Pyrolysis is a thermochemical process that transforms organic materials, such as biomass, into valuable products like biochar, bio-oil, and syngas. When applied to biochar production, pyrolysis involves heating biomass to high temperatures (typically 300-900°C) in the absence of oxygen, leading to the decomposition of the material into carbon-rich solids (biochar), gases (syngas), and liquids (bio-oil). The process enhances the properties of the original biomass, making biochar a stable, carbon-rich material with applications in soil improvement, carbon sequestration, and environmental remediation. The specific characteristics of biochar, such as porosity, surface area, and chemical composition, depend on the pyrolysis conditions, including temperature, heating rate, and residence time.
Key Points Explained:
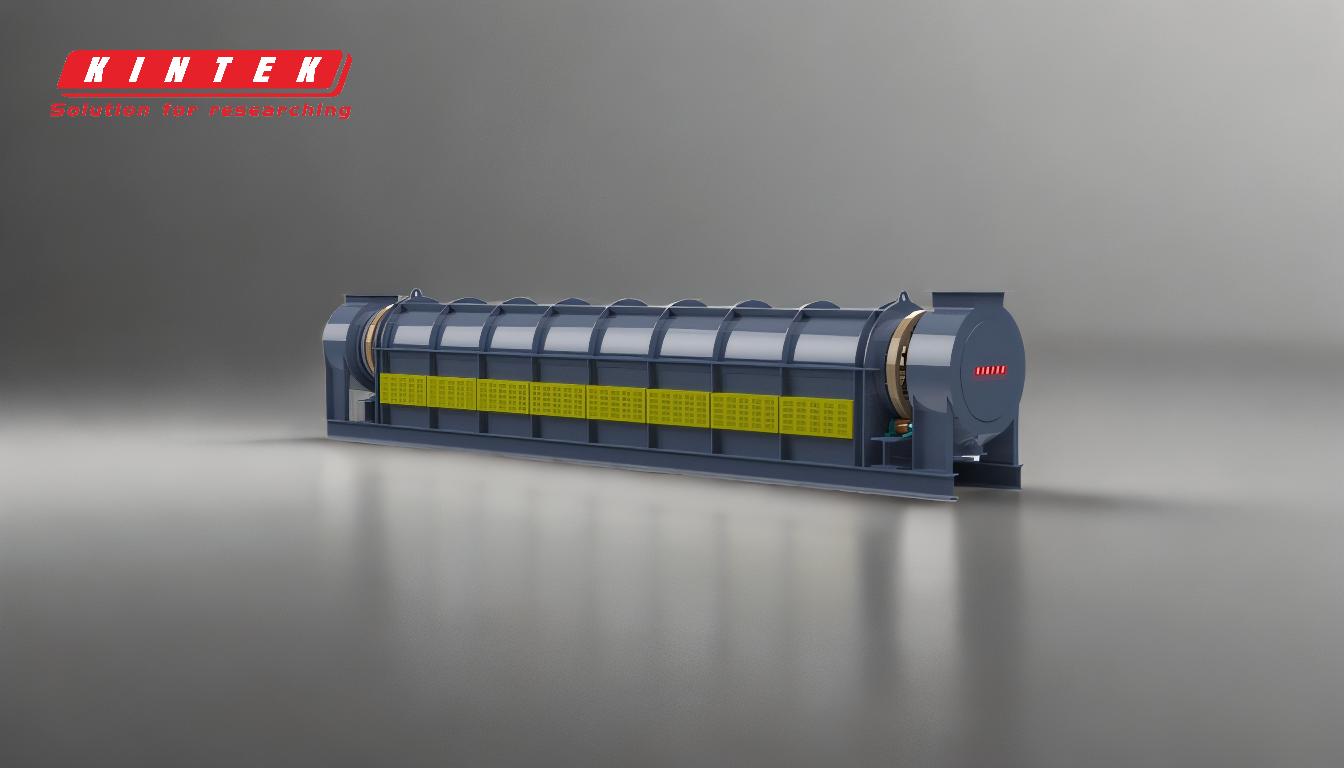
-
Definition of Pyrolysis and Its Role in Biochar Production:
- Pyrolysis is a thermal decomposition process that occurs in the absence of oxygen.
- It converts biomass into biochar, bio-oil, and syngas, with biochar being the primary solid product.
- The process is essential for transforming low-value biomass into high-value materials with diverse applications.
-
Process Conditions and Their Impact on Biochar:
- Temperature: Pyrolysis typically occurs between 300-900°C. Lower temperatures (around 400°C) during slow pyrolysis favor biochar production, while higher temperatures may increase gas and liquid yields.
- Residence Time: Longer residence times during slow pyrolysis enhance the formation of stable, carbon-rich biochar.
- Heating Rate: Slow heating rates are used in biochar production to ensure thorough decomposition and maximize solid yield.
-
Products of Pyrolysis:
- Biochar: A carbon-rich solid with high stability, porosity, and surface area. It is used for soil amendment, carbon sequestration, and environmental applications.
- Syngas: A mixture of gases, including hydrogen, carbon monoxide, and methane, which can be used as a fuel or chemical feedstock.
- Bio-oil: A liquid mixture of water and volatile organic compounds, used as a renewable fuel or chemical precursor.
-
Transformation of Biomass During Pyrolysis:
- The biomass undergoes thermal decomposition, breaking down complex organic molecules into simpler compounds.
- Volatile components are released as gases and liquids, leaving behind a solid residue enriched in carbon.
- The process removes moisture, volatile matter, and other impurities, resulting in a stable and durable material.
-
Properties of Biochar:
- Porosity: Pyrolysis creates a highly porous structure, which enhances biochar's ability to retain water and nutrients in soil.
- Surface Area: The process increases the surface area, making biochar effective for adsorption and chemical reactions.
- Stability: Biochar is resistant to microbial decomposition, making it a long-term carbon sink.
-
Applications of Biochar:
- Soil Amendment: Improves soil fertility, water retention, and nutrient availability.
- Carbon Sequestration: Stores carbon in a stable form, reducing greenhouse gas emissions.
- Environmental Remediation: Adsorbs pollutants and contaminants from soil and water.
-
Energy Balance and Sustainability:
- The energy required for pyrolysis can be partially or fully supplied by the combustion of syngas produced during the process.
- Biochar production is a sustainable method for managing agricultural and forestry residues, reducing waste, and generating valuable by-products.
By understanding the pyrolysis process and its effects on biochar, stakeholders can optimize production conditions to meet specific application requirements, ensuring the efficient use of biomass resources and contributing to environmental sustainability.
Summary Table:
Aspect | Details |
---|---|
Process | Thermal decomposition of biomass in the absence of oxygen. |
Temperature Range | 300-900°C (lower temps favor biochar; higher temps increase gas/liquid yield). |
Key Products | Biochar (solid), syngas (gases), bio-oil (liquid). |
Biochar Properties | High porosity, surface area, and stability; ideal for soil and carbon storage. |
Applications | Soil amendment, carbon sequestration, environmental remediation. |
Sustainability | Energy-efficient process; utilizes syngas for energy, reducing waste. |
Discover how pyrolysis can transform your biomass into valuable resources—contact us today to learn more!