Sintering is a versatile manufacturing process that can be applied to a wide range of materials, including metals, ceramics, polymers, and composites. It is particularly useful for materials with high melting points, such as tungsten and molybdenum, as well as for powder metallurgy applications involving metals like iron, aluminum, nickel, copper, and titanium alloys. Sintering is also used in additive manufacturing, rapid prototyping, and the production of high-temperature components like gears and bearings. The process enhances material properties, making it suitable for creating components with specific mechanical, thermal, or chemical characteristics.
Key Points Explained:
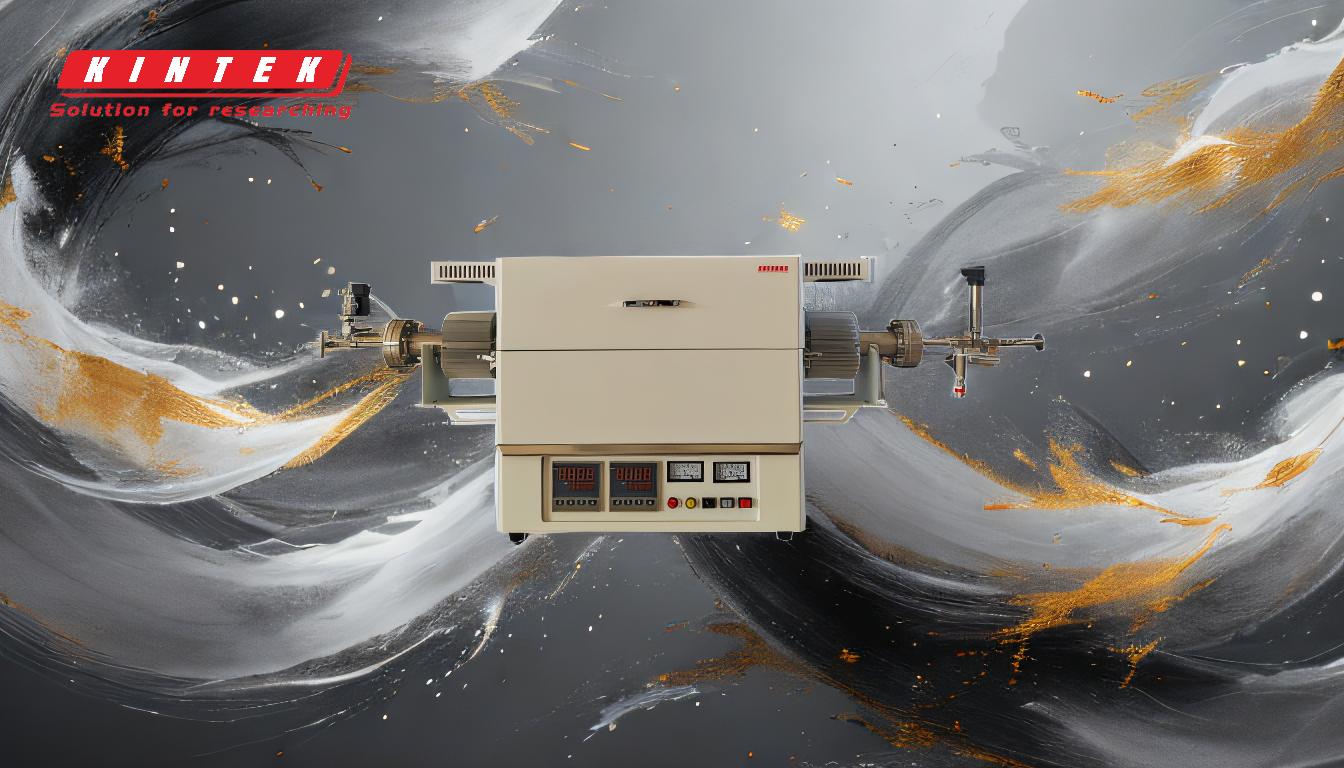
-
Materials Suitable for Sintering:
- Metals: Sintering is widely used for metals, including stainless steel, aluminum, nickel, copper, titanium alloys, and iron-based materials like iron-copper, iron-nickel, and carbon steels. These metals are processed to improve their mechanical properties, such as strength and durability.
- Ceramics: Ceramics, including oxides, carbides, and nitrides, are commonly sintered to produce high-temperature components like gears, bearings, and other parts requiring thermal stability and wear resistance.
- Polymers: Polymers are sintered for applications such as rapid prototyping and the manufacture of filters. This process allows for the creation of complex shapes and structures with specific porosity and mechanical properties.
- Composites: Sintering is also used for composite materials, which combine different materials to achieve unique properties, such as enhanced strength, lightweight, or thermal resistance.
-
Applications of Sintering:
- Powder Metallurgy: Sintering is a key process in powder metallurgy, where metal powders are compacted and heated to form solid components. This is particularly useful for producing small, intricate parts like gears and pulleys.
- Additive Manufacturing: Advances in sintering technology have made it suitable for additive manufacturing, where materials are layered and sintered to create complex, custom-designed components.
- High-Temperature Components: Sintered ceramics and metals are used in high-temperature applications, such as aerospace and automotive industries, where components must withstand extreme conditions.
-
Advantages of Sintering:
- Material Property Enhancement: Sintering improves the mechanical, thermal, and chemical properties of materials, making them suitable for demanding applications.
- Versatility: The process can be applied to a wide range of materials, including metals, ceramics, polymers, and composites, allowing for the production of diverse components.
- Cost-Effectiveness: Sintering is often more cost-effective than traditional manufacturing methods, especially for producing small, complex parts in large quantities.
-
Technological Advances:
- Improved Sintering Techniques: Advances in sintering technology have led to the refinement of materials like stainless steel, aluminum, and titanium alloys, making them more suitable for modern manufacturing processes.
- Additive Manufacturing Integration: Sintering is increasingly integrated with additive manufacturing techniques, enabling the production of complex, custom-designed components with enhanced material properties.
-
Material-Specific Considerations:
- Metals: Metals like iron, nickel, and copper are often sintered under atmospheric pressure with protective gases to prevent oxidation and improve material integrity.
- Ceramics: Sintered ceramics are used in applications requiring high thermal stability and wear resistance, such as in the production of gears and bearings.
- Polymers: Sintered polymers are used in rapid prototyping and filter manufacturing, where specific porosity and mechanical properties are required.
In summary, sintering is a highly versatile and adaptable process that can be applied to a wide range of materials, including metals, ceramics, polymers, and composites. Its ability to enhance material properties and produce complex components makes it a valuable technique in various industries, from aerospace to automotive and beyond.
Summary Table:
Aspect | Details |
---|---|
Materials | Metals, ceramics, polymers, composites |
Applications | Powder metallurgy, additive manufacturing, high-temperature components |
Advantages | Enhanced material properties, versatility, cost-effectiveness |
Technological Advances | Improved sintering techniques, additive manufacturing integration |
Unlock the potential of sintering for your projects—contact our experts today!