Thin film deposition is a critical process in various industries, including electronics, optics, and coatings. It involves several sequential steps to achieve a high-quality thin film with desired properties. The process typically includes selecting a pure material source, preparing the substrate, transporting the material to the substrate, depositing the material to form a thin film, and optionally treating or analyzing the film. These steps ensure the film adheres well, has the correct thickness, and meets specific performance criteria. Below, the key steps are explained in detail.
Key Points Explained:
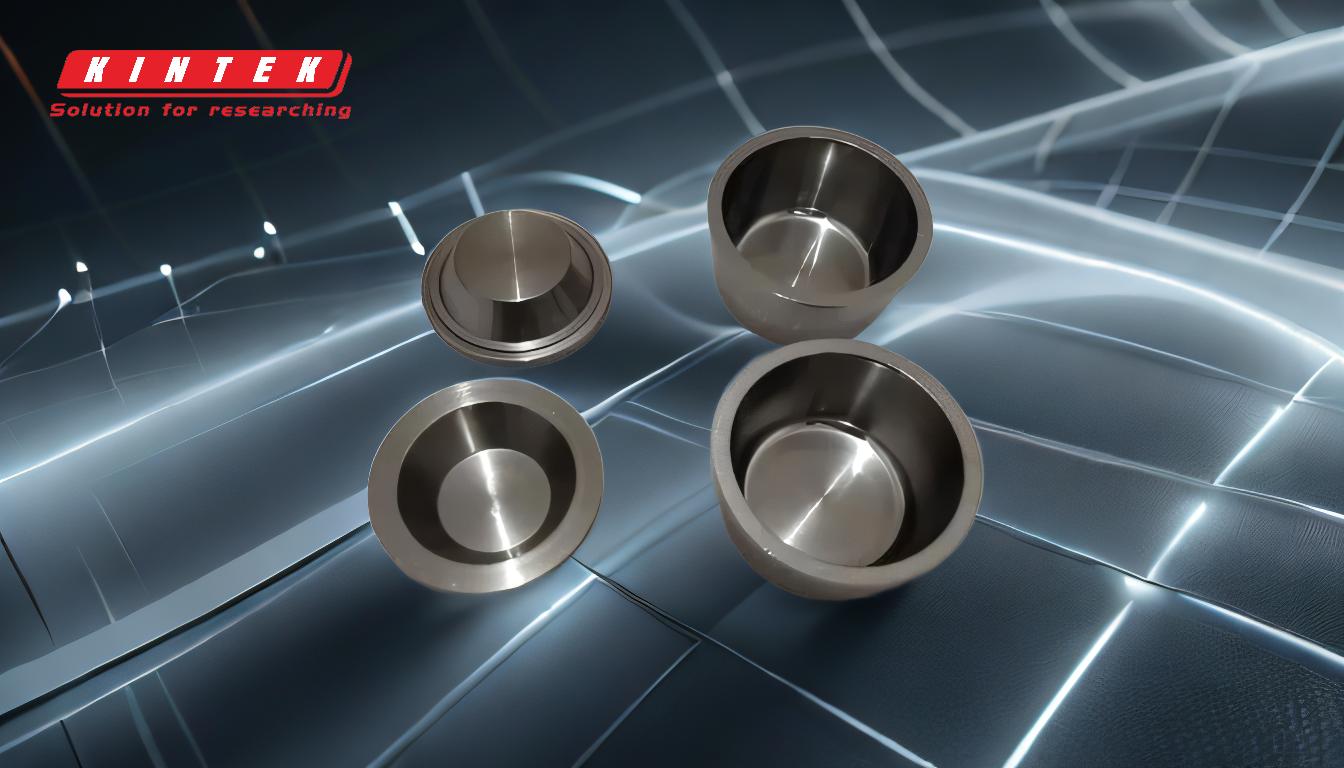
-
Selection of the Pure Material Source (Target)
- The first step involves choosing a high-purity material, known as the target, which will form the thin film.
- The material is selected based on the desired properties of the film, such as conductivity, transparency, or durability.
- Common materials include metals, semiconductors, and ceramics.
- The purity of the target is crucial, as impurities can negatively affect the film's properties.
-
Preparation of the Substrate
- The substrate is the surface on which the thin film will be deposited.
- It must be thoroughly cleaned to remove contaminants like dust, oils, or oxides, which can interfere with adhesion.
- Cleaning methods include ultrasonic cleaning, chemical etching, or plasma treatment.
- In some cases, the substrate may also be treated to improve adhesion or modify surface properties.
-
Transporting the Material to the Substrate
- The target material is transported to the substrate through a medium, which can be a fluid or a vacuum.
- In vacuum-based methods (e.g., Physical Vapour Deposition or PVD), the material is evaporated or sputtered in a vacuum chamber to prevent contamination.
- In fluid-based methods (e.g., Chemical Vapour Deposition or CVD), the material is transported as a gas or liquid precursor.
-
Deposition of the Thin Film
- The target material is deposited onto the substrate to form a thin film.
- The deposition method depends on the technique used:
- PVD: The material is evaporated or sputtered and then condenses on the substrate.
- CVD: A chemical reaction occurs on the substrate surface, depositing the material.
- Atomic Layer Deposition (ALD): The film is built one atomic layer at a time, ensuring precise thickness control.
- Spray Pyrolysis: A solution containing the material is sprayed onto the substrate and thermally decomposed to form a film.
- The deposition conditions (e.g., temperature, pressure, and time) are carefully controlled to achieve the desired film properties.
-
Optional Annealing or Heat Treatment
- After deposition, the thin film may undergo annealing or heat treatment to improve its properties.
- Annealing can enhance adhesion, reduce stress, or modify the film's microstructure.
- This step is particularly important for films requiring high durability or specific electrical properties.
-
Analysis and Modification of the Deposition Process
- The final step involves analyzing the thin film to ensure it meets the required specifications.
- Techniques like X-ray diffraction (XRD), scanning electron microscopy (SEM), or atomic force microscopy (AFM) are used to evaluate properties such as thickness, uniformity, and composition.
- If the film does not meet the desired criteria, the deposition process may be modified by adjusting parameters like temperature, pressure, or deposition rate.
By following these steps, manufacturers can produce thin films with precise properties tailored to specific applications. Each step is critical and must be carefully controlled to ensure the final product meets the required standards.
Summary Table:
Step | Description |
---|---|
1. Selection of Material | Choose a high-purity target material (e.g., metals, semiconductors, ceramics). |
2. Substrate Preparation | Clean and treat the substrate to ensure proper adhesion and surface properties. |
3. Material Transport | Transport the material via vacuum (PVD) or fluid-based (CVD) methods. |
4. Thin Film Deposition | Use PVD, CVD, ALD, or spray pyrolysis to deposit the film. |
5. Optional Heat Treatment | Anneal the film to enhance adhesion, reduce stress, or modify microstructure. |
6. Analysis & Modification | Analyze the film using XRD, SEM, or AFM; adjust deposition parameters if needed. |
Need help optimizing your thin film deposition process? Contact our experts today for tailored solutions!