PVD (Physical Vapor Deposition) coating is a modern, environmentally friendly process used to apply thin, durable layers to materials, enhancing their performance and appearance. It involves vaporizing metal solids like titanium, zirconium, or chromium in a vacuum and reacting them with gases such as nitrogen to form a coating. PVD coatings improve surface hardness, wear resistance, corrosion resistance, and chemical stability. They also offer aesthetic benefits, such as a wide range of colors and a lustrous finish, while being safe for human use and environmentally sustainable. These coatings are widely used in industries like manufacturing, medical devices, and jewelry due to their durability, reliability, and ease of maintenance.
Key Points Explained:
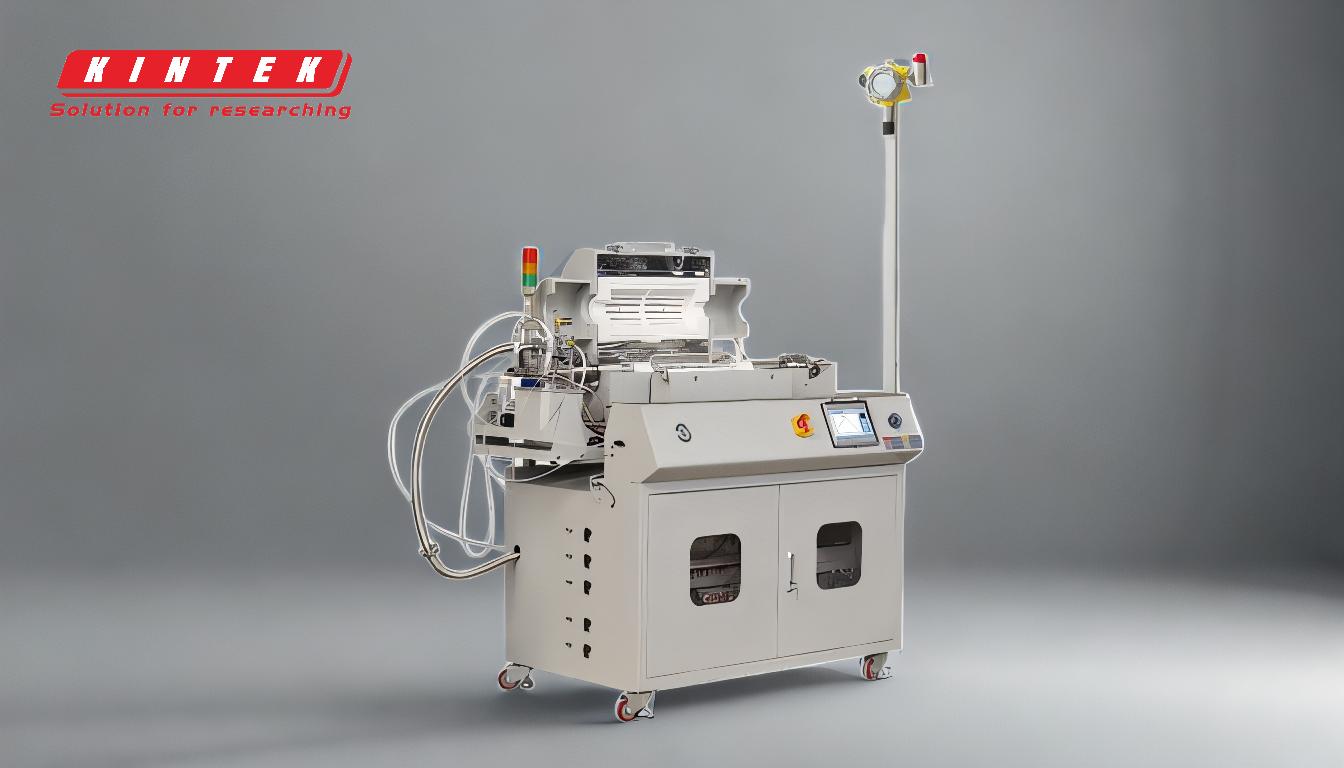
-
Enhanced Durability and Performance
- PVD coatings significantly improve the hardness and wear resistance of materials, making them more durable. For example, cutting tools with PVD coatings can last up to 10 times longer than uncoated tools.
- The coatings reduce friction, which minimizes wear and tear, extending the lifespan of the coated parts.
- They also provide excellent chemical and oxidation resistance, making them suitable for harsh environments.
-
Corrosion Resistance
- PVD coatings create a barrier that protects the substrate from corrosive elements, such as moisture and chemicals.
- This makes them ideal for applications in industries like marine, automotive, and medical, where corrosion resistance is critical.
-
Aesthetic Benefits
- PVD coatings offer a wide range of colors, from metallic finishes to vibrant hues, allowing for customization of product appearance.
- The coatings provide a long-lasting, jewelry-like finish that is resistant to tarnishing and fading.
- They can replicate polished or textured surfaces with high precision, maintaining the original design details.
-
Environmental and Health Safety
- PVD is an environmentally friendly process that produces no harmful byproducts.
- The coatings are non-toxic and safe for use in applications like surgical implants and food processing equipment.
- The process uses vacuum technology, ensuring clean and pure materials.
-
Versatility and Compatibility
- PVD coatings are compatible with a wide range of materials, including metals, plastics, and ceramics.
- They can be applied uniformly, even on complex shapes, ensuring consistent quality.
- The coatings can be combined with friction-reducing layers or structured as monolayers, multilayers, or nanostructures for specific applications.
-
Improved Adhesion and Dimensional Accuracy
- PVD coatings bond strongly with the substrate, ensuring long-lasting performance.
- They maintain the dimensional accuracy and contour of the original part, making them suitable for precision components.
- The process does not alter the microstructure of the substrate, preserving its mechanical properties.
-
Low Maintenance and Cost-Effectiveness
- PVD-coated parts require minimal maintenance due to their durability and resistance to wear and corrosion.
- The extended lifespan of coated tools and components reduces replacement costs, making PVD coatings a cost-effective solution in the long run.
-
Applications Across Industries
- Manufacturing: Cutting tools, molds, and dies benefit from increased hardness and wear resistance.
- Medical: Surgical instruments and implants use PVD coatings for their biocompatibility and corrosion resistance.
- Jewelry: PVD coatings provide a durable, attractive finish for watches, rings, and other accessories.
- Automotive: Components like engine parts and decorative trims use PVD coatings for both functional and aesthetic purposes.
In summary, PVD coatings are a versatile and sustainable solution for enhancing the performance, durability, and appearance of materials across various industries. Their ability to combine functional benefits with aesthetic appeal makes them a preferred choice for modern manufacturing and design.
Summary Table:
Key Benefits | Details |
---|---|
Enhanced Durability | Increases hardness and wear resistance; extends tool lifespan by up to 10x. |
Corrosion Resistance | Protects against moisture and chemicals, ideal for harsh environments. |
Aesthetic Appeal | Offers vibrant colors, jewelry-like finishes, and tarnish resistance. |
Environmental Safety | Non-toxic, eco-friendly, and safe for medical and food applications. |
Versatility | Compatible with metals, plastics, and ceramics; uniform application. |
Low Maintenance | Reduces wear and corrosion, lowering long-term costs. |
Applications | Used in manufacturing, medical, jewelry, and automotive industries. |
Ready to enhance your products with PVD coatings? Contact us today to learn more!