Silicon Carbide (SiC) is a ceramic material renowned for its exceptional thermal properties, making it ideal for high-temperature and high-stress applications. Its thermal conductivity ranges between 120-270 W/mK, which is significantly higher than many other materials, enabling efficient heat dissipation. Additionally, SiC has a low coefficient of thermal expansion (4.0x10-6/°C), contributing to its excellent thermal shock resistance. These properties allow SiC to maintain mechanical strength and structural integrity at temperatures as high as 1,400°C to 1,600°C. Its high thermal conductivity, combined with low thermal expansion, makes it suitable for applications such as semiconductor electronics, rocket nozzles, and heat exchangers. Furthermore, SiC's chemical inertness and wear resistance enhance its durability in harsh environments.
Key Points Explained:
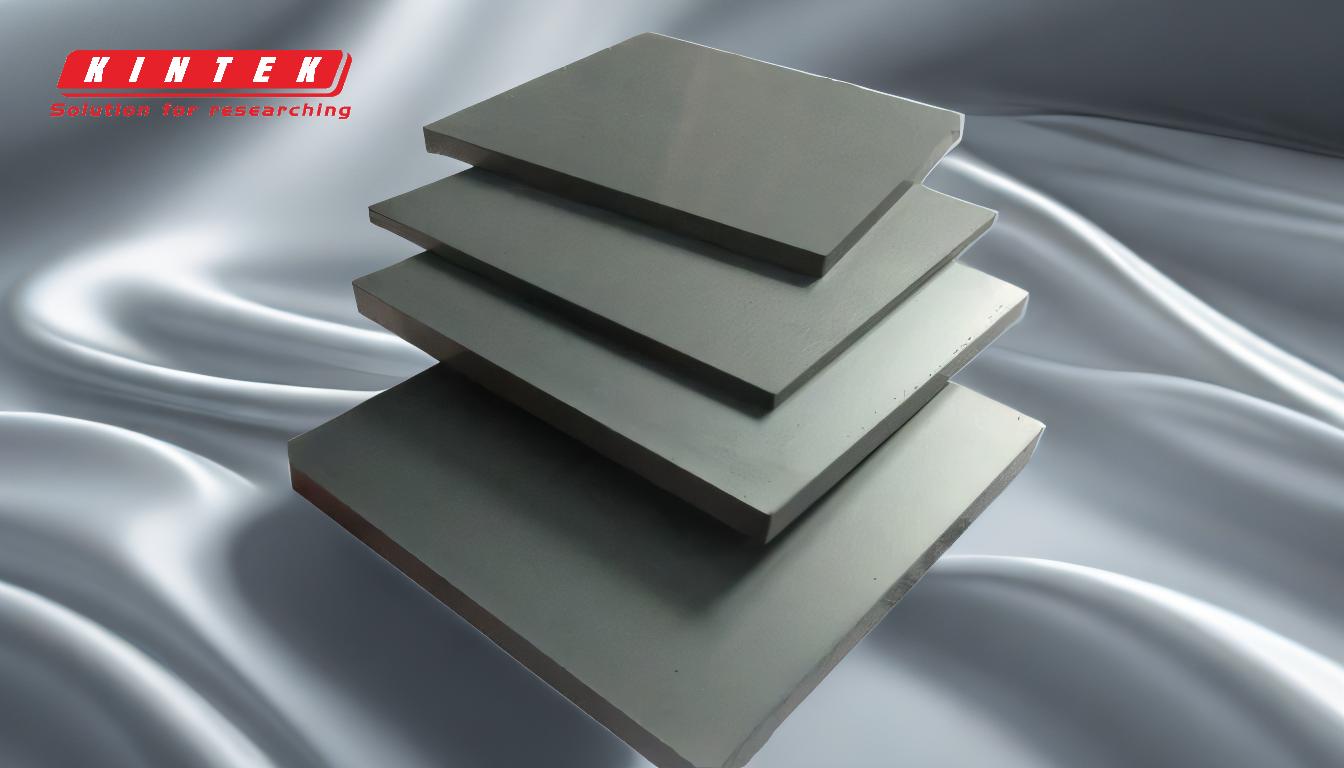
-
High Thermal Conductivity (120-270 W/mK)
- Silicon Carbide exhibits a thermal conductivity range of 120-270 W/mK, which is significantly higher than many other ceramics and semiconductor materials.
- This property ensures efficient heat transfer, making SiC suitable for applications where thermal management is critical, such as in semiconductor devices, heat exchangers, and high-power electronics.
- High thermal conductivity also contributes to its ability to withstand rapid temperature changes without cracking or degrading, which is essential for thermal shock resistance.
-
Low Coefficient of Thermal Expansion (4.0x10-6/°C)
- SiC has a low thermal expansion coefficient, meaning it expands minimally when exposed to high temperatures.
- This property reduces the risk of thermal stress and cracking, especially in applications involving rapid heating or cooling cycles.
- The low thermal expansion, combined with high thermal conductivity, enhances its thermal shock resistance, making it ideal for high-temperature environments like rocket nozzles and combustion engine valves.
-
Thermal Shock Resistance
- Thermal shock resistance is a critical property of SiC, derived from its high thermal conductivity and low thermal expansion.
- This resistance allows SiC to endure sudden temperature changes without structural damage, making it suitable for applications in extreme environments, such as aerospace and automotive industries.
- For example, SiC is used in rocket nozzles, where materials must withstand rapid temperature fluctuations during launch and re-entry.
-
High-Temperature Stability (Up to 1,400°C to 1,600°C)
- SiC maintains its mechanical strength and structural integrity at extremely high temperatures, up to 1,400°C and even approaching 1,600°C without significant strength loss.
- This property makes it a preferred material for high-temperature applications, such as heat exchangers, furnace components, and electric vehicle environments.
- Its ability to resist deformation and degradation at high temperatures ensures long-term reliability in demanding conditions.
-
Chemical Inertness and Wear Resistance
- SiC is chemically inert, meaning it resists corrosion and reactions with most chemicals, even at high temperatures.
- This property, combined with its wear resistance, makes it suitable for use in harsh chemical environments and abrasive applications.
- For instance, SiC is used in chemical processing equipment and wear-resistant components in industrial machinery.
-
Density and Stiffness
- SiC has a low density, which contributes to its lightweight nature, making it advantageous for applications where weight reduction is critical, such as in aerospace and automotive industries.
- Its high stiffness ensures dimensional stability under mechanical stress, further enhancing its performance in structural applications.
-
Electrical Conductivity
- While SiC is a ceramic, it exhibits relatively high electrical conductivity compared to other ceramics, with some forms having electrical resistance as low as one ohm cm.
- This property makes it suitable for use in semiconductor electronics and other applications where electrical conductivity is required.
-
Applications Leveraging Thermal Properties
- The combination of high thermal conductivity, low thermal expansion, and thermal shock resistance makes SiC ideal for manufacturing semiconductor electronics, rocket nozzles, heat exchangers, and combustion engine valves.
- Its ability to operate reliably in high-temperature and high-stress environments ensures its widespread use in advanced technologies, including electric vehicles and aerospace systems.
In summary, the thermal properties of Silicon Carbide, including its high thermal conductivity, low thermal expansion, and exceptional thermal shock resistance, make it a versatile and reliable material for high-temperature and high-stress applications. Its chemical inertness, wear resistance, and high-temperature stability further enhance its suitability for use in demanding environments across various industries.
Summary Table:
Property | Value/Range | Benefits |
---|---|---|
Thermal Conductivity | 120-270 W/mK | Efficient heat transfer, ideal for thermal management in electronics. |
Thermal Expansion | 4.0x10-6/°C | Minimizes thermal stress, enhances thermal shock resistance. |
Thermal Shock Resistance | High | Withstands rapid temperature changes without damage. |
High-Temperature Stability | Up to 1,400°C-1,600°C | Maintains strength and integrity in extreme heat. |
Chemical Inertness | High | Resists corrosion and chemical reactions in harsh environments. |
Wear Resistance | High | Durable in abrasive and high-stress applications. |
Density | Low | Lightweight, suitable for aerospace and automotive uses. |
Electrical Conductivity | Relatively high | Suitable for semiconductor electronics and conductive applications. |
Discover how Silicon Carbide (SiC) can enhance your high-temperature applications—contact us today for expert guidance!