A three-up mold, also known as a three-plate mold, is a specialized type of injection molding tool designed to separate the runner system (the channels through which molten plastic flows) from the finished part. This design allows for automatic removal of the runner system and the finished part in separate stages during the mold-opening process. It is particularly useful for multi-cavity molds or when producing parts with complex geometries, as it ensures efficient material usage and reduces manual labor in runner removal. The mold consists of three plates: the fixed plate (attached to the injection molding machine), the runner plate (where the runner system is located), and the moving plate (where the finished part is formed). This configuration enables precise control over the ejection process and improves production efficiency.
Key Points Explained:
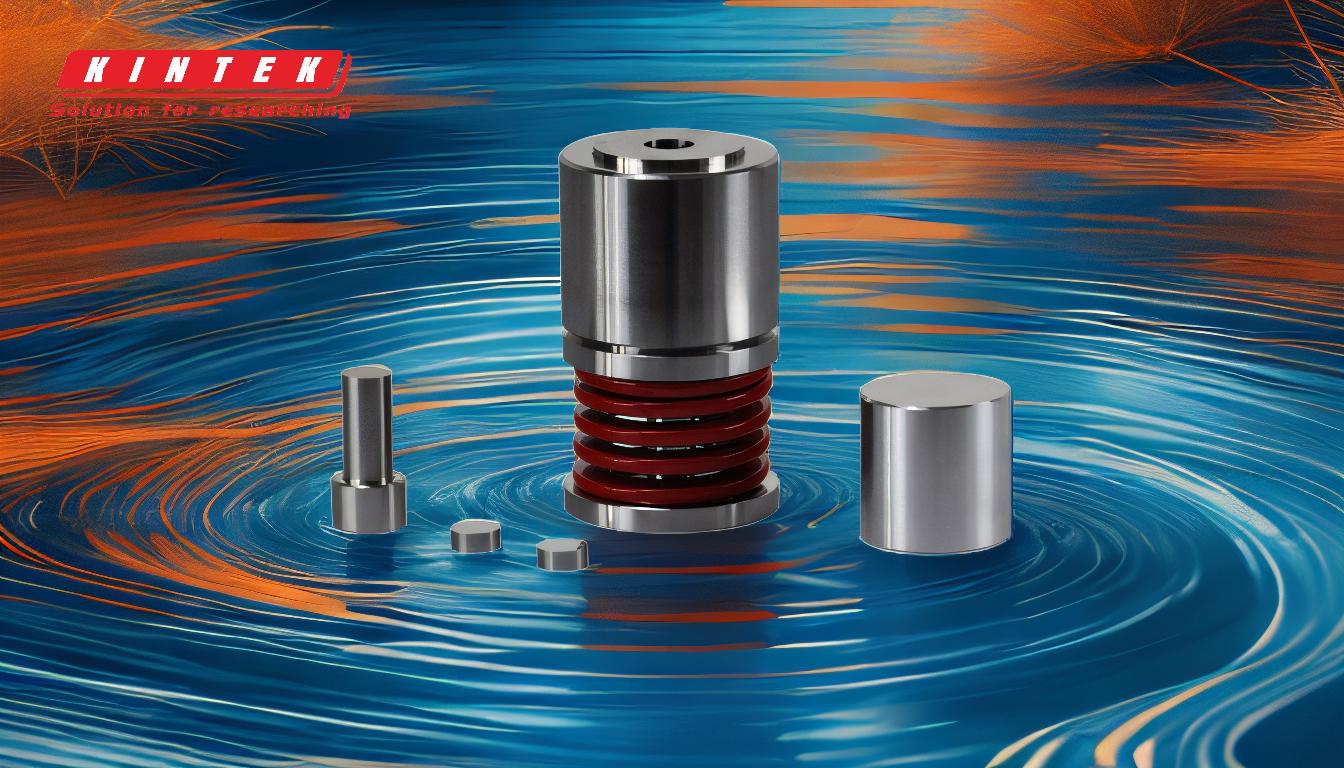
-
Definition and Purpose of a Three-Up Mold:
- A three-up mold is a type of injection molding tool that uses a cold runner system.
- Its primary purpose is to separate the runner system (waste material) from the finished part, allowing both to be ejected independently during the mold-opening process.
- This design is ideal for high-volume production, multi-cavity molds, and parts requiring precise ejection.
-
Structure of a Three-Up Mold:
- The mold consists of three main plates:
- Fixed Plate: Attached to the injection molding machine, it holds the sprue (the entry point for molten plastic).
- Runner Plate: Contains the runner system, which distributes molten plastic to the cavities.
- Moving Plate: Houses the cavities where the finished parts are formed.
- These plates are designed to open in a specific sequence to separate the runner and the finished part.
- The mold consists of three main plates:
-
How It Works:
- During the injection molding process, molten plastic flows through the sprue into the runner system on the runner plate.
- The plastic then fills the cavities on the moving plate to form the finished parts.
- When the mold opens, the fixed plate and runner plate separate first, allowing the runner system to be ejected.
- Next, the runner plate and moving plate separate, enabling the finished parts to be ejected separately.
-
Advantages of a Three-Up Mold:
- Automatic Runner Removal: Eliminates the need for manual runner separation, reducing labor costs.
- Material Efficiency: Minimizes material waste by reusing the runner system in some cases.
- Versatility: Suitable for complex parts and multi-cavity molds.
- Improved Ejection: Ensures clean and precise ejection of both runners and finished parts.
-
Applications:
- Commonly used in industries requiring high precision and efficiency, such as automotive, electronics, and consumer goods.
- Ideal for producing small, intricate parts or components with multiple cavities.
-
Comparison with Two-Plate Molds:
- Unlike two-plate molds, which combine the runner system and finished part ejection, three-up molds provide a dedicated mechanism for separating the two.
- This separation reduces the risk of damage to the finished parts and improves overall production efficiency.
By understanding the structure, functionality, and benefits of a three-up mold, manufacturers can make informed decisions about its use in their injection molding processes, ensuring optimal efficiency and quality in production.
Summary Table:
Aspect | Details |
---|---|
Definition | A three-plate injection mold separating runners and finished parts. |
Structure | Fixed plate, runner plate, and moving plate for precise ejection. |
Advantages | Automatic runner removal, material efficiency, and improved ejection. |
Applications | Automotive, electronics, and consumer goods industries. |
Comparison | Superior to two-plate molds for complex parts and multi-cavity designs. |
Optimize your injection molding process with a three-up mold—contact our experts today!