Vapor deposition, particularly physical vapor deposition (PVD), is a versatile and widely used technique in modern industries. It involves the deposition of thin films or coatings onto substrates through physical processes such as sputtering or evaporation. PVD offers numerous advantages, including environmental friendliness, applicability to various inorganic materials, and the ability to produce coatings with excellent adhesion, resistance, and durability. These properties make PVD indispensable in applications ranging from high-temperature coatings to conductive layers for SEM specimens and protective coatings for heat-sensitive materials like plastics or biological samples. Below, we explore the key uses and benefits of vapor deposition in detail.
Key Points Explained:
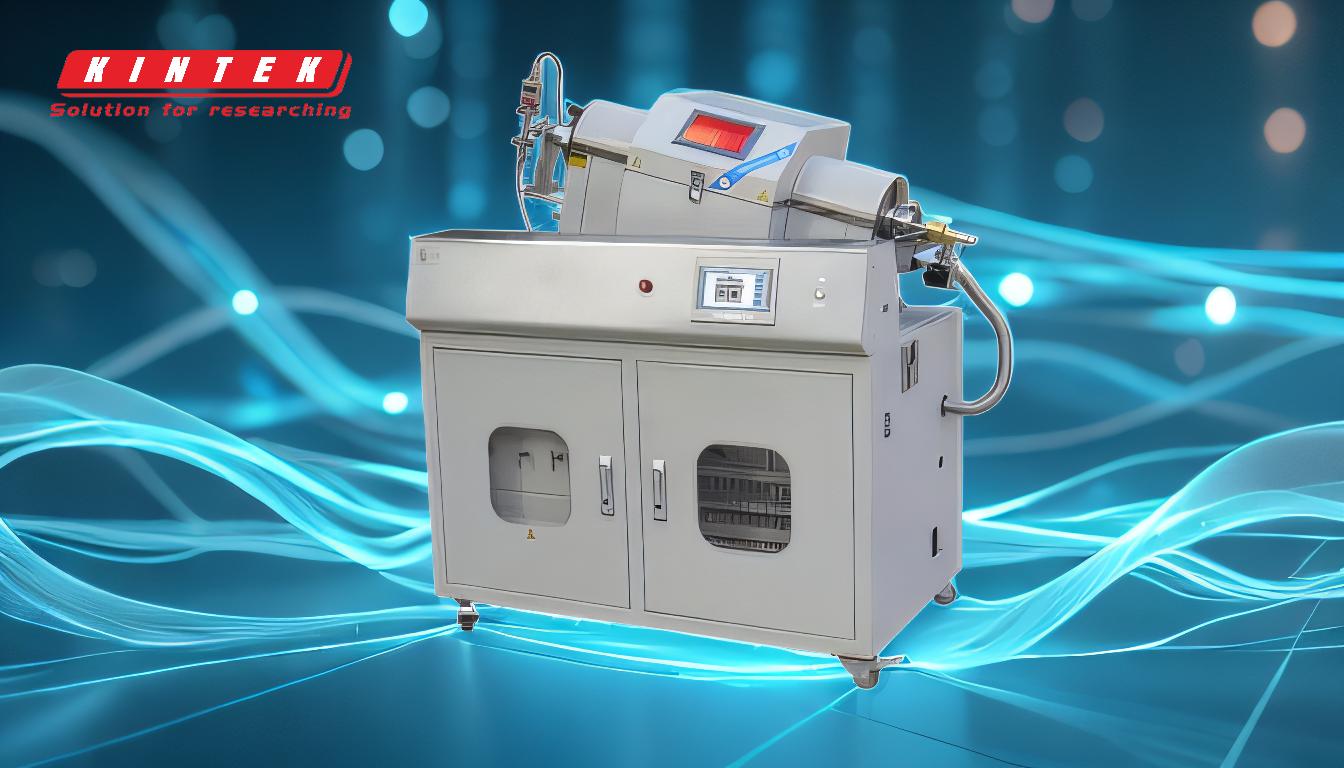
-
Wide Applicability Across Industries
- Vapor deposition techniques, especially PVD, are used across a broad spectrum of industries. They are employed in manufacturing processes to create coatings that enhance the performance, durability, and functionality of materials.
- Examples include:
- High-temperature coatings: Used in aerospace and automotive industries to protect components exposed to extreme heat.
- Conductive coatings: Applied to SEM (scanning electron microscope) specimens to improve imaging quality.
- Coatings for heat-sensitive materials: Used in the medical and electronics industries to protect plastics, biological samples, and other delicate materials.
-
Environmental and Operational Advantages
- PVD is an environmentally friendly process because it does not require chemical reagents or post-treatment cleaning, reducing waste and pollution.
- The process is highly controllable, allowing for precise adjustments to the composition and thickness of the coatings, which is critical for achieving desired material properties.
-
Common PVD Methods and Their Applications
- The two most common PVD methods are plasma sputtering and electron-beam evaporation:
- Plasma sputtering: This method involves bombarding a target material with high-energy ions to dislodge atoms, which then deposit onto a substrate. It is widely used for creating durable and uniform coatings.
- Electron-beam evaporation: In this method, an electron beam heats a target material until it evaporates, and the vapor condenses onto a substrate. This technique is ideal for creating high-purity coatings and is often used in semiconductor manufacturing.
- The two most common PVD methods are plasma sputtering and electron-beam evaporation:
-
Advantages of PVD Coatings
- Excellent adhesion: PVD coatings bond strongly to substrates, ensuring long-lasting performance.
- Resistance and durability: Coatings produced through PVD are highly resistant to wear, corrosion, and oxidation, making them suitable for harsh environments.
- Versatility: PVD can be applied to a wide range of inorganic materials, including metals, ceramics, and composites.
-
Specific Industrial Applications
- Aerospace: PVD is used to create thermal barrier coatings for turbine blades and other high-temperature components.
- Electronics: It is employed to deposit conductive and insulating layers in microelectronics and semiconductor devices.
- Medical: PVD coatings are applied to surgical instruments and implants to improve biocompatibility and reduce wear.
- Optics: Thin films produced by PVD are used in lenses, mirrors, and other optical components to enhance performance.
-
Future Trends and Innovations
- The demand for PVD technologies is expected to grow as industries seek more sustainable and efficient coating solutions.
- Innovations in PVD equipment and processes, such as advanced sputtering techniques and hybrid deposition methods, are likely to expand its applications further.
In summary, vapor deposition, particularly PVD, is a critical technology with diverse applications across industries. Its ability to produce high-quality, durable, and environmentally friendly coatings makes it an essential tool in modern manufacturing and material science. As technology advances, the scope of vapor deposition is expected to broaden, offering even more innovative solutions to industrial challenges.
Summary Table:
Key Aspect | Details |
---|---|
Industries | Aerospace, automotive, electronics, medical, optics |
Applications | High-temperature coatings, conductive layers, protective coatings |
Advantages | Environmental friendliness, excellent adhesion, resistance, durability |
Common Methods | Plasma sputtering, electron-beam evaporation |
Future Trends | Sustainable solutions, advanced sputtering techniques, hybrid methods |
Learn how vapor deposition can revolutionize your industry—contact us today for expert advice!