Dip coating is a versatile and cost-effective technique used to apply thin films to substrates by immersing them into a solution and withdrawing them at a controlled speed. This method is widely used in industries such as electronics, optics, and biomedical devices due to its simplicity and reproducibility. The process involves several key steps, including immersion, withdrawal, drying, and curing, which influence the quality and thickness of the coating. By adjusting parameters such as withdrawal speed, solution viscosity, and environmental conditions, one can achieve coatings with specific properties tailored to various applications. Below, we explore the techniques of dip coating in detail, focusing on its process, influencing factors, and applications.
Key Points Explained:
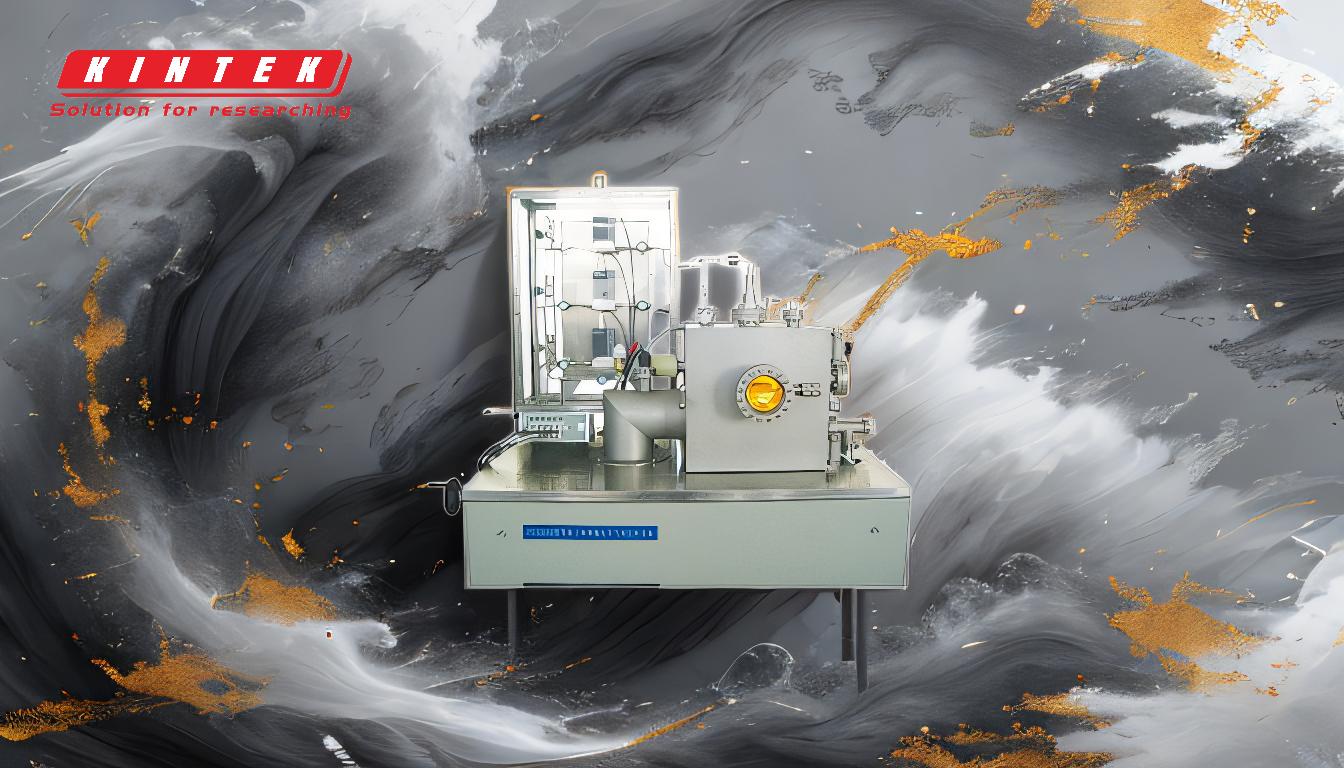
-
Overview of Dip Coating Process:
- Immersion: The substrate is immersed into a solution containing the coating material, such as hydrolysable metal compounds or nanoparticles.
- Withdrawal: The substrate is withdrawn at a constant speed, allowing a thin liquid film to form on its surface.
- Drying and Curing: The coated substrate is exposed to an atmosphere containing water vapor or other curing agents to solidify the film.
-
Key Parameters Influencing Dip Coating:
- Withdrawal Speed: The speed at which the substrate is withdrawn directly affects the thickness of the coating. Higher speeds result in thicker films, while lower speeds produce thinner layers.
- Solution Viscosity: The viscosity of the coating solution determines its flow behavior and film uniformity. Solutions with higher viscosity tend to form thicker and more uniform coatings.
- Environmental Conditions: Factors such as temperature, humidity, and air flow during drying and curing can significantly impact the final coating quality.
- Substrate Surface Properties: The wettability and roughness of the substrate influence the adhesion and uniformity of the coating.
-
Advantages of Dip Coating:
- Cost-Effectiveness: Dip coating requires minimal equipment and is relatively inexpensive compared to other coating methods like PVD or CVD.
- Versatility: It can be used with a wide range of materials, including polymers, ceramics, and metals.
- Reproducibility: The process is highly reproducible, making it suitable for large-scale production.
-
Applications of Dip Coating:
- Optical Coatings: Used to create anti-reflective, reflective, or protective layers on lenses and mirrors.
- Biomedical Devices: Applied to implants and medical instruments to enhance biocompatibility or add functional layers.
- Electronics: Used for coating sensors, displays, and other components with conductive or insulating layers.
- Energy: Applied in the fabrication of solar cells, fuel cells, and batteries to improve performance and durability.
-
Comparison with Other Coating Techniques:
- Physical Vapor Deposition (PVD): PVD involves the deposition of thin films through the condensation of vaporized material. It offers high precision but is more expensive and complex than dip coating.
- Chemical Vapor Deposition (CVD): CVD involves chemical reactions to deposit thin films. It provides excellent adhesion and uniformity but requires high temperatures and specialized equipment.
- Micro-Arc Oxidation (MAO): MAO is used for coating metals with ceramic layers. It is suitable for hard and wear-resistant coatings but is limited to conductive substrates.
- Thermal Spraying: This method involves melting and spraying materials onto a substrate. It is ideal for thick coatings but lacks the precision of dip coating.
- Sol-Gel: Similar to dip coating, sol-gel involves the formation of a gel that is converted into a solid coating. It is highly versatile but often requires additional curing steps.
-
Challenges and Considerations:
- Film Thickness Control: Achieving consistent film thickness across large or complex substrates can be challenging.
- Material Compatibility: The coating solution must be compatible with the substrate to ensure proper adhesion and performance.
- Environmental Impact: Some coating solutions may contain volatile organic compounds (VOCs) or other hazardous materials, requiring proper handling and disposal.
By understanding the techniques and factors involved in dip coating, manufacturers can optimize the process to meet specific application requirements. This method’s simplicity, versatility, and cost-effectiveness make it a popular choice for a wide range of industries.
Summary Table:
Aspect | Details |
---|---|
Process Steps | Immersion, withdrawal, drying, curing |
Key Parameters | Withdrawal speed, solution viscosity, environmental conditions, substrate |
Advantages | Cost-effective, versatile, reproducible |
Applications | Optical coatings, biomedical devices, electronics, energy |
Comparison with Others | PVD, CVD, MAO, thermal spraying, sol-gel |
Challenges | Film thickness control, material compatibility, environmental impact |
Optimize your coating process with dip coating—contact our experts today for tailored solutions!