A rotary heat type furnace, often referred to as a rotary tube furnace, is a specialized heating device designed for various thermal processing applications. It operates by rotating the furnace tube, which ensures uniform heating and thorough mixing of materials. This design is particularly beneficial for processes like material sintering, coating preparation, chemical reactions, and heat treatment. The furnace can be tilted and rotated 360°, and it supports the introduction of various gases or vacuum conditions, making it versatile for different industrial and laboratory applications. The continuous movement of materials within the furnace enhances gas diffusion, reduces gas consumption, and improves heat treatment efficiency, making it a reliable and efficient tool for achieving consistent and high-quality results.
Key Points Explained:
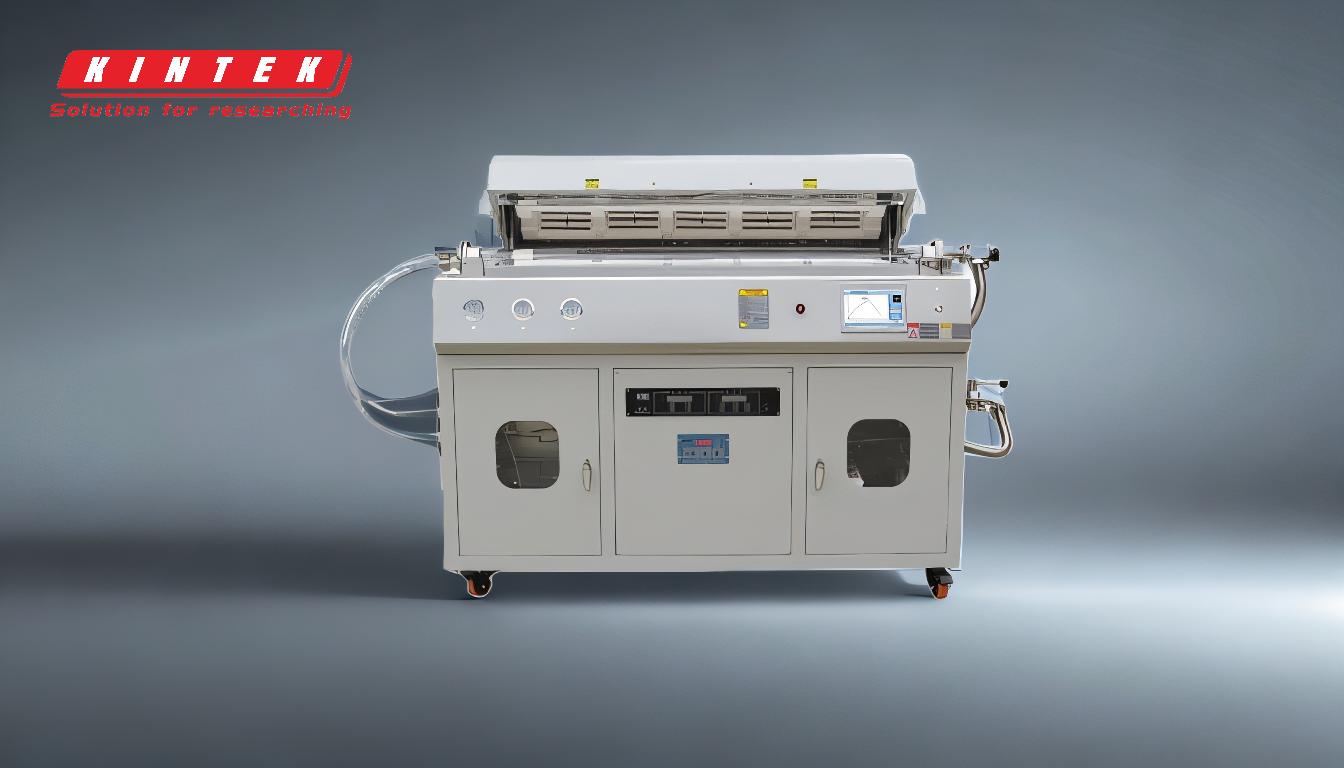
-
Design and Operation of a Rotary Heat Type Furnace
- A rotary heat type furnace, or rotating furnace, features a rotating furnace tube that ensures materials are evenly heated and processed.
- The furnace body can be tilted, and the furnace tube can rotate 360°, allowing for precise control over the heating process.
- It supports the introduction of gases like nitrogen, argon, and hydrogen, or can operate under vacuum conditions using an external vacuum pump.
-
Key Applications
- Material Sintering: Used for sintering ceramics and metal powders to improve density, strength, and corrosion resistance.
- Coating Preparation: Ideal for creating ceramic or metal coatings on substrates to enhance wear resistance, corrosion resistance, and aesthetics.
- Chemical Reactions: Facilitates the synthesis of new materials or the preparation of catalysts.
- Heat Treatment and Annealing: Improves the structure and performance of metal materials through controlled heating and cooling processes.
-
Advantages of Rotary Heat Type Furnaces
- Uniform Heating: The rotational motion ensures materials are fully mixed, reducing temperature gradients and improving heat treatment effects.
- Versatility: Suitable for heating various materials, including powders, granules, and solids.
- Efficiency: Continuous movement of materials enhances gas diffusion, reduces gas consumption, and increases heat treatment efficiency.
- Precision: Equipped with a computer control system for accurate temperature control, ensuring high-quality results.
-
Industrial and Laboratory Use
- In industrial settings, rotary tube furnaces offer quicker heating times, improved operating conditions, and decreased fuel consumption.
- In laboratories, they are used for processes like lithium battery material preparation, where uniform heating and consistent results are critical.
-
Comparison with Other Furnace Types
- Unlike static furnaces, rotary tube furnaces ensure that the entire surface area of materials is exposed to the atmosphere, improving heat treatment efficiency.
- Features like multiple temperature zones, optional atmospheres, and vacuum compatibility make them more versatile than traditional furnaces.
-
Safety and Reliability
- Rotary heat type furnaces are designed to be safe and reliable, with simple operation and high temperature control accuracy.
- They have a large temperature range, excellent insulation, and high furnace temperature uniformity, ensuring consistent and repeatable results.
By combining rotational motion with precise temperature control and versatile operating conditions, rotary heat type furnaces are an essential tool for achieving high-quality thermal processing in both industrial and laboratory settings.
Summary Table:
Aspect | Details |
---|---|
Design | Rotating furnace tube, 360° rotation, tiltable, supports gases or vacuum. |
Applications | Sintering, coating preparation, chemical reactions, heat treatment. |
Advantages | Uniform heating, versatility, efficiency, precision, and reliability. |
Industrial Use | Quicker heating, improved conditions, reduced fuel consumption. |
Laboratory Use | Lithium battery material preparation, uniform heating, consistent results. |
Safety Features | Simple operation, high temperature control accuracy, excellent insulation. |
Ready to enhance your thermal processing? Contact us today to learn more about rotary heat type furnaces!