Semiconductor manufacturing relies heavily on deposition methods to create thin films of materials on silicon wafers. These films are essential for building the intricate structures of semiconductor devices. The three most common deposition methods used in semiconductor manufacturing are Chemical Vapor Deposition (CVD), Physical Vapor Deposition (PVD), and Atomic Layer Deposition (ALD). Each method has unique advantages and is chosen based on the specific requirements of the semiconductor device being manufactured. CVD is widely used for its versatility and ability to deposit high-quality films, PVD is valued for its precision and purity, and ALD is preferred for its atomic-level control and uniformity.
Key Points Explained:
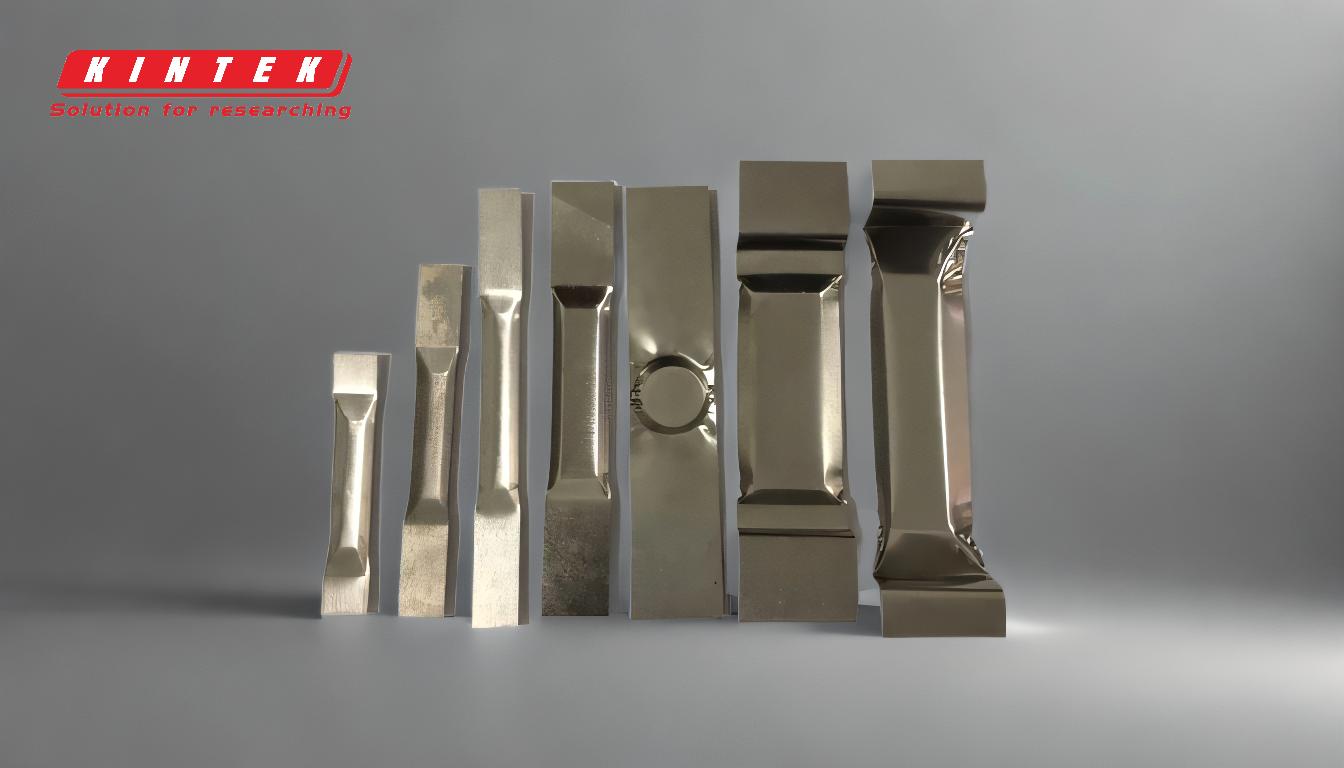
-
Chemical Vapor Deposition (CVD)
- CVD is a process where gaseous reactants are introduced into a reaction chamber, and a chemical reaction occurs on the surface of the substrate, forming a solid thin film.
- Common types of CVD include:
- Low Pressure Chemical Vapor Deposition (LPCVD): Operates at reduced pressures, producing high-quality, uniform films.
- Plasma Enhanced Chemical Vapor Deposition (PECVD): Uses plasma to enhance the chemical reaction, allowing deposition at lower temperatures.
- Atmospheric Pressure Chemical Vapor Deposition (APCVD): Operates at atmospheric pressure, suitable for high-throughput processes.
- CVD is versatile and can deposit a wide range of materials, including silicon dioxide, silicon nitride, and polysilicon.
- It is widely used in semiconductor manufacturing due to its ability to produce films with excellent step coverage and uniformity.
-
Physical Vapor Deposition (PVD)
- PVD involves the physical transfer of material from a source to the substrate, typically through processes like evaporation or sputtering.
- Common PVD methods include:
- Thermal Vapor Deposition: Material is heated until it vaporizes and then condenses on the substrate.
- Sputtering: Atoms are ejected from a target material by bombarding it with high-energy ions, which then deposit onto the substrate.
- PVD is known for producing extremely pure and uniform films with excellent adhesion to the substrate.
- It is often used for depositing metals (e.g., aluminum, copper) and alloys in semiconductor devices.
-
Atomic Layer Deposition (ALD)
- ALD is a highly controlled deposition method where materials are deposited one atomic layer at a time.
- The process involves alternating pulses of precursor gases, which react with the substrate surface in a self-limiting manner, ensuring precise thickness control.
- ALD is ideal for applications requiring ultra-thin, conformal films with exceptional uniformity, such as gate oxides in transistors.
- It is particularly useful for depositing materials on complex 3D structures, where uniformity and conformality are critical.
These three deposition methods—CVD, PVD, and ALD—are fundamental to semiconductor manufacturing, each offering unique capabilities that cater to the diverse needs of modern semiconductor devices.
Summary Table:
Deposition Method | Key Features | Common Applications |
---|---|---|
Chemical Vapor Deposition (CVD) | Versatile, high-quality films, excellent step coverage | Silicon dioxide, silicon nitride, polysilicon |
Physical Vapor Deposition (PVD) | Precision, purity, excellent adhesion | Metals (aluminum, copper), alloys |
Atomic Layer Deposition (ALD) | Atomic-level control, ultra-thin, conformal films | Gate oxides, 3D structures |
Need help choosing the right deposition method for your semiconductor project? Contact our experts today!