts today for tailored solutions!