PVD coating, or Physical Vapor Deposition coating, is an advanced vacuum-based process used to apply thin, durable, and high-performance coatings to various materials. It involves vaporizing a solid material in a vacuum chamber, which then condenses onto a substrate to form a thin film. This process is highly controlled, allowing for precise modifications to the coating's composition and properties. PVD coatings are known for their exceptional hardness, resistance to corrosion, wear, and oxidation, as well as their ability to enhance both functional and aesthetic properties of materials. The process is widely used in industries such as aerospace, automotive, medical devices, and consumer goods due to its versatility and environmental friendliness.
Key Points Explained:
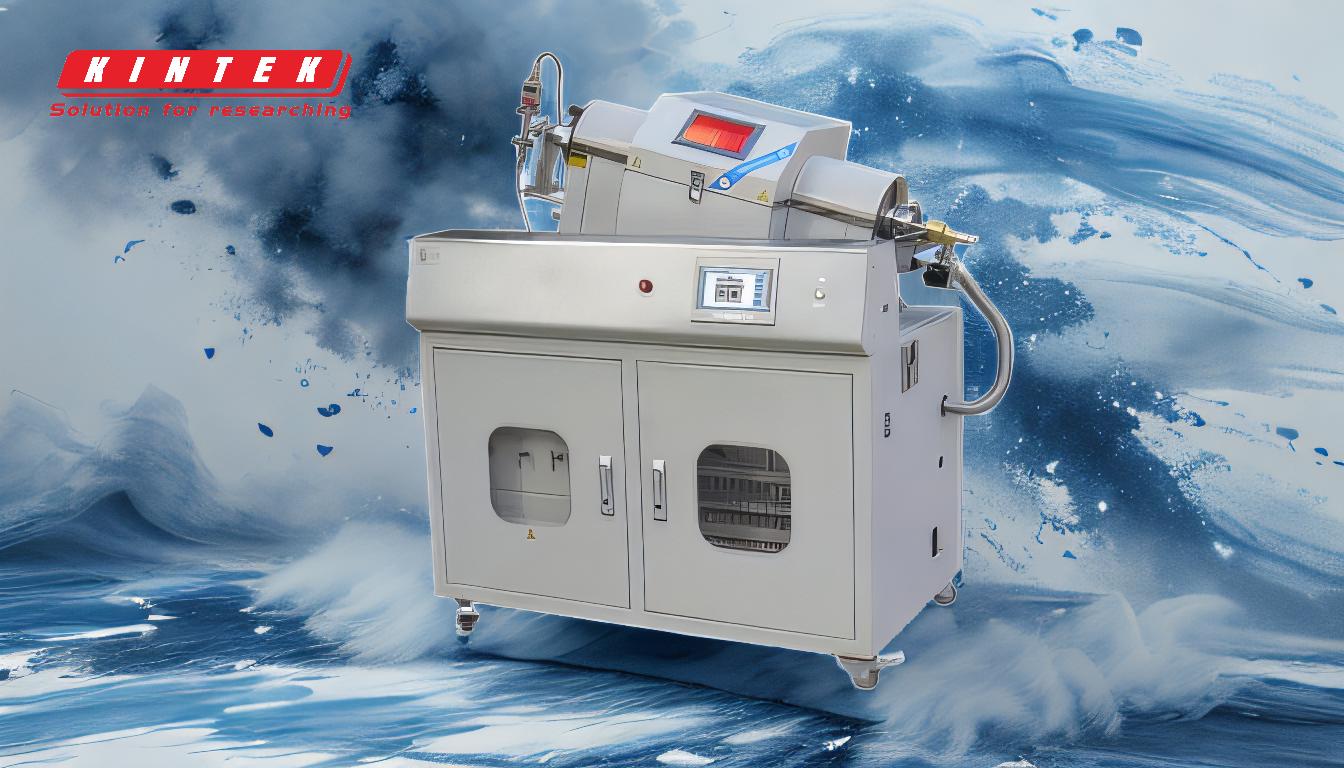
-
What is PVD Coating?
- PVD coating is a vacuum-based process where a solid material is vaporized and then deposited onto a substrate to form a thin, durable layer. The process occurs in a vacuum chamber to ensure cleanliness and precision. This method allows for the creation of coatings that are highly resistant to wear, corrosion, and oxidation, making them ideal for demanding applications.
-
How Does PVD Coating Work?
- The PVD process involves several key steps:
- Vaporization: The solid material (target) is vaporized using techniques such as heating in a crucible, electron beam bombardment, ion bombardment from a plasma, or a cathodic arc.
- Transport: The vaporized material travels through the vacuum chamber and deposits onto the substrate.
- Condensation: The vapor condenses on the substrate, forming a thin, uniform coating.
- Reactive gases can be introduced during the process to modify the coating's composition, enhancing its properties.
- The PVD process involves several key steps:
-
Properties of PVD Coatings
- Thin and Durable: PVD coatings are typically between 0.5 to 5 microns thick, yet they are extremely durable and hard.
- Hardness and Wear Resistance: The coatings significantly increase the hardness and wear resistance of the substrate, making them suitable for high-stress applications.
- Corrosion and Oxidation Resistance: PVD coatings provide excellent protection against corrosion and oxidation, extending the lifespan of the coated material.
- Aesthetic Versatility: PVD coatings can be applied to achieve various colors, textures, and finishes, making them popular for decorative purposes.
-
Benefits of PVD Coating
- Durability and Reliability: PVD coatings are known for their long-lasting performance, even under harsh conditions.
- Compatibility: They can be applied to a wide range of materials, including metals, ceramics, and polymers.
- Uniform Coating: The vacuum environment ensures a uniform and consistent coating thickness across the substrate.
- Low Maintenance: PVD-coated surfaces require minimal maintenance due to their resistance to wear and corrosion.
- Environmental Friendliness: The process is environmentally friendly, as it produces minimal waste and does not involve harmful chemicals.
-
Applications of PVD Coatings
- Industrial Applications: PVD coatings are used in industries such as aerospace, automotive, and medical devices to enhance the performance and longevity of components.
- Consumer Goods: They are also used in consumer products like watches, jewelry, and electronics to improve both functionality and appearance.
- Aesthetic Uses: PVD coatings are often applied to stainless steel and other materials to create visually appealing finishes.
-
Factors Influencing PVD Coating Properties
- Substrate Material: The properties of the PVD coating are influenced by the underlying substrate material. For example, a TiN (Titanium Nitride) coating can significantly increase the fatigue limit and endurance of a Ti-6Al-4V alloy.
- Coating Hardness: The hardness of the coating is a critical factor in determining its durability and resistance to wear.
-
Advantages Over Other Coating Methods
- High Temperature Tolerance: PVD coatings can withstand high temperatures, making them suitable for applications where other coatings might fail.
- In-Situ Controls: The process allows for real-time monitoring and control, ensuring consistent quality and performance.
In summary, PVD coating is a highly versatile and effective method for applying thin, durable, and high-performance coatings to a wide range of materials. Its ability to enhance both functional and aesthetic properties makes it a valuable technique in various industries.
Summary Table:
Aspect | Details |
---|---|
Process | Vacuum-based vaporization and deposition of solid materials onto substrates |
Thickness | 0.5 to 5 microns |
Key Properties | High hardness, wear resistance, corrosion resistance, aesthetic versatility |
Applications | Aerospace, automotive, medical devices, consumer goods, decorative uses |
Benefits | Durability, compatibility, uniform coating, low maintenance, eco-friendly |
Interested in enhancing your materials with PVD coatings? Contact our experts today to learn more!