Physical Vapor Deposition (PVD) and Chemical Vapor Deposition (CVD) are two widely used thin-film deposition techniques with distinct processes and applications. PVD involves vaporizing a solid material in a vacuum and depositing it onto a substrate, while CVD uses chemical reactions of gaseous precursors to form a thin film on a substrate. PVD is commonly used in industries like electronics, automotive, and fashion for coatings that enhance reflectivity, durability, or aesthetics. CVD, on the other hand, excels in applications requiring conformal coatings, such as integrated circuits, wear-resistant coatings, and gas sensing. Both techniques are essential in modern manufacturing, offering unique advantages depending on the application.
Key Points Explained:
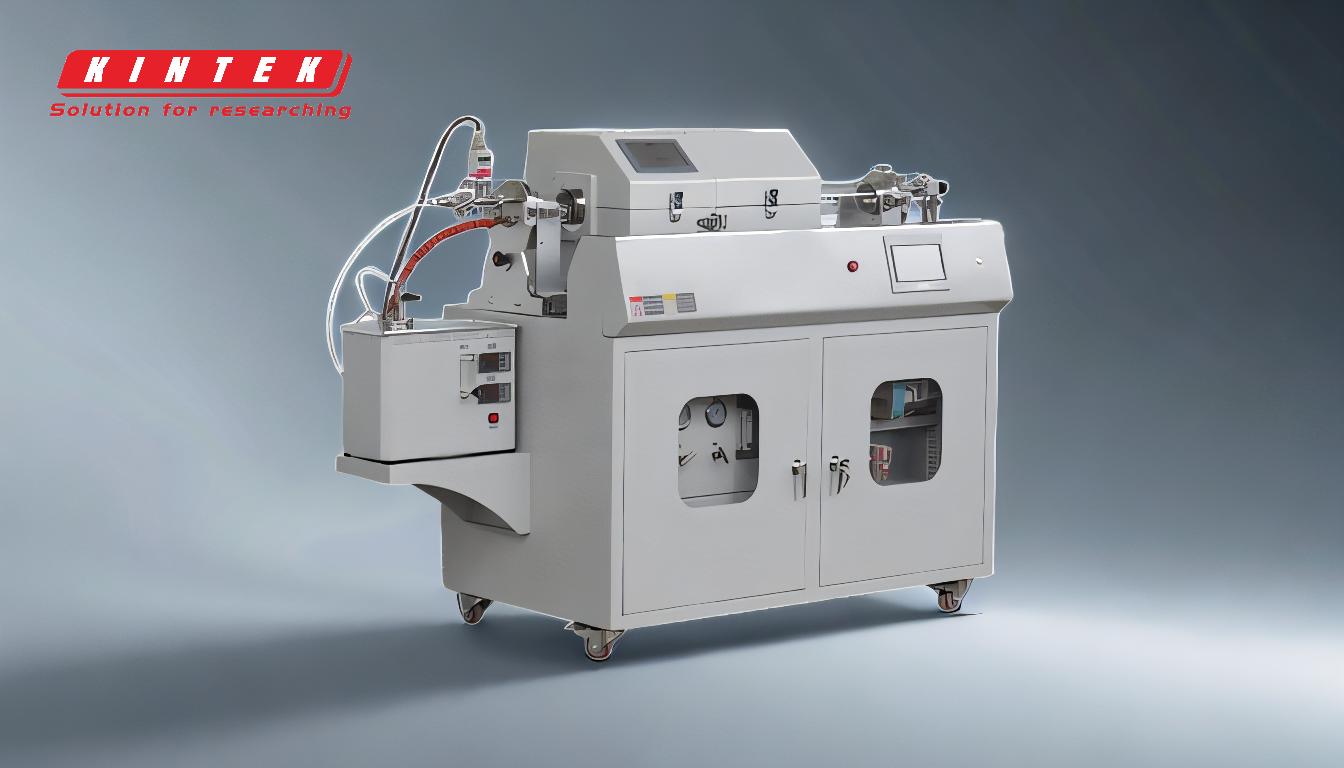
-
Definition and Process of PVD and CVD:
- PVD: Involves vaporizing a solid material in a vacuum environment and depositing it onto a substrate. This process is typically used for creating thin films that enhance properties like reflectivity, hardness, or corrosion resistance.
- CVD: Involves heating a gaseous precursor, which then reacts and condenses on a substrate to form a thin film. This method is ideal for depositing conformal coatings on complex geometries or irregular surfaces.
-
Examples of PVD Applications:
- Electronics: Used for aluminum tracks and ceramic resistors in electronic circuitry.
- Optics: Anti-reflective ceramic coatings for lenses and mirrors.
- Automotive: Corrosion-resistant coatings for gas turbine blades and wear-resistant coatings for mechanical tools.
- Fashion and Home Furnishings: Decorative coatings on jewelry, faucets, and utensils.
-
Examples of CVD Applications:
- Integrated Circuits: Used for depositing thin films in semiconductor manufacturing.
- Wear-Resistant Coatings: Applied to tools and machinery to improve durability.
- Gas Sensing: Thin films used in sensors for detecting specific gases.
- Photovoltaic Devices: Coatings for solar panels to enhance efficiency.
-
Advantages of CVD Over PVD:
- Higher Pressure Operation: CVD operates at higher pressures, eliminating the need for expensive high-vacuum pumps.
- Conformal Coatings: CVD can deposit uniform films on irregular surfaces or densely packed substrates due to its laminar flow properties.
- Cost Efficiency: Reduced infrastructure costs when toxic gas management is not required.
-
Types of CVD Equipment:
- Atmospheric Pressure CVD (APCVD): Operates at atmospheric pressure, suitable for large-scale production.
- Low Pressure CVD (LPCVD): Operates at reduced pressure, providing better film uniformity.
- Plasma-Enhanced CVD (PECVD): Uses plasma to enhance chemical reactions, allowing for lower deposition temperatures.
-
Comparison of PVD and CVD:
- PVD: Better for applications requiring high-purity films and line-of-sight deposition.
- CVD: Superior for conformal coatings and applications involving complex geometries.
By understanding the distinct processes, applications, and advantages of PVD and CVD, manufacturers can choose the appropriate technique based on their specific needs, whether it’s for enhancing durability, improving reflectivity, or achieving precise thin-film deposition.
Summary Table:
Aspect | PVD | CVD |
---|---|---|
Process | Vaporizes solid material in a vacuum and deposits it onto a substrate. | Uses chemical reactions of gaseous precursors to form a thin film. |
Applications | Electronics, optics, automotive, fashion, and home furnishings. | Integrated circuits, wear-resistant coatings, gas sensing, solar panels. |
Advantages | High-purity films, line-of-sight deposition. | Conformal coatings, uniform films on complex geometries, cost efficiency. |
Example Applications | Aluminum tracks, anti-reflective coatings, decorative jewelry coatings. | Semiconductor manufacturing, gas sensors, photovoltaic devices. |
Need help choosing between PVD and CVD for your application? Contact our experts today for tailored solutions!