The process of metal deposition involves creating a thin film of metal, such as aluminum, on a substrate like a silicon (Si) wafer. This is typically done using specialized equipment like an E-beam Evaporator. The process begins with preparing the substrate, followed by depositing the metal layer through techniques like evaporation or sputtering. The goal is to achieve a uniform, high-quality metal film that adheres well to the substrate, which is essential for applications in semiconductor manufacturing, electronics, and other industries.
Key Points Explained:
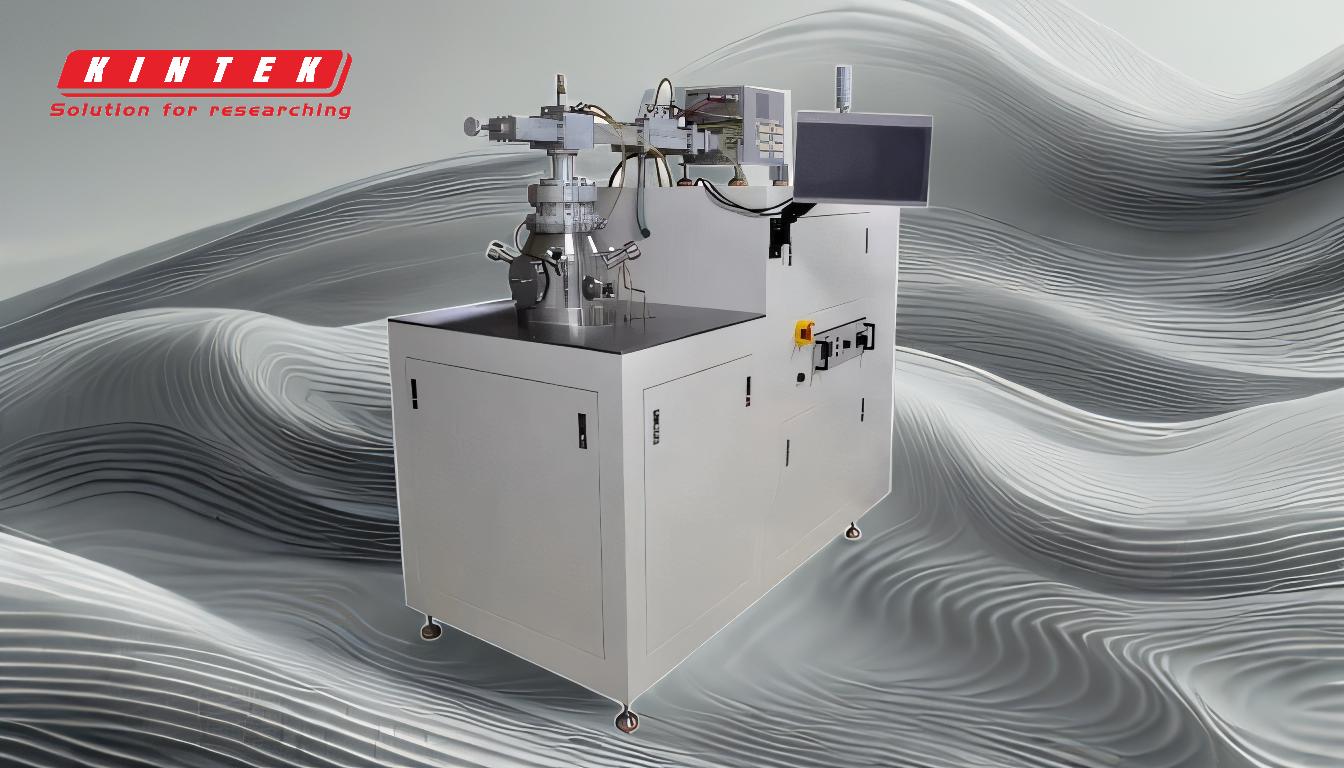
-
Substrate Preparation:
- The process begins with a clean and prepared substrate, often a silicon (Si) wafer. The substrate must be free of contaminants to ensure proper adhesion and uniformity of the metal film.
- Cleaning methods may include chemical cleaning, plasma cleaning, or other surface treatment techniques to remove any oxides, particles, or organic residues.
-
Metal Deposition Techniques:
- E-beam Evaporation: This is a common method for depositing metals like aluminum. In this process, a high-energy electron beam is focused on the target metal (e.g., aluminum), causing it to heat up and evaporate. The evaporated metal atoms then travel through a vacuum chamber and condense on the substrate, forming a thin film.
- Sputtering: Another technique where high-energy ions bombard the target metal, dislodging atoms that then deposit onto the substrate. This method is often used for more complex materials or when better film uniformity is required.
- Both methods are carried out in a vacuum to minimize contamination and ensure a clean deposition environment.
-
Equipment Used:
- E-beam Evaporator: A specialized tool for metal deposition, available in facilities like IMSE. It uses an electron beam to heat and evaporate the metal, which is then deposited onto the substrate.
- Vacuum Chamber: Essential for both evaporation and sputtering processes to maintain a controlled environment and prevent contamination.
-
Film Quality and Adhesion:
- The quality of the deposited metal film is critical. Factors like thickness uniformity, surface roughness, and adhesion strength are closely monitored.
- Adhesion promoters or intermediate layers may be used to improve the bonding between the metal film and the substrate.
-
Applications:
- Metal deposition is widely used in semiconductor manufacturing, where thin metal films are essential for creating interconnects, contacts, and other components in integrated circuits.
- It is also used in optics, solar cells, and various other industries where thin metal coatings are required.
-
Challenges and Considerations:
- Uniformity: Achieving a uniform film thickness across the entire substrate can be challenging, especially for large wafers.
- Contamination: Even small amounts of contamination can affect the performance of the metal film, so maintaining a clean environment is crucial.
- Stress and Defects: The deposition process can introduce stress or defects in the film, which may affect its electrical or mechanical properties.
By understanding these key points, a purchaser or user of equipment and consumables for metal deposition can make informed decisions about the processes and tools needed to achieve high-quality results.
Summary Table:
Key Aspect | Details |
---|---|
Substrate Preparation | Clean and prepare the substrate (e.g., Si wafer) using chemical or plasma cleaning. |
Deposition Techniques | E-beam evaporation or sputtering, both performed in a vacuum environment. |
Equipment | E-beam evaporator, vacuum chamber. |
Film Quality | Monitor thickness uniformity, surface roughness, and adhesion strength. |
Applications | Used in semiconductor manufacturing, optics, solar cells, and more. |
Challenges | Uniformity, contamination, and stress/defects in the film. |
Need high-quality metal deposition solutions? Contact our experts today to learn more!