The brazing temperature for aluminum is a critical factor that ensures the proper flow and bonding of the braze alloy. It is typically set at least 25ºC (50ºF) above the liquidus temperature of the braze alloy to ensure effective brazing. Aluminum can be brazed using various methods, including flame brazing, furnace brazing, inert gas brazing, vacuum brazing, and dissimilar metal brazing. Each method has its specific temperature requirements and conditions, but the key principle remains to maintain the temperature above the liquidus point of the alloy for successful brazing.
Key Points Explained:
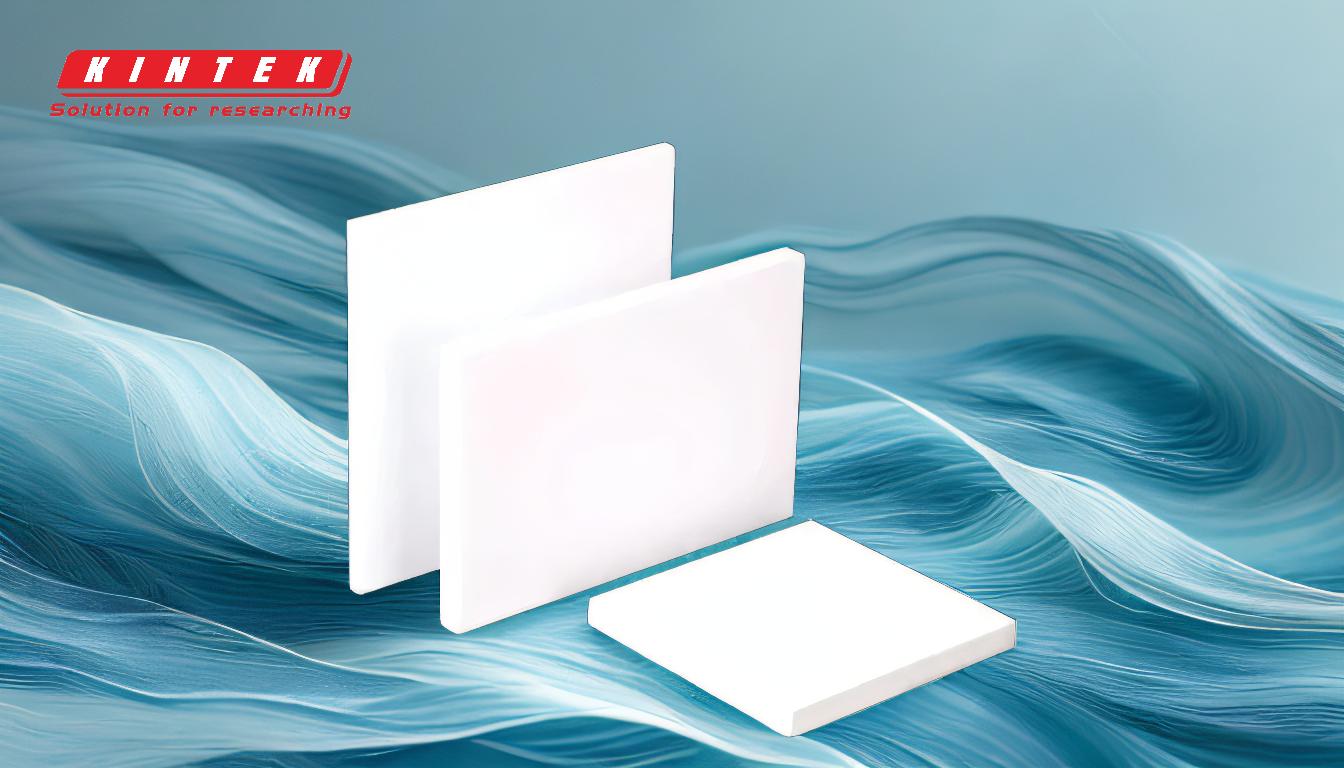
-
Recommended Brazing Temperature Range:
- The brazing temperature for aluminum should be set at least 25ºC (50ºF) above the liquidus temperature of the braze alloy. This ensures that the alloy is in a fully liquid state, which is essential for proper flow and bonding. Staying within the recommended range helps avoid overheating, which can lead to issues such as alloy evaporation or damage to the base metal.
-
Importance of Liquidus Temperature:
- The liquidus temperature is the point at which the braze alloy becomes completely liquid. Brazing above this temperature ensures that the alloy can flow into the joints and create strong bonds. If the temperature is too close to the liquidus point, the alloy may not flow properly, leading to weak joints.
-
Methods of Aluminum Brazing:
- Flame Brazing: This method uses a gas flame to heat the joint area. It is suitable for small-scale or manual operations.
- Furnace Brazing: This involves heating the entire assembly in a furnace, providing uniform heating and precise temperature control.
- Inert Gas Brazing: This method uses an inert gas atmosphere (e.g., nitrogen or argon) to prevent oxidation during the brazing process.
- Vacuum Brazing: This is performed in a vacuum environment to eliminate oxidation and contamination, making it ideal for high-purity applications.
- Dissimilar Metal Brazing: This involves joining aluminum to other metals, requiring careful temperature control to avoid damaging the different materials.
-
Temperature Control and Monitoring:
- Accurate temperature control is crucial in aluminum brazing. Overheating can cause the aluminum to melt or the braze alloy to evaporate, while insufficient heating can result in incomplete bonding. Using temperature monitoring tools such as thermocouples or infrared sensors ensures that the process stays within the optimal range.
-
Material Considerations:
- The choice of braze alloy and base metal composition can influence the brazing temperature. For example, some aluminum alloys have lower melting points, requiring adjustments to the brazing temperature to avoid damaging the base material.
-
Practical Tips for Successful Brazing:
- Always clean the aluminum surfaces thoroughly before brazing to remove oxides and contaminants.
- Use flux to prevent oxidation during the brazing process, especially in methods like flame brazing.
- Preheat the parts gradually to minimize thermal stress and ensure uniform heating.
By adhering to these principles and selecting the appropriate brazing method, you can achieve strong, reliable joints in aluminum brazing applications.
Summary Table:
Key Aspect | Details |
---|---|
Recommended Temperature | At least 25ºC (50ºF) above the braze alloy's liquidus temperature. |
Liquidus Temperature | Ensures the alloy is fully liquid for proper flow and bonding. |
Brazing Methods | Flame, furnace, inert gas, vacuum, and dissimilar metal brazing. |
Temperature Control | Use thermocouples or infrared sensors for accurate monitoring. |
Material Considerations | Adjust temperature based on braze alloy and base metal composition. |
Practical Tips | Clean surfaces, use flux, and preheat gradually for best results. |
Need expert advice on aluminum brazing? Contact us today for tailored solutions!