CVD (Chemical Vapor Deposition) coating is a highly versatile and advanced technology used to deposit thin films or coatings onto substrates through chemical reactions in a controlled environment. This process involves the thermal decomposition or chemical reaction of precursor gases, which form a solid material on the substrate surface. CVD coatings are widely used in industries such as semiconductors, ceramics, mining, and jewelry due to their ability to produce high-purity, uniform, and durable coatings with precise control over properties at the atomic or nanometer scale. These coatings offer superior performance in applications requiring resistance to wear, corrosion, and high temperatures, making them indispensable in modern manufacturing and industrial processes.
Key Points Explained:
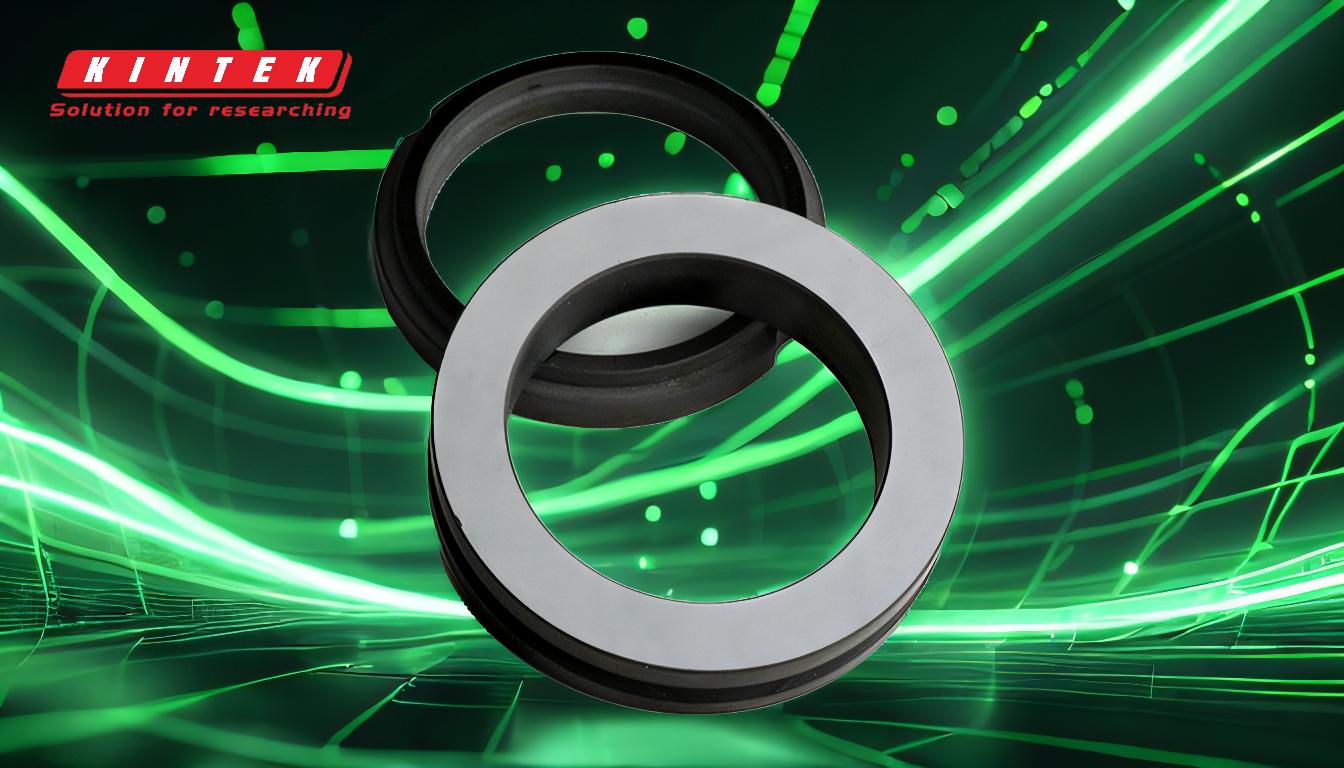
-
Definition of CVD Coating:
- CVD coating is a process where a thin film or coating is deposited onto a substrate through chemical reactions in a controlled environment. The precursor gases undergo thermal decomposition or chemical reactions, forming a solid material on the substrate surface. This technology is particularly effective for creating highly purified materials or coatings with controlled properties at the atomic or nanometer scale.
-
How CVD Coating Works:
- The CVD process involves introducing precursor gases into a reaction chamber where they interact with the substrate. The gases decompose or react chemically at high temperatures, depositing a solid material onto the substrate. This creates a metallurgical and diffusion-type bond between the coating and the substrate, which is stronger than the physical bond formed in processes like PVD (Physical Vapor Deposition).
-
Applications of CVD Coatings:
- CVD coatings are used across a wide range of industries due to their high quality and low porosity. Key applications include:
- Semiconductors: CVD is used to create high-performance thin films and conductive parts, essential for semiconductor manufacturing.
- Ceramics and Mining: CVD is critical for producing nanocomposite ceramic coatings, which are used in wear-resistant and high-temperature applications.
- Jewelry: CVD is employed to synthesize diamonds by depositing carbon atoms from precursor gases onto substrates.
- Machine Tools and Wear Components: CVD coatings provide excellent resistance to sliding friction wear-out and galling, making them ideal for metal-forming applications.
- CVD coatings are used across a wide range of industries due to their high quality and low porosity. Key applications include:
-
Advantages of CVD Coatings:
- High Purity and Uniformity: CVD coatings are known for their excellent purity and uniformity, making them suitable for applications requiring precise thin-film deposition.
- Strong Bonding: The metallurgical and diffusion-type bond formed in CVD coatings is much stronger than the physical bond created through PVD, enhancing durability and performance.
- Versatility: CVD can be used to deposit a wide range of materials, including metals, ceramics, and composites, making it adaptable to various industrial needs.
- Low Porosity: CVD coatings have low porosity, providing excellent protection against water, high temperatures, and corrosion.
-
Types of CVD Processes:
- LPCVD (Low-Pressure Chemical Vapor Deposition): Offers advantages such as low-temperature processing, high deposition rates, and the ability to produce high-quality, uniform films with excellent conformal step coverage. It is particularly useful for applications requiring precise thin-film deposition, such as in MEMS devices and semiconductor manufacturing.
- Other Variants: CVD processes can be tailored to specific needs, such as plasma-enhanced CVD (PECVD) or atmospheric pressure CVD (APCVD), depending on the application requirements.
-
Industrial Significance:
- CVD technology is advantageous for industrial production due to its relatively low manufacturing cost and high productivity. It is widely used in industries such as semiconductors, ceramics, mining, and jewelry, where high-performance coatings are essential for product functionality and durability.
In summary, CVD coatings are a cornerstone of modern manufacturing, offering unparalleled precision, durability, and versatility. Their ability to create high-quality, uniform, and durable coatings makes them indispensable in industries ranging from semiconductors to jewelry, ensuring the longevity and performance of critical components.
Summary Table:
Aspect | Details |
---|---|
Definition | Thin film deposition via chemical reactions in a controlled environment. |
Process | Precursor gases decompose or react, forming a solid coating on substrates. |
Applications | Semiconductors, ceramics, mining, jewelry, machine tools, wear components. |
Advantages | High purity, strong bonding, versatility, low porosity, durability. |
Types of CVD | LPCVD, PECVD, APCVD, tailored for specific industrial needs. |
Unlock the potential of CVD coatings for your industry—contact our experts today!