Sputtering is a versatile physical vapor deposition (PVD) technique used to deposit thin films of materials onto substrates. It involves the ejection of atoms from a target material by bombarding it with high-energy ions, typically from a noble gas like argon. This process is widely used in industries such as microelectronics, optoelectronics, and solar cell manufacturing. Sputtering can be categorized into various types, including DC, RF, MF, pulsed DC, and HiPIMS, each suited for specific applications. Common materials deposited through sputtering include aluminum, copper, titanium, gold, and indium tin oxide, which are critical for creating functional coatings and devices.
Key Points Explained:
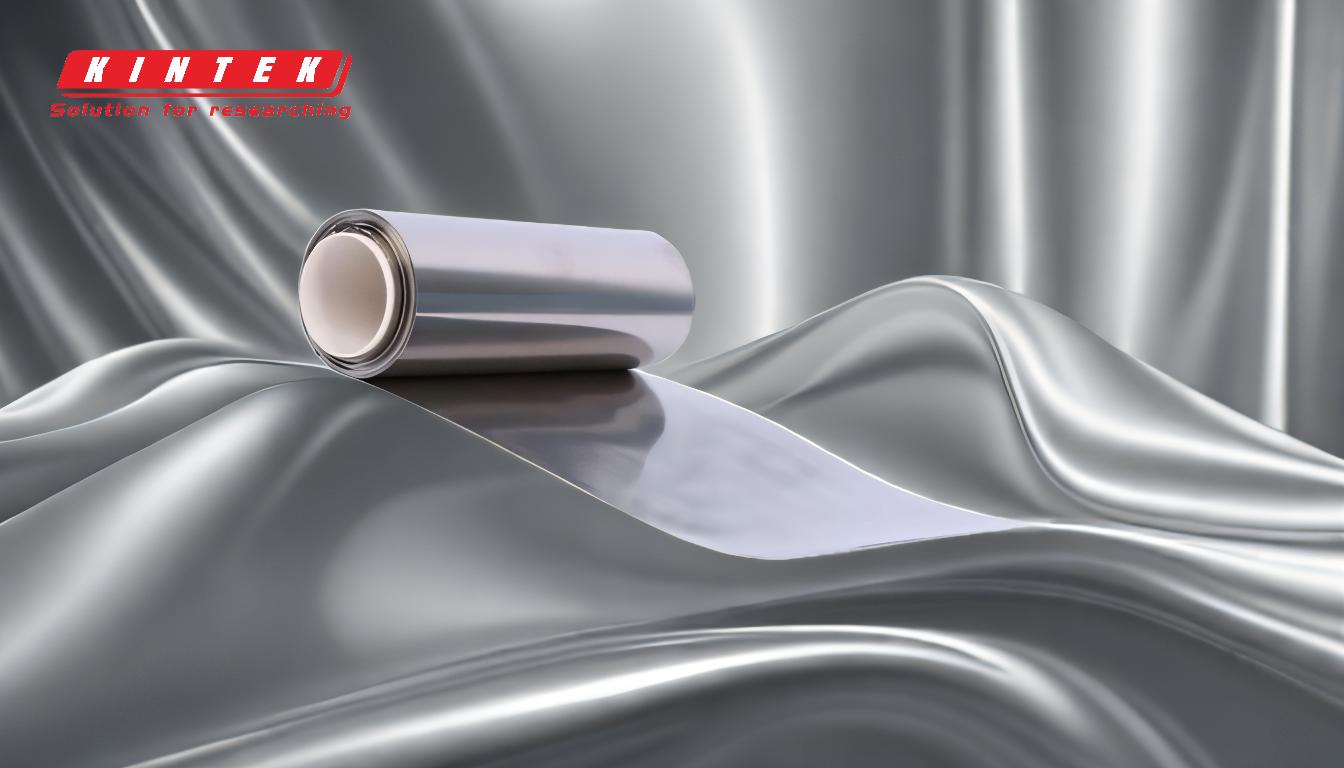
-
What is Sputtering?
- Sputtering is a PVD technique where a target material is bombarded with high-energy ions, causing atoms to be ejected and deposited onto a substrate. This process is facilitated by creating a plasma in a vacuum chamber, typically using a noble gas like argon. The ejected atoms form a thin film on the substrate, which can be used in various applications such as microelectronics, solar cells, and optoelectronics.
-
Types of Sputtering Processes
- Direct Current (DC) Sputtering: This is the most basic form of sputtering, where a DC power supply is used to generate the plasma. It is commonly used for conductive materials like metals.
- Radio Frequency (RF) Sputtering: RF sputtering is used for insulating materials. The alternating current prevents charge buildup on the target, making it suitable for materials like oxides.
- Mid-Frequency (MF) Sputtering: This method is a hybrid between DC and RF sputtering, offering better control over the deposition process.
- Pulsed DC Sputtering: This technique uses pulsed power to reduce arcing and improve film quality, especially for reactive sputtering processes.
- High-Power Impulse Magnetron Sputtering (HiPIMS): HiPIMS delivers high power in short pulses, producing dense and high-quality films with excellent adhesion.
-
Applications of Sputtering
- Microelectronics: Sputtering is used to deposit conductive and insulating layers in semiconductor devices, such as integrated circuits and memory chips.
- Optoelectronics: Materials like indium tin oxide (ITO) are sputtered to create transparent conductive coatings for displays and touchscreens.
- Solar Cells: Sputtering is employed to deposit materials like cadmium telluride and copper indium gallium selenide (CIGS) for thin-film solar cells.
- Decorative Coatings: Metals like gold and titanium are sputtered onto surfaces to create durable and aesthetically pleasing finishes.
-
Materials Deposited by Sputtering
- Common materials include aluminum, copper, titanium, gold, silver, cadmium telluride, copper indium gallium selenide, and indium tin oxide. These materials are chosen for their specific properties, such as conductivity, transparency, or reflectivity, making them suitable for various industrial applications.
-
Advantages of Sputtering
- Uniform Coatings: Sputtering produces highly uniform thin films, even on complex geometries.
- Versatility: It can deposit a wide range of materials, including metals, alloys, and compounds.
- High-Quality Films: The process results in films with excellent adhesion, density, and purity.
- Scalability: Sputtering is suitable for both small-scale research and large-scale industrial production.
-
Challenges and Considerations
- Cost: Sputtering equipment can be expensive, and the process may require high vacuum conditions, increasing operational costs.
- Deposition Rate: Some sputtering methods, like HiPIMS, have lower deposition rates compared to other PVD techniques.
- Material Limitations: Certain materials may not be suitable for sputtering due to their physical or chemical properties.
In summary, sputtering is a highly effective and versatile PVD technique with numerous applications across various industries. Its ability to deposit high-quality, uniform thin films makes it indispensable in fields like microelectronics, optoelectronics, and renewable energy. However, the choice of sputtering method and materials must be carefully considered to optimize performance and cost-effectiveness.
Summary Table:
Material | Applications |
---|---|
Aluminum | Microelectronics, conductive coatings |
Gold | Decorative coatings, optoelectronics |
Indium Tin Oxide (ITO) | Transparent conductive coatings for displays and touchscreens |
Titanium | Durable and aesthetic finishes, solar cells |
Copper | Semiconductor devices, integrated circuits |
Interested in sputtering solutions for your industry? Contact our experts today to learn more!