Pyrolysis is a thermal decomposition process that occurs in the absence of oxygen, breaking down organic materials into smaller molecules. The process is divided into distinct temperature stages, each characterized by specific physical and chemical transformations. These stages include drying, pyrolysis, and condensation/collection. During drying, moisture is removed from the feedstock. In the pyrolysis stage, the material is heated to high temperatures (typically 400–800°C), leading to the breakdown of organic matter into volatile gases, liquid bio-oil, and solid char. Finally, the volatile gases are condensed into bio-oil, while solid char and syngas are collected for further use. Understanding these stages is crucial for optimizing the pyrolysis process and maximizing product yield.
Key Points Explained:
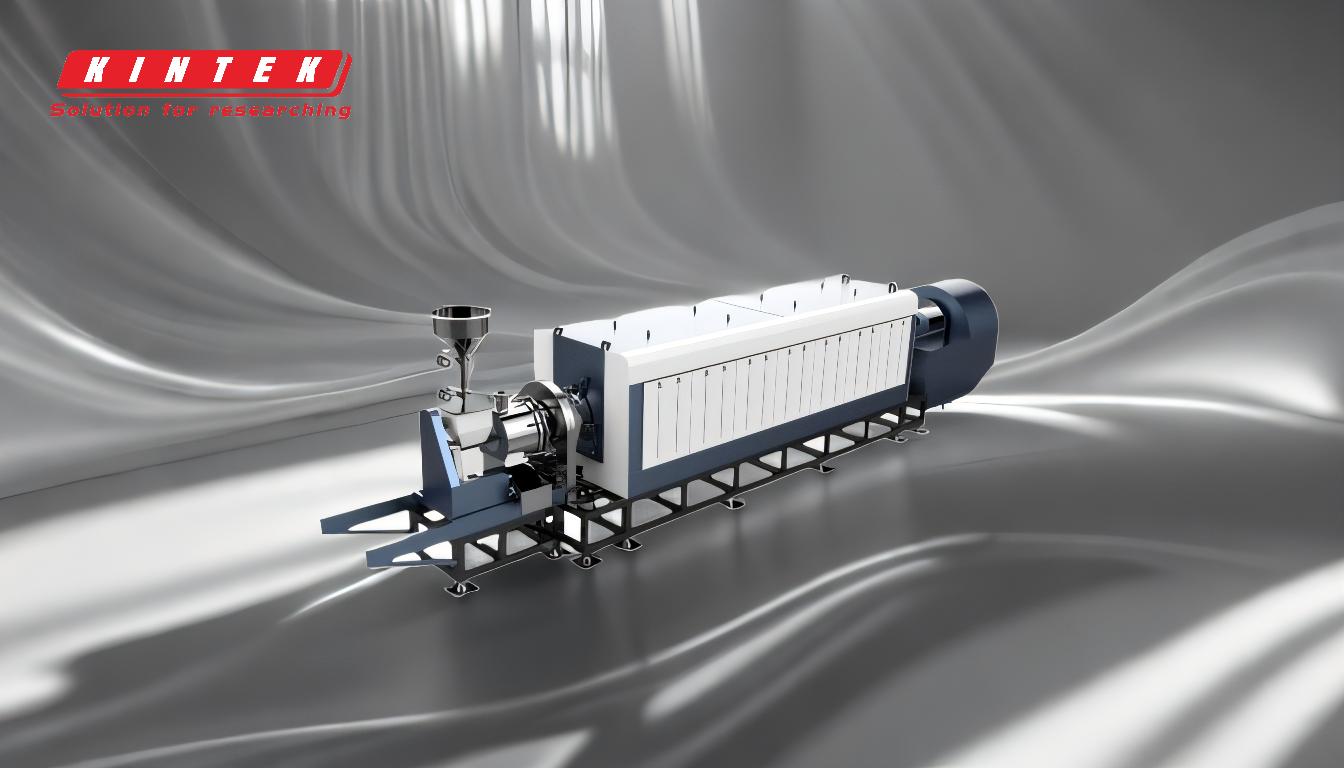
-
Drying Stage (Preparation Phase)
- Objective: Remove moisture from the feedstock to ensure efficient pyrolysis.
- Temperature Range: Typically below 200°C.
- Process: The feedstock is heated to evaporate water content, which is essential because moisture can hinder the pyrolysis reaction and reduce the quality of the end products.
- Importance: Dry feedstock ensures better thermal efficiency and prevents unwanted side reactions during the pyrolysis stage.
-
Pyrolysis Stage (Thermal Decomposition)
- Objective: Break down the organic material into volatile gases, liquid bio-oil, and solid char.
- Temperature Range: 400–800°C, depending on the feedstock and desired products.
-
Process: In the absence of oxygen, the feedstock undergoes thermal cracking, where large organic molecules are broken into smaller molecules. This stage is highly dependent on temperature:
- Low-Temperature Pyrolysis (400–500°C): Produces more biochar and less bio-oil.
- Medium-Temperature Pyrolysis (500–700°C): Balances the yield of bio-oil, syngas, and biochar.
- High-Temperature Pyrolysis (700–800°C): Favors the production of syngas and reduces biochar yield.
- Importance: The temperature directly influences the composition and yield of the end products, making it a critical parameter for process optimization.
-
Condensation and Collection Stage (Product Recovery)
- Objective: Separate and collect the pyrolysis products (bio-oil, syngas, and biochar).
- Temperature Range: Cooling from pyrolysis temperatures to ambient conditions.
-
Process:
- Volatile Gases: These are cooled and condensed into liquid bio-oil.
- Syngas: Non-condensable gases (e.g., hydrogen, methane, carbon monoxide) are collected for use as fuel or chemical feedstock.
- Biochar: Solid residue is collected and can be used as a soil amendment or for carbon sequestration.
- Importance: Efficient condensation and collection ensure high-quality products and maximize the economic viability of the pyrolysis process.
-
Factors Influencing Temperature Stages
- Feedstock Type: Different materials (e.g., wood, plastic, agricultural waste) have varying thermal properties and decomposition temperatures.
- Heating Rate: Slow heating favors biochar production, while fast heating maximizes bio-oil yield.
- Residence Time: Longer residence times at high temperatures can enhance syngas production.
- Catalyst Use: Catalysts can lower the required pyrolysis temperature and improve product selectivity.
-
Applications of Pyrolysis Products
- Bio-oil: Used as a renewable fuel or refined into chemicals.
- Syngas: Utilized for energy generation or as a precursor for synthetic fuels.
- Biochar: Applied in agriculture to improve soil health or as a carbon sequestration tool.
By understanding the temperature stages of pyrolysis, equipment and consumable purchasers can make informed decisions about the design and operation of pyrolysis systems, ensuring optimal performance and product quality.
Summary Table:
Stage | Objective | Temperature Range | Key Process | Importance |
---|---|---|---|---|
Drying | Remove moisture from feedstock | Below 200°C | Evaporate water content to ensure efficient pyrolysis | Prevents unwanted side reactions and improves thermal efficiency |
Pyrolysis | Break down organic material | 400–800°C | Thermal cracking of large molecules into volatile gases, bio-oil, and biochar | Temperature influences product composition and yield |
Condensation/Collection | Separate and collect products | Cooling to ambient | Condense gases into bio-oil; collect syngas and biochar | Ensures high-quality products and maximizes economic viability |
Ready to optimize your pyrolysis process? Contact our experts today for tailored solutions!