A microwave plasma reactor is a specialized device used in processes like chemical vapor deposition (CVD), where it generates plasma using microwave energy to facilitate chemical reactions. In the context of diamond synthesis, the reactor introduces gases like methane (CH4) and hydrogen (H2), sometimes with argon (Ar), oxygen (O2), or nitrogen (N2), into a vacuum chamber. High-voltage microwaves ionize these gases, creating a plasma state. This plasma interacts with a substrate to deposit diamond films or grow diamond crystals. The reactor is a critical tool in advanced material synthesis, offering precise control over the reaction environment.
Key Points Explained:
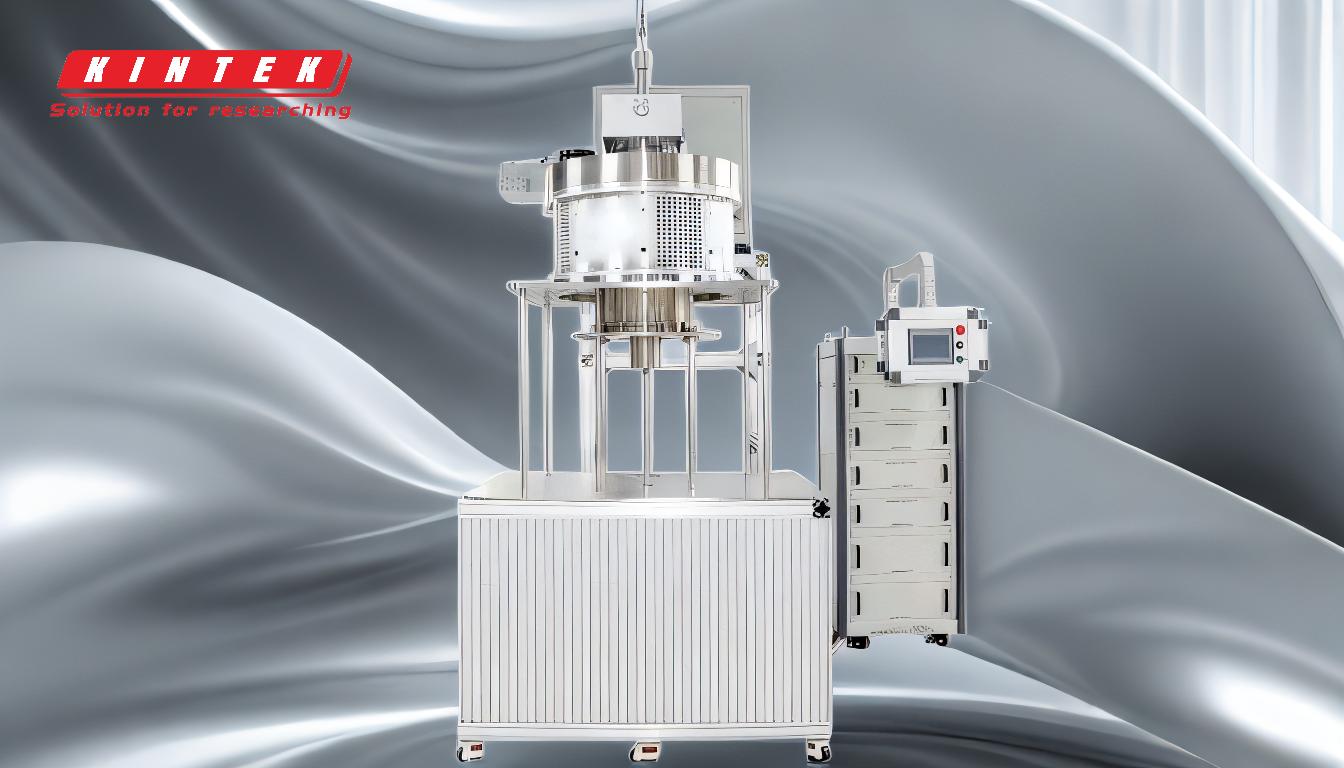
-
What is a Microwave Plasma Reactor?
- A microwave plasma reactor is a device that uses microwave energy to generate plasma, a highly ionized gas. This plasma is used to drive chemical reactions, particularly in processes like chemical vapor deposition (CVD). The reactor typically consists of a vacuum chamber, microwave generators, and gas delivery systems.
-
How Does It Work?
- The reactor operates by introducing specific gases into a vacuum chamber. For diamond synthesis, gases like methane (CH4) and hydrogen (H2) are commonly used. Additional gases such as argon (Ar), oxygen (O2), or nitrogen (N2) may be added depending on the desired outcome.
- High-voltage microwaves are then directed into the chamber. These microwaves ionize the gases, converting them into plasma. The plasma contains highly reactive species that interact with a substrate placed inside the chamber.
-
Role in Diamond Synthesis
- In diamond synthesis, the plasma reacts with the substrate to deposit carbon atoms in a crystalline form, resulting in the growth of diamond films or crystals. The process is highly controlled, allowing for the production of high-quality diamonds with specific properties.
-
Advantages of Microwave Plasma Reactors
- Precision Control: The reactor allows for precise control over the reaction environment, including gas composition, pressure, and temperature.
- Efficiency: Microwave energy efficiently ionizes gases, creating a stable plasma that enhances reaction rates.
- Versatility: The reactor can be used for various applications beyond diamond synthesis, such as coating materials, etching, and surface modification.
-
Applications Beyond Diamond Synthesis
- While diamond synthesis is a prominent application, microwave plasma reactors are also used in other fields:
- Material Coating: Depositing thin films of materials like silicon carbide or titanium nitride.
- Surface Treatment: Modifying surface properties of materials to enhance adhesion, hardness, or corrosion resistance.
- Environmental Applications: Breaking down pollutants or synthesizing advanced materials for energy storage.
- While diamond synthesis is a prominent application, microwave plasma reactors are also used in other fields:
-
Challenges and Considerations
- Complexity: The setup and operation of microwave plasma reactors require specialized knowledge and equipment.
- Cost: High initial investment and maintenance costs can be a barrier for some users.
- Safety: Handling high-voltage microwaves and reactive gases necessitates stringent safety protocols.
In summary, a microwave plasma reactor is a powerful tool for advanced material synthesis, particularly in diamond growth. Its ability to generate and control plasma using microwave energy makes it indispensable in research and industrial applications. However, its complexity and cost require careful consideration when selecting and operating such equipment.
Summary Table:
Aspect | Details |
---|---|
Function | Generates plasma using microwave energy for chemical reactions. |
Key Components | Vacuum chamber, microwave generators, gas delivery systems. |
Common Gases Used | Methane (CH4), Hydrogen (H2), Argon (Ar), Oxygen (O2), Nitrogen (N2). |
Applications | Diamond synthesis, material coating, surface treatment, environmental uses. |
Advantages | Precision control, efficiency, versatility. |
Challenges | High complexity, cost, and safety requirements. |
Ready to explore how a microwave plasma reactor can transform your material synthesis? Contact us today for expert guidance!