Reactive sputtering is a specialized thin-film deposition technique where a reactive gas, such as oxygen or nitrogen, is introduced into a sputtering chamber. This gas chemically reacts with the sputtered atoms from a target material, forming compounds like oxides or nitrides, which are then deposited onto a substrate as a thin film. This process allows for precise control over the film's composition and properties, making it essential for applications such as creating barrier layers, optical coatings, and semiconductor devices. The process involves careful management of parameters like gas flow rates, partial pressures, and plasma conditions to achieve desired stoichiometry and film characteristics.
Key Points Explained:
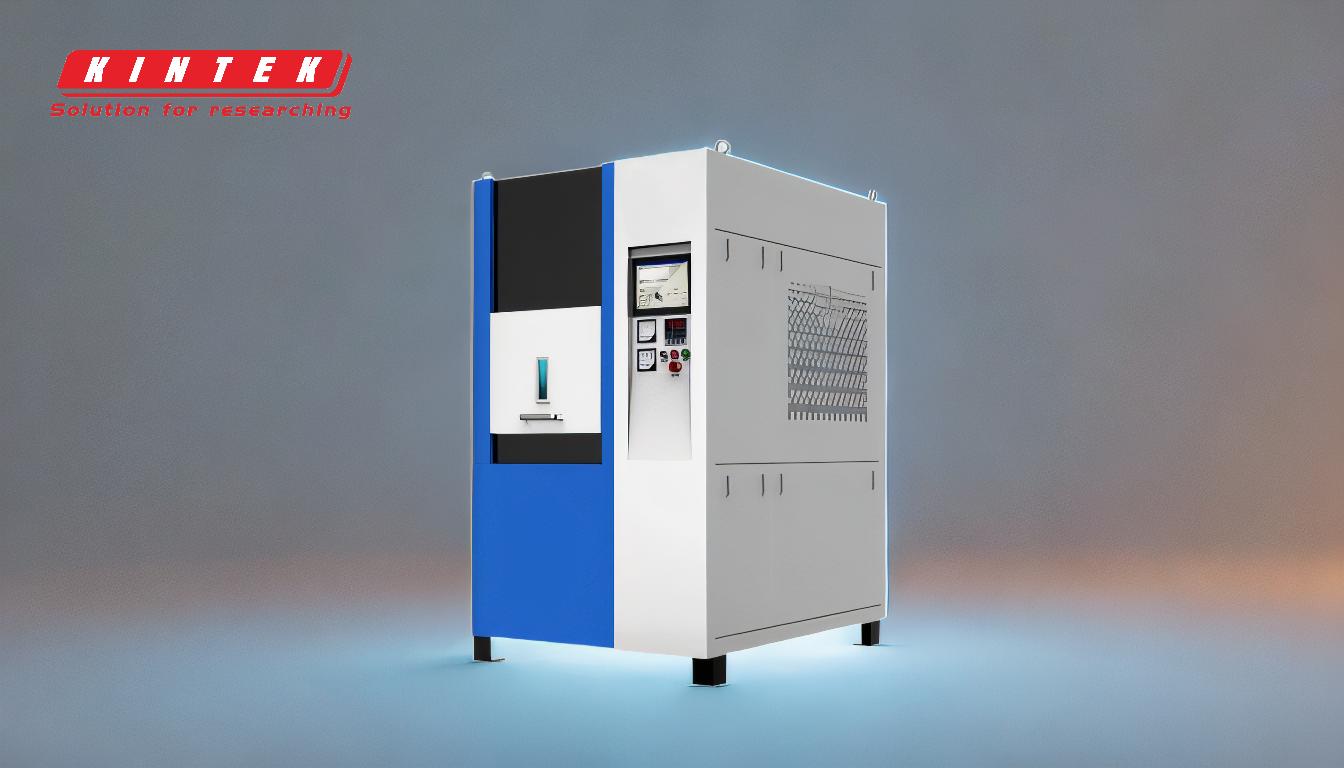
-
Definition of Reactive Sputtering:
- Reactive sputtering is a variant of the plasma sputtering process used to deposit thin films onto substrates.
- It involves introducing a reactive gas (e.g., oxygen, nitrogen) into the sputtering chamber, where it chemically reacts with the sputtered atoms from the target material.
- The resulting reaction products form a compound (e.g., titanium nitride, silicon oxide) that is deposited as a thin film on the substrate.
-
Key Components of the Process:
- Target Material: Typically an elemental material (e.g., titanium, silicon) that is sputtered to release atoms into the chamber.
- Reactive Gas: A gas like oxygen or nitrogen that reacts with the sputtered atoms to form a compound.
- Inert Gas: Often argon, used to create the plasma that sputters the target material.
- Substrate: The surface onto which the thin film is deposited.
-
Chemical Reaction Mechanism:
- The sputtered atoms from the target material collide with the reactive gas molecules in the plasma.
- A chemical reaction occurs, forming a new compound (e.g., titanium nitride or silicon oxide).
- This compound is then deposited onto the substrate as a thin film.
-
Control of Film Properties:
- Stoichiometry: The composition of the film can be controlled by adjusting the ratio of reactive gas to inert gas.
- Film Structure: Parameters like gas flow rates, partial pressures, and plasma conditions influence the film's structure and properties.
- Functional Properties: The process allows for optimization of properties such as stress, refractive index, and electrical conductivity.
-
Challenges and Considerations:
- Hysteresis Behavior: The introduction of a reactive gas can complicate the process, leading to non-linear behavior in film deposition rates and stoichiometry.
- Parameter Control: Precise control of gas flow rates, partial pressures, and plasma conditions is required to achieve desired film characteristics.
- Target Erosion: The Berg Model is often used to estimate the impact of reactive gases on target erosion and deposition rates.
-
Applications of Reactive Sputtering:
- Barrier Layers: Used in semiconductor manufacturing to create thin films that prevent diffusion of materials.
- Optical Coatings: Produces films with specific refractive indices for applications like anti-reflective coatings.
- Semiconductor Devices: Enables the deposition of precise thin films for electronic components.
-
Variants of Reactive Sputtering:
- DC Reactive Sputtering: Uses direct current to generate the plasma.
- HF (High-Frequency) Reactive Sputtering: Uses high-frequency alternating current, often for insulating materials.
By carefully managing the reactive sputtering process, manufacturers can produce thin films with tailored properties for a wide range of industrial and technological applications.
Summary Table:
Aspect | Details |
---|---|
Definition | A thin-film deposition technique using reactive gases to form compounds. |
Key Components | Target material, reactive gas (e.g., oxygen, nitrogen), inert gas, substrate. |
Applications | Barrier layers, optical coatings, semiconductor devices. |
Challenges | Hysteresis behavior, precise parameter control, target erosion. |
Variants | DC Reactive Sputtering, HF Reactive Sputtering. |
Discover how reactive sputtering can enhance your manufacturing process—contact our experts today for tailored solutions!