Brazing is a metal-joining process that uses a filler metal with a melting point above 840°F (450°C) but below the melting point of the base metals being joined. The choice of gas used during brazing is critical to ensure a strong, clean, and oxidation-free joint. Commonly used gases include inert gases like argon and helium, reducing gases like hydrogen, and mixtures such as dissociated ammonia or nitrogen-hydrogen blends. These gases create a protective atmosphere that prevents oxidation, scaling, and soot formation, ensuring a high-quality brazed joint. The selection of the appropriate gas depends on the materials being joined, the brazing method, and the desired finish.
Key Points Explained:
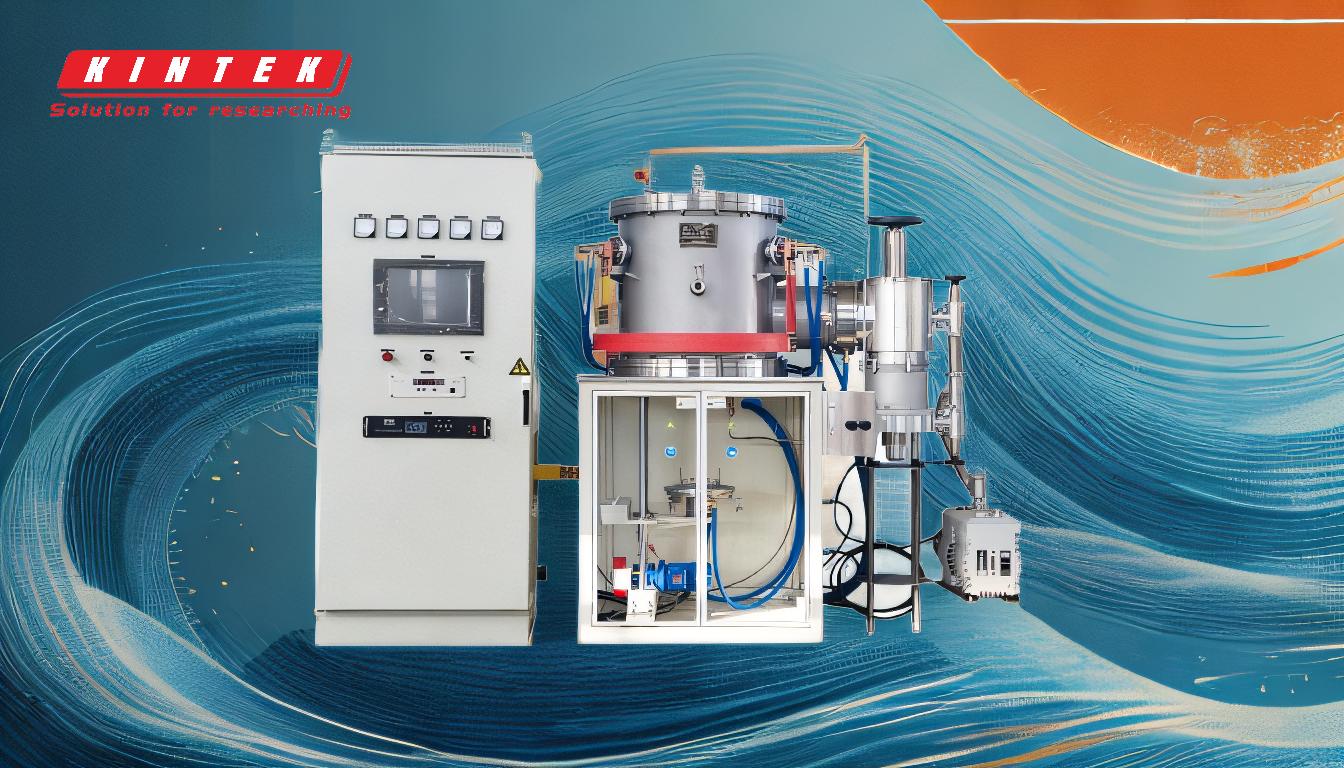
-
Purpose of Using Gas in Brazing:
- The primary purpose of using gas in brazing is to create a controlled atmosphere that prevents oxidation and contamination of the metal surfaces and filler material.
- Oxidation can weaken the joint and cause defects such as scaling or soot buildup, which negatively affect the appearance and performance of the brazed product.
- A clean atmosphere ensures proper wetting and flow of the filler metal, leading to strong and reliable joints.
-
Types of Gases Used in Brazing:
-
Inert Gases:
- Argon and helium are commonly used inert gases in brazing. They are chemically inactive and do not react with the metals or filler material.
- These gases are ideal for brazing materials that are highly reactive or sensitive to oxidation, such as titanium or certain stainless steels.
-
Reducing Gases:
- Hydrogen is a reducing gas that actively removes oxides from the metal surfaces, promoting a clean and bright finish.
- It is particularly effective for brazing copper, nickel, and some steels but requires careful handling due to its flammability.
-
Dissociated Ammonia:
- Dissociated ammonia (a mixture of hydrogen and nitrogen) is another reducing atmosphere used in brazing.
- It provides the benefits of hydrogen while diluting its flammability, making it safer to use in certain applications.
-
Nitrogen-Based Mixtures:
- Nitrogen-hydrogen blends are cost-effective and widely used for brazing stainless steels and other materials.
- These mixtures provide a protective atmosphere without the risks associated with pure hydrogen.
-
Exothermic and Endothermic Gases:
- Exothermic gases (e.g., nitrogen with small amounts of hydrogen and carbon monoxide) and endothermic gases (e.g., nitrogen-hydrogen-carbon monoxide mixtures) are used for specific applications, such as brazing carbon steels.
-
Inert Gases:
-
Factors Influencing Gas Selection:
-
Base Materials:
- The type of metals being joined determines the appropriate gas. For example, hydrogen is suitable for copper and nickel, while argon is better for reactive metals like titanium.
-
Brazing Method:
- Furnace brazing often uses inert or reducing atmospheres, while torch brazing may rely on flux to prevent oxidation.
-
Desired Finish:
- A clean, bright finish requires a reducing atmosphere like hydrogen or dissociated ammonia, whereas a vacuum or inert gas may suffice for less critical applications.
-
Cost and Safety:
- The cost of the gas and the safety considerations (e.g., flammability of hydrogen) also play a role in the selection process.
-
Base Materials:
-
Advantages of Using Protective Atmospheres:
- Prevents oxidation and scaling, ensuring a high-quality joint.
- Reduces the need for post-brazing cleaning, saving time and resources.
- Enhances the wetting and flow of the filler metal, improving joint strength and reliability.
-
Common Applications:
- Hydrogen and dissociated ammonia are often used in furnace brazing of stainless steels, copper, and nickel alloys.
- Argon and helium are preferred for brazing reactive metals like titanium and zirconium.
- Nitrogen-based mixtures are widely used in industrial brazing applications due to their cost-effectiveness and safety.
By carefully selecting the appropriate gas for brazing, manufacturers can achieve strong, clean, and reliable joints tailored to the specific requirements of the materials and application.
Summary Table:
Gas Type | Examples | Key Benefits | Common Applications |
---|---|---|---|
Inert Gases | Argon, Helium | Chemically inactive; prevents oxidation in reactive metals like titanium. | Brazing titanium, zirconium, and stainless steels. |
Reducing Gases | Hydrogen | Removes oxides; provides a clean, bright finish. | Brazing copper, nickel, and some steels. |
Dissociated Ammonia | Hydrogen-Nitrogen Mixture | Combines hydrogen's benefits with reduced flammability. | Furnace brazing of stainless steels and nickel alloys. |
Nitrogen-Based Mixtures | Nitrogen-Hydrogen Blends | Cost-effective; safe and protective atmosphere. | Industrial brazing of stainless steels and other metals. |
Exothermic/Endothermic Gases | Nitrogen-Hydrogen-CO Mixtures | Tailored for specific applications like carbon steel brazing. | Brazing carbon steels and other specialized materials. |
Need help selecting the right gas for your brazing process? Contact our experts today for tailored solutions!