Spark Plasma Sintering (SPS) is a versatile and advanced sintering technology widely used in materials science and engineering. It is particularly effective for sintering metals, ceramics, and composite materials, offering advantages such as fast heating rates, short sintering times, and the ability to operate at low temperatures and high pressures. SPS is instrumental in preparing nanomaterials, bulk amorphous alloys, gradient functional materials, and high-density, fine-grained ceramics and cermets. Additionally, it is used to create transparent ceramics, such as barium strontium titanate (BST) ceramics, achieving high density and transparency. The technology's unique capabilities make it a preferred choice for producing advanced materials with tailored properties.
Key Points Explained:
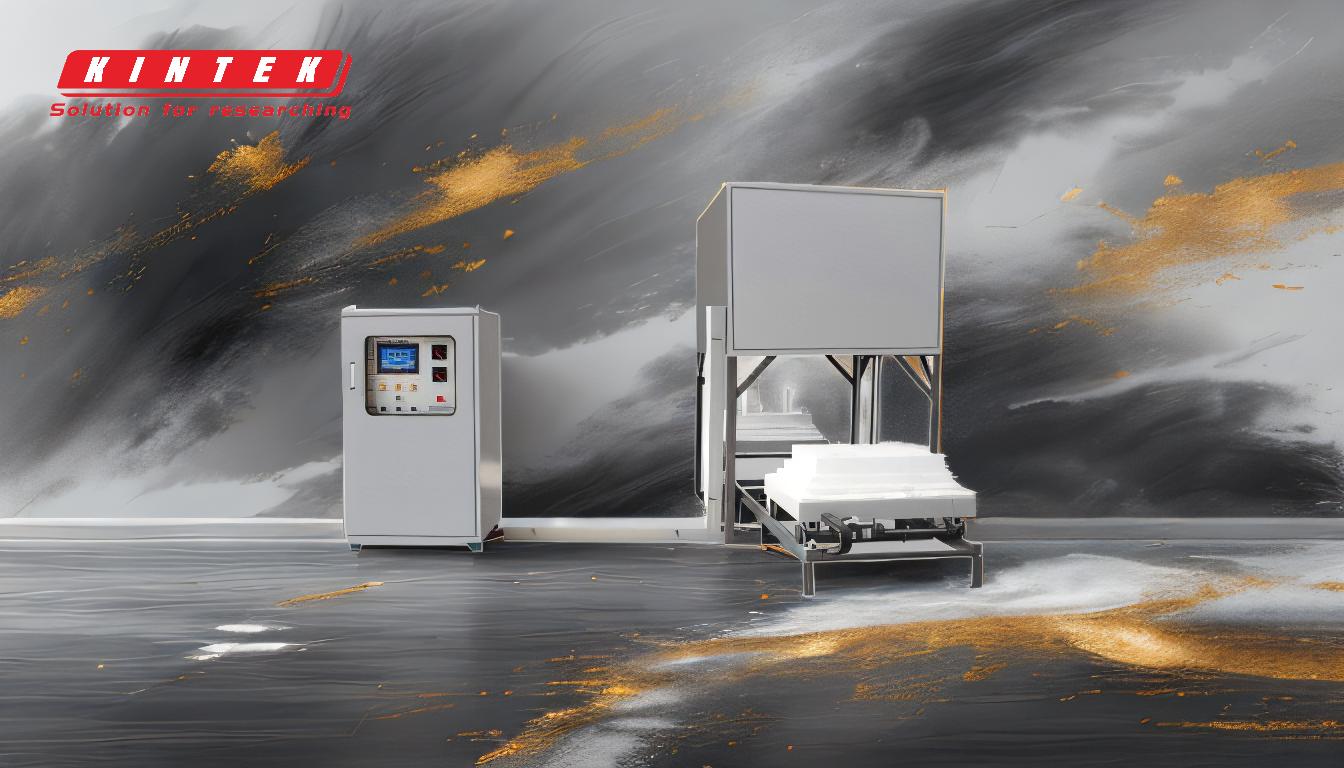
-
Sintering of Metals, Ceramics, and Composites:
- SPS is used to sinter a wide range of materials, including metals, ceramics, and composite materials. This versatility makes it a valuable tool in materials science.
- It is particularly effective for preparing high-density, fine-grained ceramics and cermets, which are essential for applications requiring high strength and durability.
-
Preparation of Nanomaterials:
- SPS is highly effective for producing nanomaterials, which have unique properties due to their small particle sizes. These materials are crucial for applications in nanotechnology, electronics, and advanced manufacturing.
-
Bulk Amorphous Alloys:
- The technology is used to prepare bulk amorphous alloys, which lack a crystalline structure and exhibit superior mechanical properties, such as high strength and corrosion resistance. These alloys are used in various high-performance applications.
-
Gradient Functional Materials:
- SPS is utilized to create gradient functional materials, which have varying properties across their structure. These materials are used in applications where different regions of a component require different mechanical, thermal, or electrical properties.
-
Transparent Ceramics:
- SPS is employed to prepare transparent ceramics, such as barium strontium titanate (BST) ceramics. The rapid densification process during SPS results in small particle sizes and low sintering temperatures, leading to high transparency and density. For example, BST ceramics prepared using SPS have achieved transmittance exceeding 74% at a wavelength of 633 nm.
-
Fast Heating Rate and Short Sintering Time:
- One of the key advantages of SPS is its fast heating rate and short sintering time. This allows for the rapid production of materials with minimal grain growth, preserving the fine-grained structure and enhancing material properties.
-
Low Temperature and High Pressure Sintering:
- SPS can operate at relatively low temperatures and high pressures, which is beneficial for sintering materials that are sensitive to high temperatures. This capability reduces the risk of material degradation and allows for the sintering of temperature-sensitive materials.
-
Applications in Powder Metallurgy:
- SPS is widely used in powder metallurgy, where metal powders are sintered to form various parts. This application is crucial in manufacturing, as it allows for the production of complex shapes and custom metal forms with high precision.
In summary, Spark Plasma Sintering is a powerful technology with a wide range of applications in materials science. Its ability to rapidly sinter metals, ceramics, and composites at low temperatures and high pressures makes it an essential tool for producing advanced materials with tailored properties.
Summary Table:
Key Application | Description |
---|---|
Sintering of Metals, Ceramics, Composites | Produces high-density, fine-grained materials for strength and durability. |
Preparation of Nanomaterials | Creates nanomaterials with unique properties for nanotechnology and electronics. |
Bulk Amorphous Alloys | Forms alloys with superior mechanical properties like high strength and corrosion resistance. |
Gradient Functional Materials | Develops materials with varying properties for specialized applications. |
Transparent Ceramics | Produces ceramics like BST with high transparency and density. |
Fast Heating Rate & Short Sintering Time | Enables rapid production with minimal grain growth. |
Low Temperature & High Pressure Sintering | Sinters temperature-sensitive materials without degradation. |
Powder Metallurgy | Manufactures complex metal parts with high precision. |
Interested in leveraging Spark Plasma Sintering for your materials science projects? Contact our experts today to learn more!