Hydraulic presses are versatile machines used across multiple industries for tasks like forging, metal forming, and molding. However, there are alternatives to hydraulic presses that can be considered depending on the specific application, material, and operational requirements. These alternatives include mechanical presses, pneumatic presses, servo-electric presses, and even manual presses. Each alternative has its own advantages and limitations, making it essential to evaluate factors such as force requirements, precision, speed, and cost-effectiveness when choosing the right equipment.
Key Points Explained:
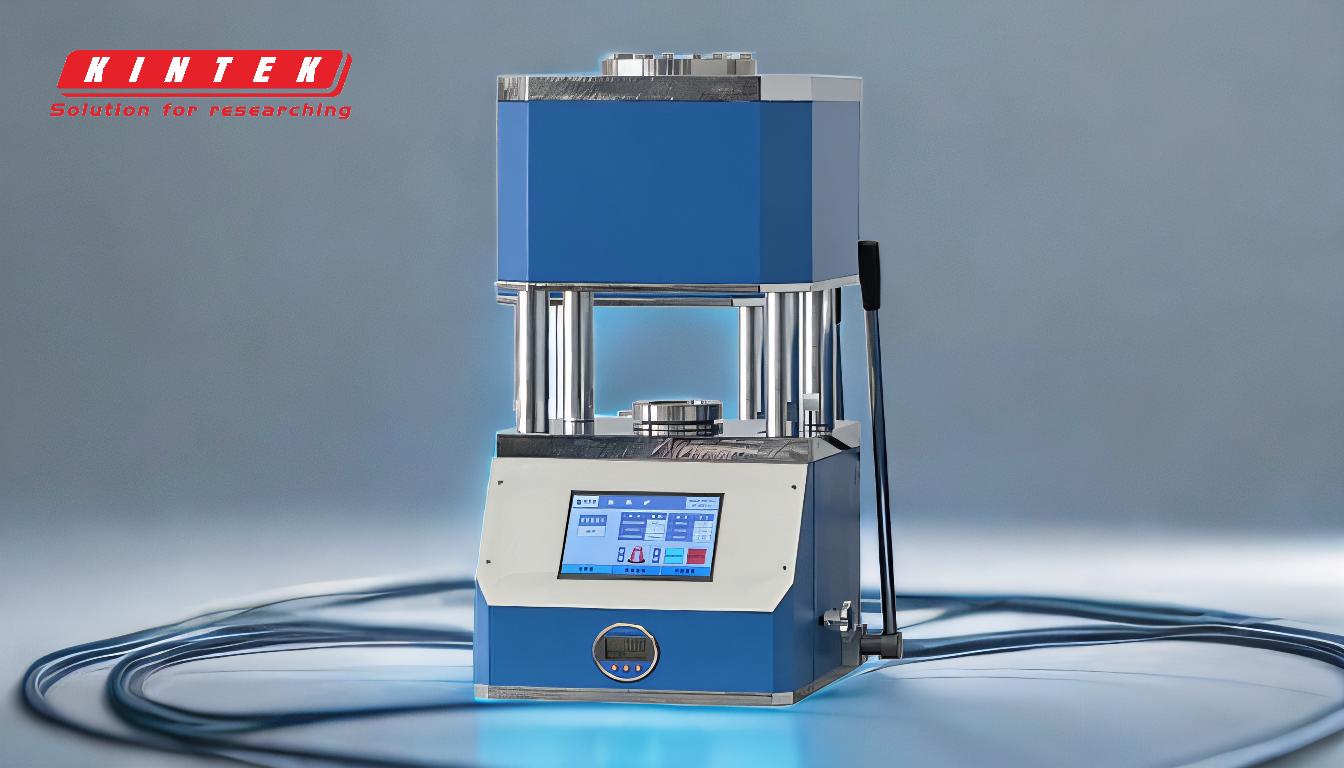
-
Mechanical Presses:
- How They Work: Mechanical presses use a motor-driven flywheel to generate force, which is transferred through a crankshaft or eccentric mechanism to the ram.
-
Advantages:
- High speed and efficiency for repetitive tasks.
- Suitable for high-volume production.
- Lower operating costs compared to hydraulic presses.
-
Limitations:
- Limited force control and precision.
- Not ideal for applications requiring variable force or stroke length.
- Applications: Commonly used in stamping, blanking, and punching operations.
-
Pneumatic Presses:
- How They Work: Pneumatic presses use compressed air to generate force, which is applied through a piston or diaphragm.
-
Advantages:
- Clean and quiet operation.
- Suitable for light to medium force applications.
- Easy to maintain and operate.
-
Limitations:
- Limited force compared to hydraulic systems.
- Requires a steady supply of compressed air.
- Applications: Ideal for assembly, riveting, and light pressing tasks.
-
Servo-Electric Presses:
- How They Work: Servo-electric presses use electric motors and precision ball screws to generate force, with programmable control over speed, force, and position.
-
Advantages:
- High precision and repeatability.
- Energy-efficient and environmentally friendly.
- Programmable for complex operations.
-
Limitations:
- Higher initial cost compared to hydraulic presses.
- Limited force capacity for heavy-duty applications.
- Applications: Suitable for applications requiring precise control, such as electronics assembly, medical device manufacturing, and small-part pressing.
-
Manual Presses:
- How They Work: Manual presses rely on human force, often through a lever or screw mechanism, to apply pressure.
-
Advantages:
- Low cost and simple design.
- No need for external power sources.
-
Limitations:
- Limited force and precision.
- Labor-intensive and not suitable for high-volume production.
- Applications: Useful for small-scale or low-force tasks, such as sample preparation or small repairs.
-
Comparison with Hydraulic Hot Press Machines:
- Hydraulic hot press machines are specialized for applications requiring both high force and controlled heating, such as in thermoplastic molding or composite material production. Alternatives like mechanical or servo-electric presses may not provide the same combination of force and heat control. However, for applications that do not require heating, the alternatives mentioned above can be viable replacements.
-
Choosing the Right Alternative:
- Force Requirements: Determine the maximum force needed for your application. Hydraulic presses excel in high-force applications, but mechanical or servo-electric presses may suffice for lighter tasks.
- Precision and Control: If your application requires precise control over force, speed, or position, servo-electric presses are a strong alternative.
- Operational Environment: Consider factors like noise, maintenance, and energy efficiency. Pneumatic and servo-electric presses offer cleaner and quieter operations compared to hydraulic systems.
- Cost Considerations: Evaluate both the initial investment and long-term operating costs. While hydraulic presses may have lower upfront costs, alternatives like servo-electric presses can offer savings in energy and maintenance over time.
By carefully assessing your specific needs and comparing the capabilities of each alternative, you can find the right solution to replace or complement a hydraulic hot press machine in your operations.
Summary Table:
Alternative | How It Works | Advantages | Limitations | Applications |
---|---|---|---|---|
Mechanical Presses | Uses a motor-driven flywheel and crankshaft to generate force. | High speed, efficiency, and lower operating costs. | Limited force control and precision. | Stamping, blanking, and punching operations. |
Pneumatic Presses | Uses compressed air to generate force via a piston or diaphragm. | Clean, quiet, and easy to maintain. | Limited force and requires a steady air supply. | Assembly, riveting, and light pressing tasks. |
Servo-Electric Presses | Uses electric motors and ball screws for programmable force and speed control. | High precision, energy-efficient, and programmable. | Higher initial cost and limited force for heavy-duty tasks. | Electronics assembly, medical device manufacturing, and small-part pressing. |
Manual Presses | Relies on human force through a lever or screw mechanism. | Low cost and simple design. | Limited force, precision, and labor-intensive. | Small-scale tasks like sample preparation or repairs. |
Need help choosing the right press for your application? Contact our experts today for personalized advice!