Compression molding and injection molding are two popular manufacturing processes used to shape plastic and composite materials. While both methods are effective, they differ significantly in terms of process mechanics, material suitability, and production efficiency. Compression molding involves placing a preheated material into a heated mold and applying pressure to shape it, making it ideal for large, relatively simple parts. Injection molding, on the other hand, injects molten material into a mold under high pressure, allowing for intricate designs and high-volume production. The key differences lie in the complexity of parts, production speed, and material handling.
Key Points Explained:
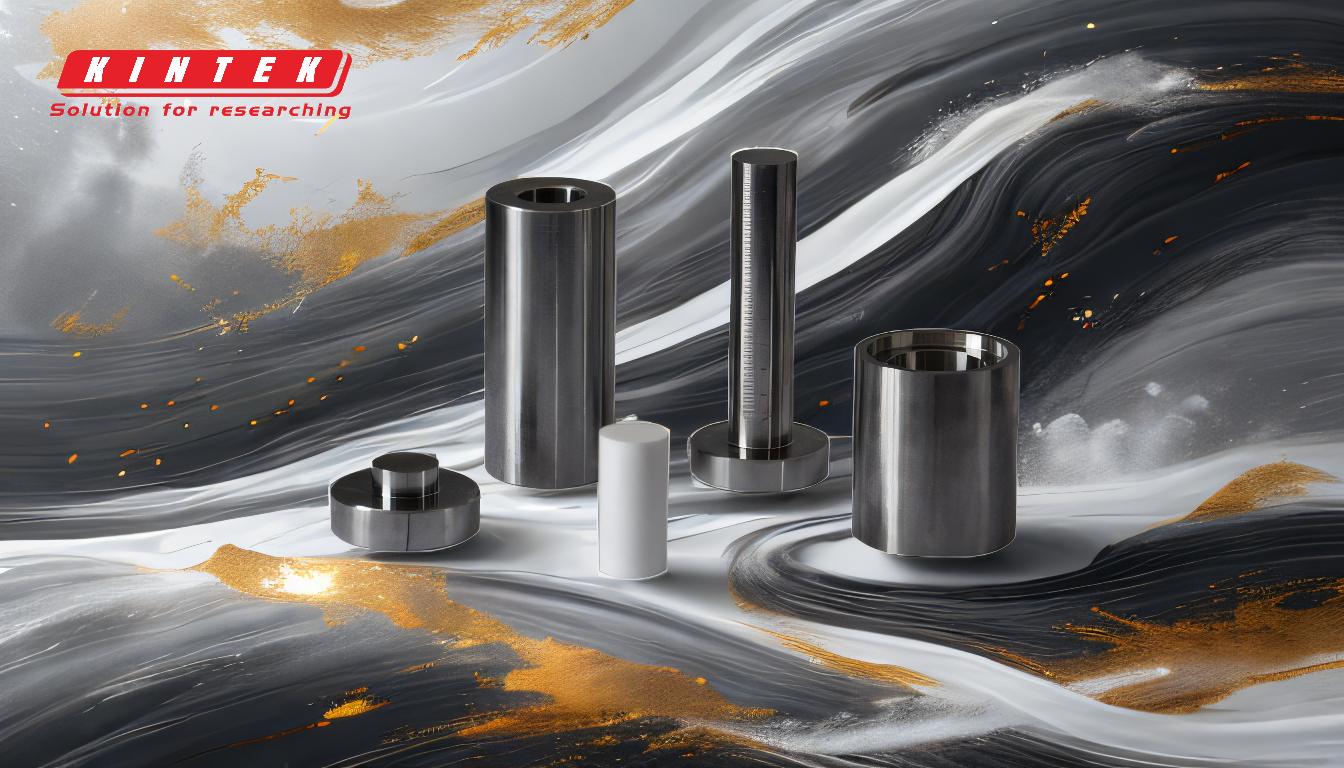
-
Process Mechanics:
- Compression Molding: In this process, a preheated material (often a thermoset polymer or composite) is placed into an open mold cavity. The mold is then closed, and pressure is applied to force the material to conform to the mold's shape. The material cures under heat and pressure, solidifying into the desired part.
- Injection Molding: This process involves heating the material (typically a thermoplastic) until it becomes molten. The molten material is then injected into a closed mold under high pressure. Once the material cools and solidifies, the mold opens, and the part is ejected. This method allows for more precise control over the material flow and is suitable for complex geometries.
-
Complexity of Parts:
- Compression Molding: Best suited for larger, simpler parts with less intricate details. The process is less effective for producing parts with complex shapes or fine features due to the limitations in material flow and pressure distribution.
- Injection Molding: Ideal for producing parts with complex geometries, thin walls, and fine details. The high-pressure injection allows the molten material to fill even the most intricate mold cavities, resulting in highly detailed and precise parts.
-
Production Speed and Efficiency:
- Compression Molding: Generally slower compared to injection molding, especially for large parts. The process involves manual or semi-automatic steps, such as placing the preheated material into the mold and applying pressure, which can increase cycle times.
- Injection Molding: Offers faster production speeds, especially for high-volume manufacturing. The process is highly automated, with machines capable of producing thousands of parts per hour. This makes injection molding more efficient for large-scale production runs.
-
Material Suitability:
- Compression Molding: Primarily used for thermoset materials, which cannot be remelted once cured. It is also suitable for certain composites and rubber materials. The process is less versatile when it comes to material options compared to injection molding.
- Injection Molding: Compatible with a wide range of thermoplastic materials, which can be remelted and reused. This versatility makes injection molding suitable for a broader range of applications, from consumer products to automotive components.
-
Tooling and Equipment Costs:
- Compression Molding: Typically requires less expensive tooling and equipment compared to injection molding. The molds used in compression molding are often simpler and less costly to produce, making it a more economical choice for low to medium production volumes.
- Injection Molding: Involves higher initial costs due to the need for complex molds and specialized machinery. However, the higher production speeds and efficiency can offset these costs over time, especially for high-volume manufacturing.
In summary, the choice between compression molding and injection molding depends on the specific requirements of the project, including the complexity of the parts, production volume, material type, and budget constraints. Compression molding is better suited for larger, simpler parts with lower production volumes, while injection molding excels in producing complex, detailed parts at high speeds and volumes.
Summary Table:
Aspect | Compression Molding | Injection Molding |
---|---|---|
Process Mechanics | Preheated material placed in an open mold, cured under heat and pressure. | Molten material injected into a closed mold under high pressure. |
Complexity of Parts | Best for larger, simpler parts with less intricate details. | Ideal for complex geometries, thin walls, and fine details. |
Production Speed | Slower, manual or semi-automatic steps increase cycle times. | Faster, highly automated, suitable for high-volume production. |
Material Suitability | Primarily thermoset materials; limited material versatility. | Wide range of thermoplastic materials; versatile applications. |
Tooling and Equipment | Less expensive tooling and equipment; economical for low to medium production volumes. | Higher initial costs but offset by efficiency for high-volume manufacturing. |
Need help choosing the right molding process for your project? Contact our experts today!