In the Chemical Vapor Deposition (CVD) process, a variety of gases are used depending on the specific application and material being synthesized. The primary gases include methane (CH4) as a carbon source and hydrogen (H2) as a carrier and etching agent. Other gases such as nitrogen (N2), argon (Ar), carbon dioxide (CO2), silicon tetrachloride, methyl trichlorosilane, and ammonia (NH3) are also used in different CVD processes. These gases are delivered through precise gas and vapor delivery systems, which control their flow and composition to achieve the desired chemical reactions and material properties. The specific combination and ratio of gases vary depending on the type of material being deposited, such as diamond, silicon, or other compounds.
Key Points Explained:
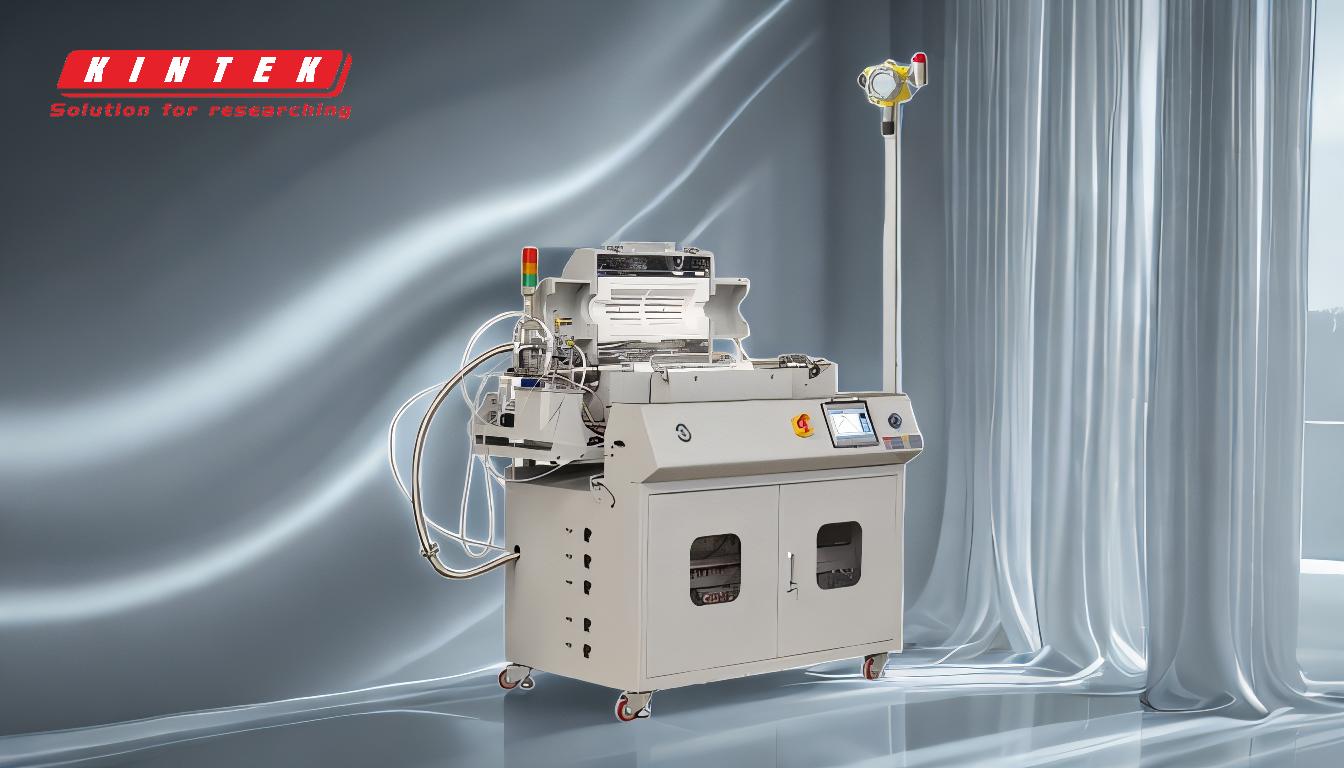
-
Primary Gases in CVD Processes:
- Methane (CH4): Methane is a common carbon source in CVD processes, particularly for diamond synthesis. It provides the carbon atoms necessary for the formation of diamond structures.
- Hydrogen (H2): Hydrogen is used both as a carrier gas and as an etching agent. It helps to selectively remove non-diamond carbon, ensuring the purity of the deposited diamond. Hydrogen is also used in high-temperature environments to activate the gas phase, enabling the necessary chemical reactions.
-
Carrier and Inert Gases:
- Nitrogen (N2): Nitrogen is often used as a carrier gas in CVD processes. It helps to transport the reactant gases to the reaction chamber and can also act as a diluent to control the reaction rate.
- Argon (Ar): Argon is another inert gas used in CVD. It provides a stable environment for the reaction and can help to control the pressure within the reaction chamber.
-
Reactive Gases:
- Carbon Dioxide (CO2): CO2 can be used in certain CVD processes as a source of carbon and oxygen. It is less common than methane but can be useful in specific applications.
- Ammonia (NH3): Ammonia is used in CVD processes that involve the deposition of nitride materials, such as silicon nitride (Si3N4). It provides the nitrogen atoms needed for these reactions.
-
Specialized Gases for Specific Applications:
- Silicon Tetrachloride (SiCl4): This gas is used in CVD processes for depositing silicon-based materials. It provides the silicon atoms necessary for the formation of silicon films.
- Methyl Trichlorosilane (CH3SiCl3): This compound is used in CVD processes for depositing silicon carbide (SiC) films. It provides both silicon and carbon atoms in the correct ratio for SiC formation.
-
Gas Delivery Systems:
- Mass Flow Controls: Precise control of gas flow rates is essential in CVD processes. Mass flow controllers (MFCs) are used to regulate the flow of each gas into the reaction chamber, ensuring the correct mixture and concentration of reactants.
- Modulating Valves: These valves are used to adjust the pressure and flow of gases within the system. They work in conjunction with MFCs to maintain the desired conditions for the CVD process.
-
Activation of Gases:
- High-Temperature Activation: In many CVD processes, the gases must be activated by high temperatures (often exceeding 2000°C) to break down the molecules into chemically active radicals. This is particularly important in diamond synthesis, where the high temperature ensures the formation of diamond rather than graphite.
- Microwave or Hot Filament Ionization: In some CVD systems, gases are ionized using microwaves or a hot filament. This ionization process generates the reactive species needed for the deposition of the desired material.
-
Variability in Gas Ratios:
- Dependent on Material Being Grown: The specific combination and ratio of gases used in CVD vary greatly depending on the type of material being deposited. For example, the ratio of methane to hydrogen in diamond synthesis is typically 1:99, but this can vary depending on the desired properties of the diamond.
By understanding the role of each gas and the importance of precise control in the CVD process, it becomes clear that the selection and management of gases are critical to achieving high-quality material deposition.
Summary Table:
Gas Type | Role in CVD | Common Applications |
---|---|---|
Methane (CH4) | Primary carbon source for diamond synthesis | Diamond film deposition |
Hydrogen (H2) | Carrier gas and etching agent; activates gas phase at high temperatures | Diamond purity control, gas activation |
Nitrogen (N2) | Carrier gas and diluent; controls reaction rate | Transporting reactant gases |
Argon (Ar) | Inert gas for stable reaction environments and pressure control | Pressure stabilization |
Carbon Dioxide (CO2) | Source of carbon and oxygen in specific applications | Specialized CVD processes |
Ammonia (NH3) | Provides nitrogen for nitride material deposition | Silicon nitride (Si3N4) synthesis |
Silicon Tetrachloride (SiCl4) | Silicon source for silicon-based material deposition | Silicon film formation |
Methyl Trichlorosilane (CH3SiCl3) | Silicon and carbon source for silicon carbide (SiC) deposition | Silicon carbide film synthesis |
Optimize your CVD process with the right gas combination—contact our experts today for personalized solutions!