The efficiency of a hydraulic system depends on several interconnected factors, including the design and quality of components, the type of hydraulic fluid used, system maintenance, and operational conditions. Key elements such as pumps, valves, actuators, and pipes must be optimized to minimize energy losses due to friction, leakage, and heat generation. The viscosity and quality of the hydraulic fluid also play a critical role in ensuring smooth operation and reducing wear. Regular maintenance, such as filter changes and seal inspections, is essential to prevent inefficiencies. Additionally, operational factors like load conditions, temperature, and system pressure must be carefully managed to maintain optimal performance.
Key Points Explained:
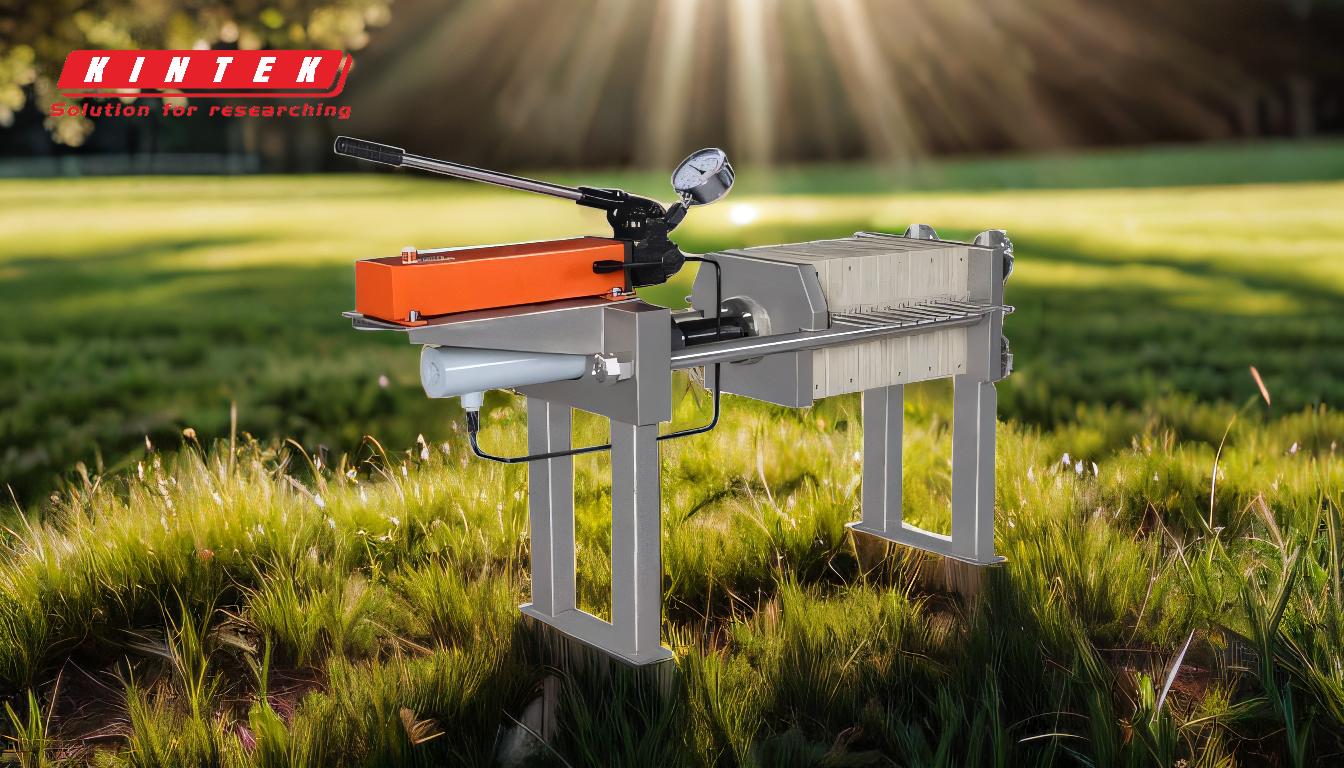
-
Component Design and Quality:
- The efficiency of a hydraulic system is heavily influenced by the design and quality of its components, such as pumps, valves, actuators, and pipes. High-quality components are engineered to minimize energy losses due to friction and leakage. For example, precision-engineered pumps and valves can reduce internal leakage, while properly sized pipes can minimize pressure drops.
-
Hydraulic Fluid Characteristics:
- The type and quality of hydraulic fluid are critical to system efficiency. The fluid's viscosity must be matched to the operating temperature and pressure to ensure smooth flow and lubrication. Using the wrong fluid can lead to increased friction, overheating, and wear. Additionally, contaminants in the fluid can cause blockages and damage to components, further reducing efficiency.
-
System Maintenance:
- Regular maintenance is essential to keep a hydraulic system operating efficiently. This includes changing filters to remove contaminants, inspecting and replacing worn seals, and checking for leaks. Neglecting maintenance can lead to increased friction, leaks, and component failures, all of which reduce system efficiency.
-
Operational Conditions:
- The efficiency of a hydraulic system can vary depending on the operational conditions. Factors such as load, temperature, and pressure must be carefully managed. For example, operating a system at excessively high pressures can lead to energy losses and increased wear. Similarly, extreme temperatures can affect the viscosity of the hydraulic fluid, leading to inefficiencies.
-
Energy Losses:
- Energy losses in a hydraulic system can occur due to friction, leakage, and heat generation. Friction losses occur as the hydraulic fluid moves through pipes and components, while leakage losses occur when fluid escapes through gaps in seals or connections. Heat generation can also reduce efficiency, as it can cause the hydraulic fluid to degrade and lose its lubricating properties.
-
System Design and Optimization:
- The overall design of the hydraulic system plays a significant role in its efficiency. A well-designed system will have components that are properly sized and matched to the operational requirements. Additionally, the system should be optimized to minimize energy losses, such as by using efficient pumps and valves and reducing the length of hydraulic lines.
By understanding and addressing these key factors, the efficiency of a hydraulic system can be maximized, leading to improved performance and reduced operational costs.
Summary Table:
Factor | Impact on Efficiency |
---|---|
Component Design & Quality | High-quality components minimize energy losses from friction and leakage. |
Hydraulic Fluid | Proper viscosity and quality ensure smooth flow, lubrication, and reduced wear. |
System Maintenance | Regular maintenance prevents inefficiencies caused by leaks, friction, and wear. |
Operational Conditions | Managing load, temperature, and pressure ensures optimal performance. |
Energy Losses | Friction, leakage, and heat generation reduce efficiency if not minimized. |
System Design & Optimization | Properly sized and optimized components minimize energy losses and improve performance. |
Maximize your hydraulic system's efficiency—contact our experts today for tailored solutions!