PVD finish stands for Physical Vapor Deposition finish, a process used to apply thin films to various substrates. This technique involves vaporizing a solid material in a vacuum environment and then depositing it onto a substrate, creating a durable and high-performance coating. PVD finishes are widely used in industries such as automotive, aerospace, and consumer electronics due to their excellent adhesion, hardness, and resistance to wear and corrosion. The process not only enhances the aesthetic appeal of products but also significantly improves their functional properties, making PVD coatings a preferred choice for many high-performance applications.
Key Points Explained:
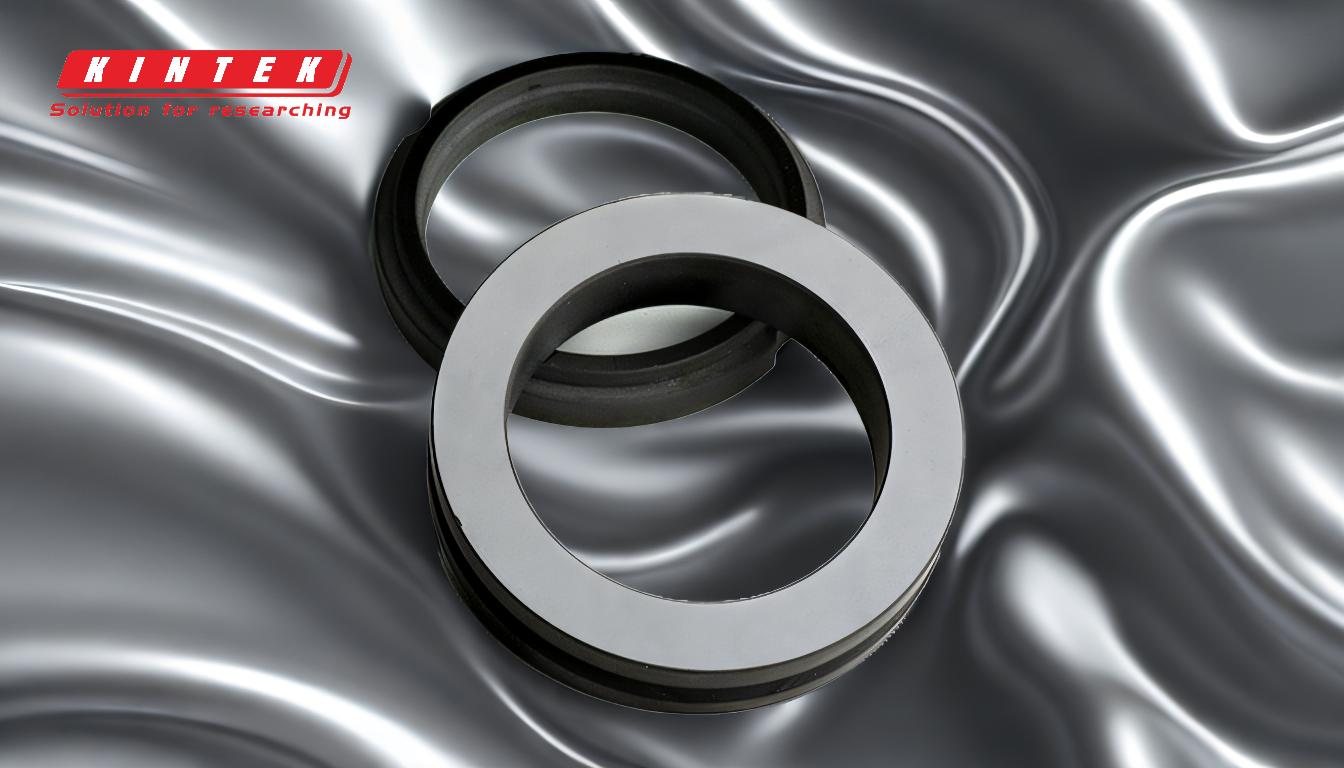
-
Definition of PVD Finish:
- PVD stands for Physical Vapor Deposition, a process that involves the vaporization of a solid material in a vacuum and its subsequent deposition onto a substrate. This method is used to create thin, durable coatings that enhance the properties of the substrate.
-
Importance of Adhesion in PVD Coatings:
- Adhesion is crucial in PVD coatings as it determines how well the coating bonds to the substrate. Good adhesion ensures the durability and performance of the coating in its intended application. Without strong adhesion, the coating may peel or flake off, compromising the integrity and functionality of the product.
-
Applications of PVD Finishes:
- PVD finishes are used in a variety of industries, including automotive, aerospace, and consumer electronics. In the automotive industry, PVD coatings are applied to engine components to improve wear resistance and reduce friction. In aerospace, they are used on turbine blades to enhance durability and performance. In consumer electronics, PVD coatings are used on mobile phone cases and watch bands to provide a scratch-resistant and aesthetically pleasing finish.
-
Benefits of PVD Finishes:
- Durability: PVD coatings are known for their hardness and resistance to wear, making them ideal for high-stress applications.
- Aesthetic Appeal: PVD finishes can produce a wide range of colors and finishes, enhancing the visual appeal of products.
- Corrosion Resistance: PVD coatings provide excellent protection against corrosion, extending the lifespan of the coated products.
- Environmental Friendliness: The PVD process is environmentally friendly as it does not involve harmful chemicals and produces minimal waste.
-
Process of PVD Coating:
- Preparation: The substrate is cleaned and prepared to ensure proper adhesion of the coating.
- Vaporization: The coating material is vaporized in a vacuum chamber using techniques such as sputtering or evaporation.
- Deposition: The vaporized material is then deposited onto the substrate, forming a thin, uniform coating.
- Post-Treatment: The coated substrate may undergo additional treatments to enhance the properties of the coating.
-
Factors Affecting PVD Coating Quality:
- Substrate Material: The type of substrate material can affect the adhesion and performance of the PVD coating.
- Coating Material: Different coating materials offer varying levels of hardness, wear resistance, and corrosion resistance.
- Process Parameters: Factors such as temperature, pressure, and deposition rate can influence the quality of the PVD coating.
- Surface Preparation: Proper cleaning and preparation of the substrate are essential for achieving good adhesion and a high-quality coating.
By understanding these key points, one can appreciate the complexity and benefits of PVD finishes, making them a valuable choice for enhancing the performance and aesthetics of various products.
Summary Table:
Key Aspect | Details |
---|---|
Definition | PVD (Physical Vapor Deposition) applies thin, durable coatings in a vacuum. |
Applications | Automotive, aerospace, consumer electronics, and more. |
Benefits | Durability, aesthetic appeal, corrosion resistance, eco-friendliness. |
Process | Preparation, vaporization, deposition, and post-treatment. |
Quality Factors | Substrate material, coating material, process parameters, surface prep. |
Enhance your products with PVD coatings—contact us today to learn more!