Atomic Layer Deposition (ALD) is a highly precise thin-film deposition technique that allows for atomic-level control over film thickness, density, and conformality. It operates through sequential, self-limiting chemical reactions between gas-phase precursors and the substrate surface. ALD is widely used in industries such as semiconductors, where it is essential for producing nanomaterials, and in biomedical applications like tissue engineering. Examples of materials deposited using ALD include Alumina oxide (Al2O3), Hafnium oxide (HfO2), and Titanium oxide (TiO2). The process involves alternating pulses of precursors separated by purge steps, ensuring uniform and conformal film growth even on high-aspect-ratio structures.
Key Points Explained:
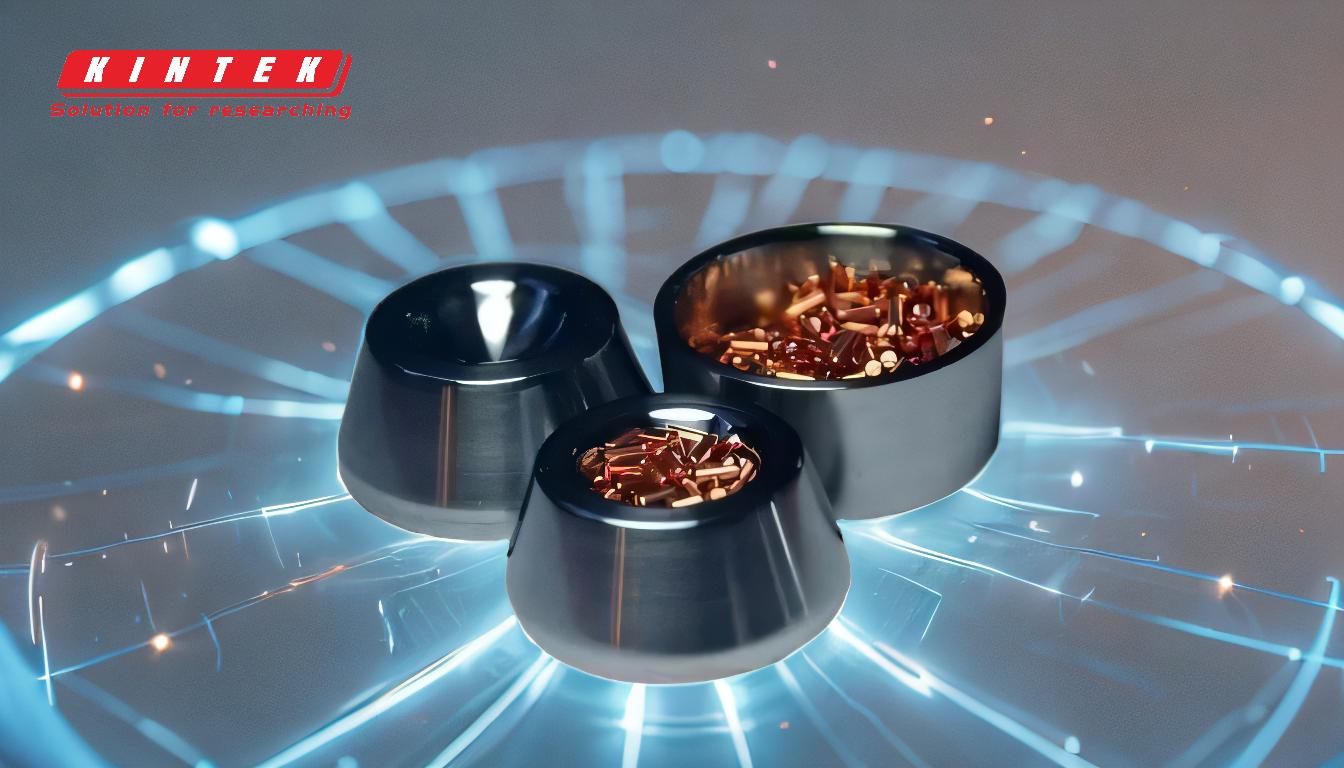
-
Definition and Process of ALD:
- ALD is a subset of Chemical Vapor Deposition (CVD) that enables the deposition of ultra-thin films with atomic-level precision.
- The process involves sequential, self-limiting chemical reactions between gas-phase precursors and the substrate surface.
- Precursors are introduced into the reaction chamber in alternating pulses, separated by purge steps to remove excess reactants and by-products.
-
Key Features of ALD:
- Precision and Uniformity: ALD provides exceptional control over film thickness, often achieving layers thinner than 10nm with high uniformity.
- Conformality: ALD films are highly conformal, capable of covering complex geometries and high-aspect-ratio structures (up to 2000:1).
- Repeatability: The process is highly repeatable, ensuring consistent results across multiple cycles.
- Pinhole-Free Layers: ALD produces dense, defect-free films, making it ideal for applications requiring high-quality coatings.
-
Examples of Materials Deposited via ALD:
- Alumina Oxide (Al2O3): Used as a dielectric layer in semiconductors and as a protective coating in various applications.
- Hafnium Oxide (HfO2): Commonly employed in high-k dielectric layers for advanced semiconductor devices.
- Titanium Oxide (TiO2): Utilized in applications such as photocatalysis, solar cells, and biomedical coatings.
-
Applications of ALD:
- Semiconductor Industry: ALD is critical for manufacturing nanomaterials, gate oxides, and memory devices due to its precision and uniformity.
- Biomedical Applications: ALD is used in tissue engineering and drug delivery systems, where controlled surface properties are essential.
- Energy and Optics: ALD is employed in solar cells, fuel cells, and optical coatings, benefiting from its ability to deposit uniform and conformal films.
-
Advantages of ALD:
- Atomic-Level Control: ALD allows for precise control over film thickness at the atomic scale.
- Versatility: It can deposit a wide range of materials, including oxides, nitrides, and metals.
- Scalability: ALD is compatible with large-scale production, making it suitable for industrial applications.
-
Limitations of ALD:
- Slow Deposition Rates: ALD is inherently slower than other deposition techniques due to its sequential nature.
- High Cost: The equipment and precursors used in ALD can be expensive, limiting its use in cost-sensitive applications.
- Complexity: The process requires careful optimization of precursor chemistry and reaction conditions.
-
Future Prospects of ALD:
- Emerging Applications: ALD is being explored for use in flexible electronics, quantum computing, and advanced energy storage systems.
- Material Innovations: Research is ongoing to develop new precursors and reaction chemistries to expand the range of materials that can be deposited via ALD.
- Process Optimization: Advances in ALD equipment and process control are expected to improve deposition rates and reduce costs, making the technique more accessible.
In summary, Atomic Layer Deposition is a powerful and versatile technique for depositing ultra-thin, high-quality films with atomic-level precision. Its applications span multiple industries, from semiconductors to biomedicine, and its unique features, such as conformality and repeatability, make it indispensable for advanced manufacturing processes. Despite its limitations, ongoing research and technological advancements continue to expand the potential of ALD in emerging fields.
Summary Table:
Aspect | Details |
---|---|
Definition | A subset of CVD for ultra-thin film deposition with atomic-level precision. |
Key Features | Precision, uniformity, conformality, repeatability, pinhole-free layers. |
Materials Deposited | Alumina oxide (Al2O3), Hafnium oxide (HfO2), Titanium oxide (TiO2). |
Applications | Semiconductors, biomedicine, energy, optics. |
Advantages | Atomic-level control, versatility, scalability. |
Limitations | Slow deposition rates, high cost, process complexity. |
Future Prospects | Flexible electronics, quantum computing, advanced energy storage. |
Learn how ALD can revolutionize your industry—contact our experts today!