Sintering is a complex process influenced by multiple factors that determine the final properties of the material. Key factors include temperature, heating rate, pressure, particle size, composition, atmosphere, and cooling rate. Temperature plays a critical role in sintering kinetics and material properties, while heating rate affects densification. Pressure enhances particle rearrangement and reduces porosity. Smaller particle sizes and homogeneous compositions promote better densification. Additionally, the sintering atmosphere (air, vacuum, or inert gases) and cooling rate significantly impact the mechanical properties of the sintered product, such as tensile strength, bending fatigue strength, and impact energy. Understanding and optimizing these factors are essential for achieving desired material characteristics.
Key Points Explained:
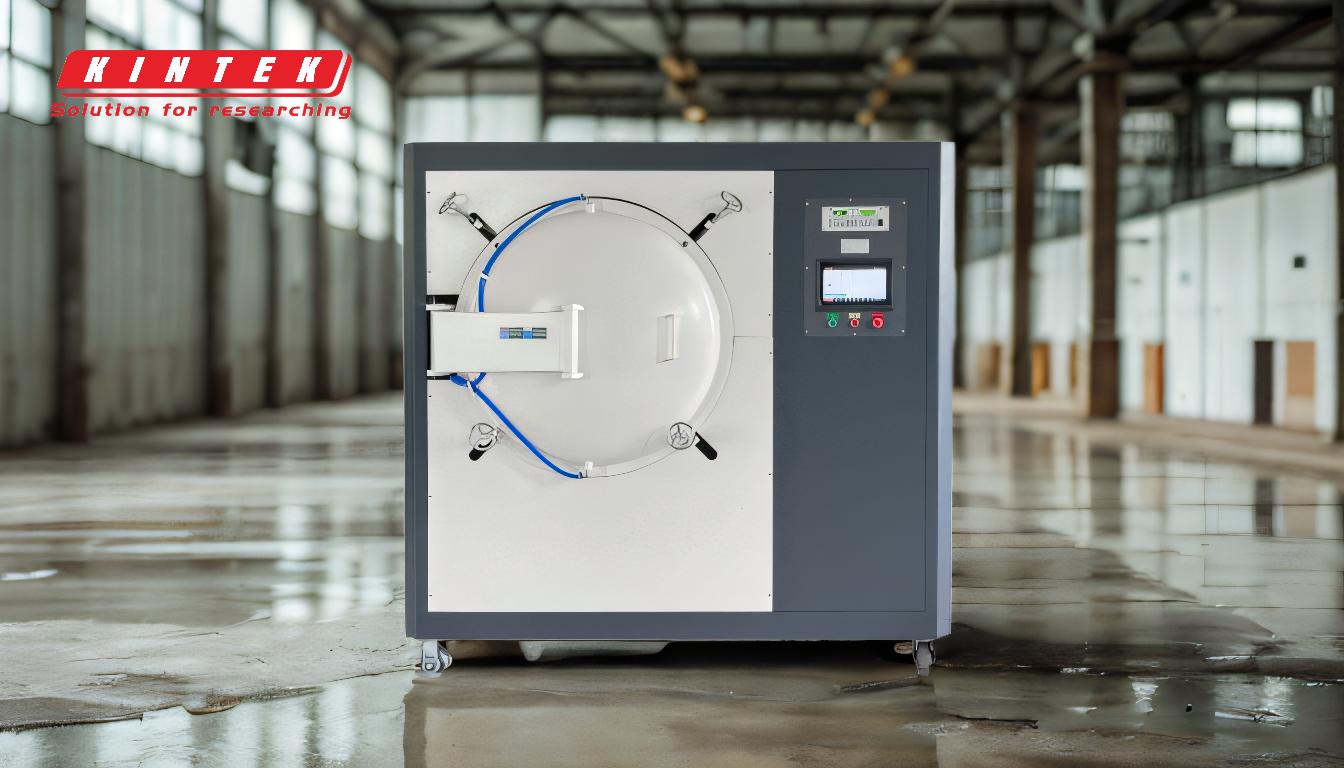
-
Temperature:
- Role: Temperature is a primary factor in sintering, as it directly influences sintering kinetics and the final material properties.
- Impact: Higher temperatures accelerate atomic diffusion, leading to better particle bonding and densification. However, excessively high temperatures can cause unwanted grain growth or phase transformations.
- Optimization: The sintering temperature must be carefully controlled to balance densification and material integrity.
-
Heating Rate:
- Role: The rate at which the material is heated affects the densification process.
- Impact: A slower heating rate allows for more uniform heat distribution, reducing thermal stresses and improving densification. Rapid heating can lead to uneven sintering and defects.
- Optimization: The heating rate should be tailored to the material and desired properties to ensure uniform sintering.
-
Pressure:
- Role: Applied pressure during sintering enhances particle rearrangement and eliminates porosity.
- Impact: Pressure helps in achieving higher densities by forcing particles into closer contact, which promotes better bonding and reduces voids.
- Optimization: The amount of pressure applied must be optimized to avoid damaging the material while achieving the desired density.
-
Particle Size:
- Role: The size of the particles being sintered significantly affects the sintering behavior.
- Impact: Smaller particles have a higher surface area-to-volume ratio, which enhances atomic diffusion and promotes faster densification. Larger particles may result in incomplete sintering and higher porosity.
- Optimization: Using finer powders can improve compaction and densification, but the particle size distribution must be controlled to avoid issues like agglomeration.
-
Composition:
- Role: The chemical composition of the material influences sintering behavior.
- Impact: Homogeneous compositions promote uniform sintering, while heterogeneous compositions can lead to uneven densification and defects. The presence of additives or impurities can also affect sintering kinetics.
- Optimization: Ensuring a homogeneous and controlled composition is crucial for achieving consistent sintering results.
-
Atmosphere:
- Role: The sintering atmosphere (air, vacuum, or inert gases like argon or nitrogen) affects the material's interaction with the environment.
- Impact: An inert atmosphere prevents oxidation and contamination, which is critical for materials sensitive to oxygen. Vacuum sintering can eliminate gases trapped in the material, reducing porosity.
- Optimization: The choice of atmosphere depends on the material and desired properties, with inert or vacuum atmospheres often preferred for high-quality sintering.
-
Cooling Rate:
- Role: The rate at which the material is cooled after sintering affects its final mechanical properties.
- Impact: A controlled cooling rate can prevent thermal stresses and phase transformations, leading to improved mechanical properties such as tensile strength, bending fatigue strength, and impact energy.
- Optimization: The cooling rate should be adjusted based on the material and desired properties to ensure optimal performance.
-
Liquid Phase Control:
- Role: In some sintering processes, a liquid phase may form, which can enhance densification.
- Impact: The presence of a liquid phase can improve particle bonding and reduce porosity, but excessive liquid phase can lead to undesirable grain growth or deformation.
- Optimization: The amount of liquid phase must be carefully controlled to balance densification and material integrity.
By understanding and optimizing these factors, manufacturers can achieve the desired material properties and performance in sintered products. Each factor must be carefully considered and controlled to ensure a successful sintering process.
Summary Table:
Factor | Role | Impact | Optimization |
---|---|---|---|
Temperature | Influences sintering kinetics and material properties | Higher temps accelerate bonding; excessive heat causes grain growth | Control temperature to balance densification and material integrity |
Heating Rate | Affects densification process | Slow heating ensures uniform sintering; rapid heating causes defects | Tailor heating rate to material and desired properties |
Pressure | Enhances particle rearrangement and reduces porosity | Higher pressure improves density; excessive pressure may damage material | Optimize pressure to achieve desired density without compromising material |
Particle Size | Determines sintering behavior | Smaller particles enhance densification; larger particles increase porosity | Use fine powders and control particle size distribution |
Composition | Influences sintering uniformity | Homogeneous compositions ensure even sintering; impurities cause defects | Maintain a controlled and homogeneous composition |
Atmosphere | Affects material-environment interaction | Inert/vacuum atmospheres prevent oxidation; air may cause contamination | Choose atmosphere based on material and desired properties |
Cooling Rate | Impacts final mechanical properties | Controlled cooling prevents thermal stresses and improves strength | Adjust cooling rate to optimize material performance |
Liquid Phase | Enhances densification in some processes | Improves bonding but excessive liquid phase causes grain growth | Carefully control liquid phase to balance densification and material integrity |
Unlock the full potential of your sintering process—contact our experts today for tailored solutions!