Sputtering is a widely used thin film deposition process in industries such as semiconductors, optical devices, and solar panels. It involves ejecting atoms from a target material onto a substrate through bombardment by high-energy particles in a vacuum chamber. The process typically includes steps such as creating a vacuum, introducing an inert gas, ionizing the gas to form a plasma, and depositing the target material onto the substrate. This method ensures precise and uniform thin film coatings, making it essential for advanced manufacturing processes.
Key Points Explained:
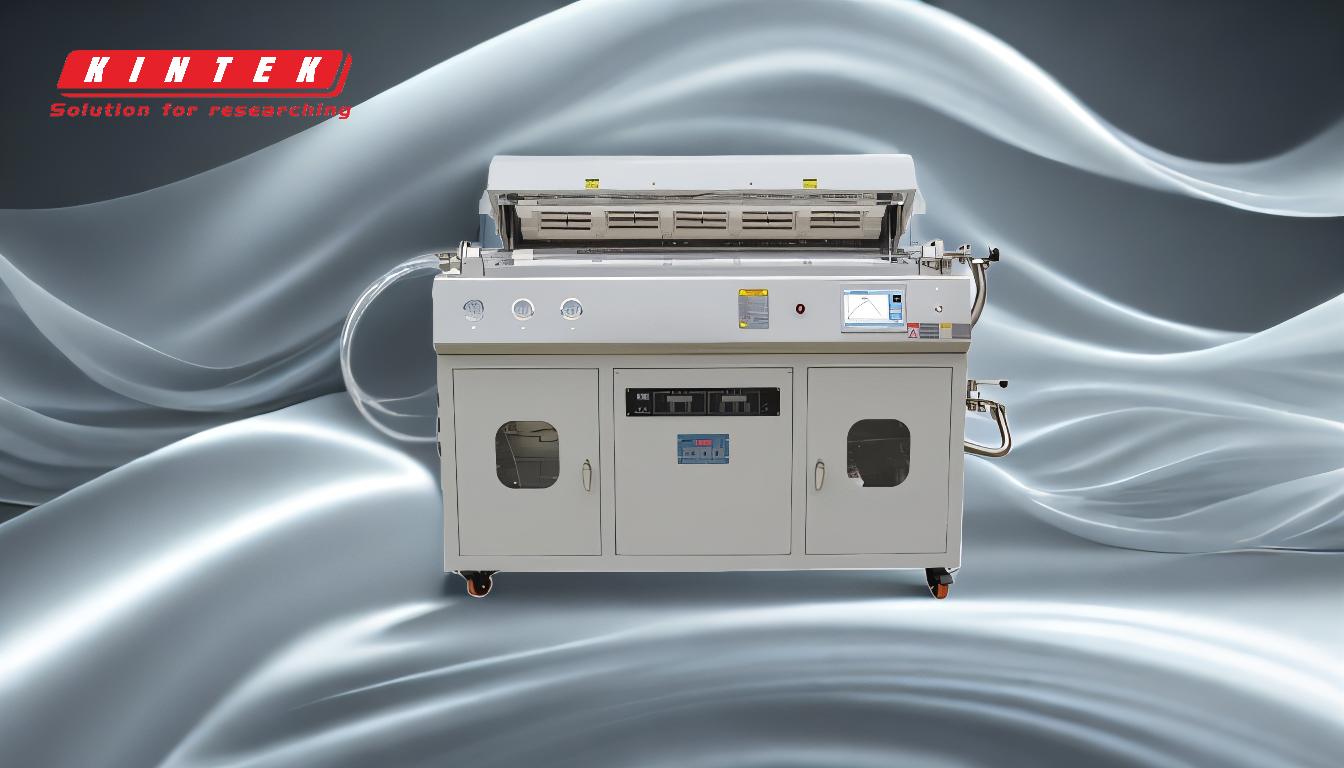
-
Preparation of the Vacuum Chamber:
- The first step in sputtering is to create a vacuum inside the reaction chamber. This involves dropping the internal pressure to around 1 Pa to remove moisture and impurities. A vacuum environment is crucial to prevent contamination and ensure the purity of the deposited film.
-
Introduction of Inert Gas:
- Once the vacuum is established, an inert gas, typically argon, is pumped into the chamber. Argon is preferred because it is chemically inert and does not react with the target material or the substrate. The gas creates a low-pressure atmosphere necessary for plasma formation.
-
Heating the Chamber:
- The chamber is heated to temperatures ranging from 150°C to 750°C. Heating helps in achieving better adhesion of the deposited film to the substrate and can also influence the microstructure of the film.
-
Creation of Plasma:
- A high voltage is applied to ionize the argon atoms, creating a plasma. In processes like RF sputtering, radio waves are used to ionize the gas. The plasma consists of positively charged argon ions and free electrons.
-
Bombardment of the Target Material:
- The target material, which acts as the cathode, is negatively charged. This attracts the positively charged argon ions from the plasma. When these high-energy ions collide with the target, they dislodge atoms or molecules from the target material.
-
Deposition onto the Substrate:
- The dislodged target atoms or molecules form a vapor stream that travels through the vacuum chamber and deposits onto the substrate, which acts as the anode. This results in the formation of a thin film or coating on the substrate.
-
Ramp Down and Cooling:
- After the deposition process, the chamber is gradually cooled down to room temperature, and the pressure is returned to ambient levels. This step ensures the stability and integrity of the deposited film.
-
Optional Post-Deposition Treatments:
- Depending on the application, the deposited film may undergo additional treatments such as annealing or heat treatment to enhance its properties. The film's properties are then analyzed to ensure they meet the required specifications.
By following these steps, sputtering provides a controlled and precise method for depositing thin films, making it indispensable in various high-tech industries.
Summary Table:
Step | Description |
---|---|
1. Preparation of the Vacuum Chamber | Create a vacuum (≈1 Pa) to remove impurities and ensure film purity. |
2. Introduction of Inert Gas | Pump inert gas (e.g., argon) into the chamber for plasma formation. |
3. Heating the Chamber | Heat chamber (150°C–750°C) to improve film adhesion and microstructure. |
4. Creation of Plasma | Apply high voltage or RF to ionize gas, forming a plasma. |
5. Bombardment of the Target Material | Argon ions collide with the target, dislodging atoms/molecules. |
6. Deposition onto the Substrate | Dislodged atoms form a vapor stream, depositing onto the substrate. |
7. Ramp Down and Cooling | Gradually cool the chamber to stabilize the deposited film. |
8. Optional Post-Deposition Treatments | Apply annealing or heat treatment to enhance film properties. |
Discover how sputtering can elevate your manufacturing process—contact our experts today!