Vapor phase deposition techniques are essential processes in thin film fabrication, widely used in industries such as semiconductors, optics, and coatings. These techniques involve the transformation of a material into a vapor phase, which is then deposited onto a substrate to form a thin, uniform layer. The primary methods include Physical Vapor Deposition (PVD), Chemical Vapor Deposition (CVD), Atomic Layer Deposition (ALD), and Spray Pyrolysis. Each technique has unique mechanisms and applications, offering advantages in terms of purity, uniformity, and adhesion of the deposited films.
Key Points Explained:
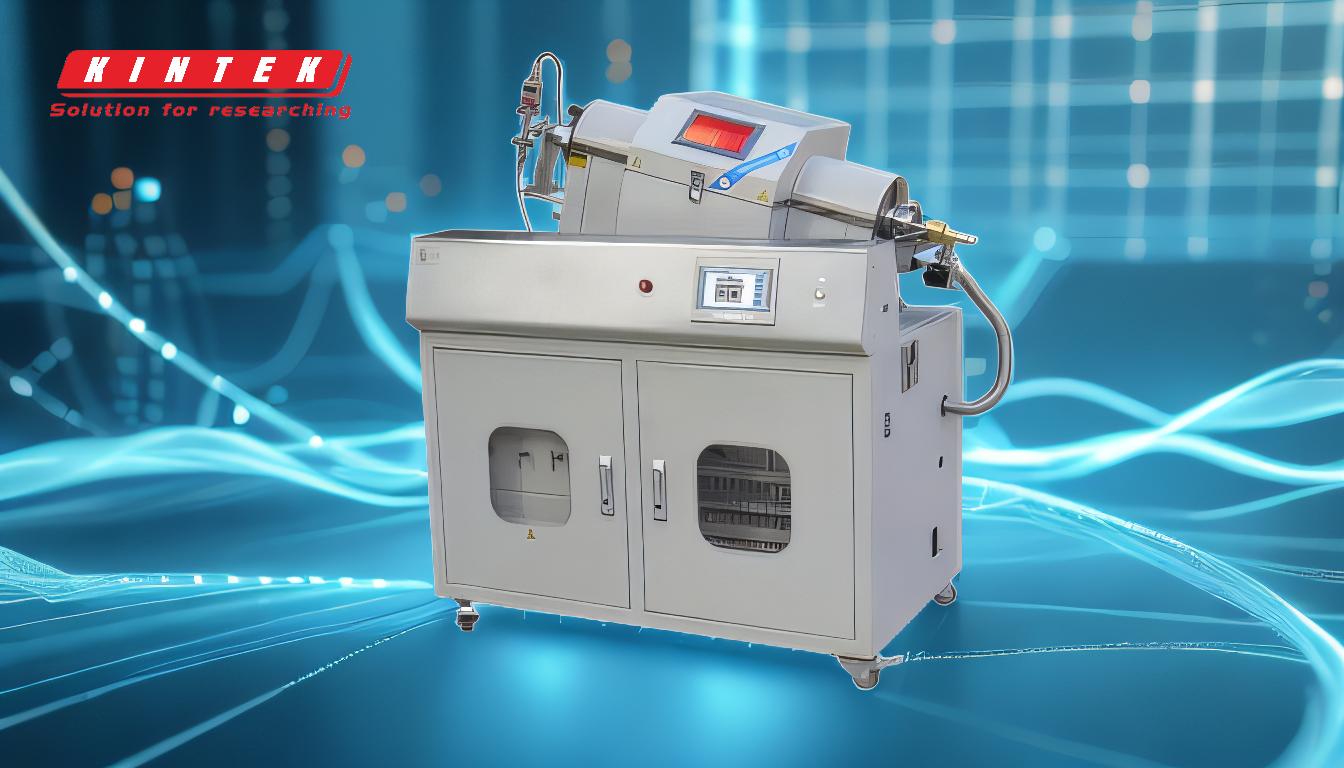
-
Physical Vapor Deposition (PVD)
- PVD involves the physical transformation of a solid material into a vapor phase, which is then deposited onto a substrate.
-
Common PVD Methods:
- Thermal Evaporation: The material is heated until it vaporizes, often using an electric heater. This method is simple and effective for materials with low melting points.
- Electron Beam Evaporation: A high-energy electron beam is used to vaporize the material, allowing for the deposition of high-purity films.
- Sputtering: A plasma or ion beam is used to eject atoms from a target material, which are then deposited onto the substrate. This technique is versatile and suitable for a wide range of materials.
- Applications: PVD is used in the production of optical coatings, semiconductor devices, and wear-resistant coatings.
-
Chemical Vapor Deposition (CVD)
- CVD relies on chemical reactions to deposit a thin film onto a substrate. The precursor gases react on the substrate surface, forming a solid film.
- Advantages: CVD can produce highly uniform and conformal coatings, even on complex geometries.
-
Types of CVD:
- Thermal CVD: Uses heat to drive the chemical reactions.
- Plasma-Enhanced CVD (PECVD): Utilizes plasma to lower the reaction temperature, making it suitable for temperature-sensitive substrates.
- Applications: CVD is widely used in the semiconductor industry for depositing silicon dioxide, silicon nitride, and other materials.
-
Atomic Layer Deposition (ALD)
- ALD is a precise technique that deposits films one atomic layer at a time. It involves alternating exposures of the substrate to different precursor gases, allowing for excellent control over film thickness and composition.
- Advantages: ALD produces highly uniform and conformal films with atomic-level precision.
- Applications: ALD is used in advanced semiconductor manufacturing, such as the fabrication of high-k dielectrics and nanoscale devices.
-
Spray Pyrolysis
- Spray Pyrolysis involves spraying a solution containing the desired material onto a heated substrate. The solution decomposes upon heating, leaving behind a thin film.
- Advantages: This method is cost-effective and suitable for large-area deposition.
- Applications: Spray Pyrolysis is used in the production of solar cells, transparent conductive oxides, and other functional coatings.
-
Molecular Beam Epitaxy (MBE)
- MBE is a specialized form of PVD used to grow high-quality crystalline films. It involves the controlled deposition of atoms or molecules onto a substrate under ultra-high vacuum conditions.
- Advantages: MBE allows for precise control over film composition and structure, making it ideal for research and high-performance applications.
- Applications: MBE is used in the fabrication of compound semiconductors, quantum wells, and superlattices.
-
Ion Beam Sputtering Deposition
- This technique uses an ion beam to sputter material from a target, which is then deposited onto a substrate.
- Advantages: Ion beam sputtering produces films with excellent adhesion and uniformity.
- Applications: It is used in the production of optical coatings, magnetic films, and other specialized coatings.
In summary, vapor phase deposition techniques are critical for creating high-quality thin films with precise control over thickness, composition, and structure. Each method has its strengths and is chosen based on the specific requirements of the application. Whether for semiconductor devices, optical coatings, or functional materials, these techniques enable the development of advanced technologies.
Summary Table:
Technique | Key Features | Applications |
---|---|---|
Physical Vapor Deposition (PVD) | - Thermal Evaporation, Electron Beam Evaporation, Sputtering | Optical coatings, semiconductor devices, wear-resistant coatings |
Chemical Vapor Deposition (CVD) | - Thermal CVD, Plasma-Enhanced CVD (PECVD) | Semiconductor industry (e.g., silicon dioxide, silicon nitride) |
Atomic Layer Deposition (ALD) | - Atomic-level precision, highly uniform films | Advanced semiconductor manufacturing, high-k dielectrics, nanoscale devices |
Spray Pyrolysis | - Cost-effective, large-area deposition | Solar cells, transparent conductive oxides, functional coatings |
Molecular Beam Epitaxy (MBE) | - Ultra-high vacuum, precise control over film composition | Compound semiconductors, quantum wells, superlattices |
Ion Beam Sputtering Deposition | - Excellent adhesion and uniformity | Optical coatings, magnetic films, specialized coatings |
Learn how vapor phase deposition can elevate your thin film fabrication—contact our experts today!