Calcination is a thermal treatment process that involves heating materials to high temperatures, typically below their melting point, in the absence or limited supply of air or oxygen. This process is used to induce thermal decomposition, remove volatile substances, or cause phase transitions in materials. It is commonly applied in the production of inorganic materials, such as converting calcium carbonate (CaCO₃) into calcium oxide (CaO) and carbon dioxide (CO₂), or extracting metals from ores. While calcination involves heating, it is distinct from burning, as it does not involve combustion but rather chemical dissociation or decomposition.
Key Points Explained:
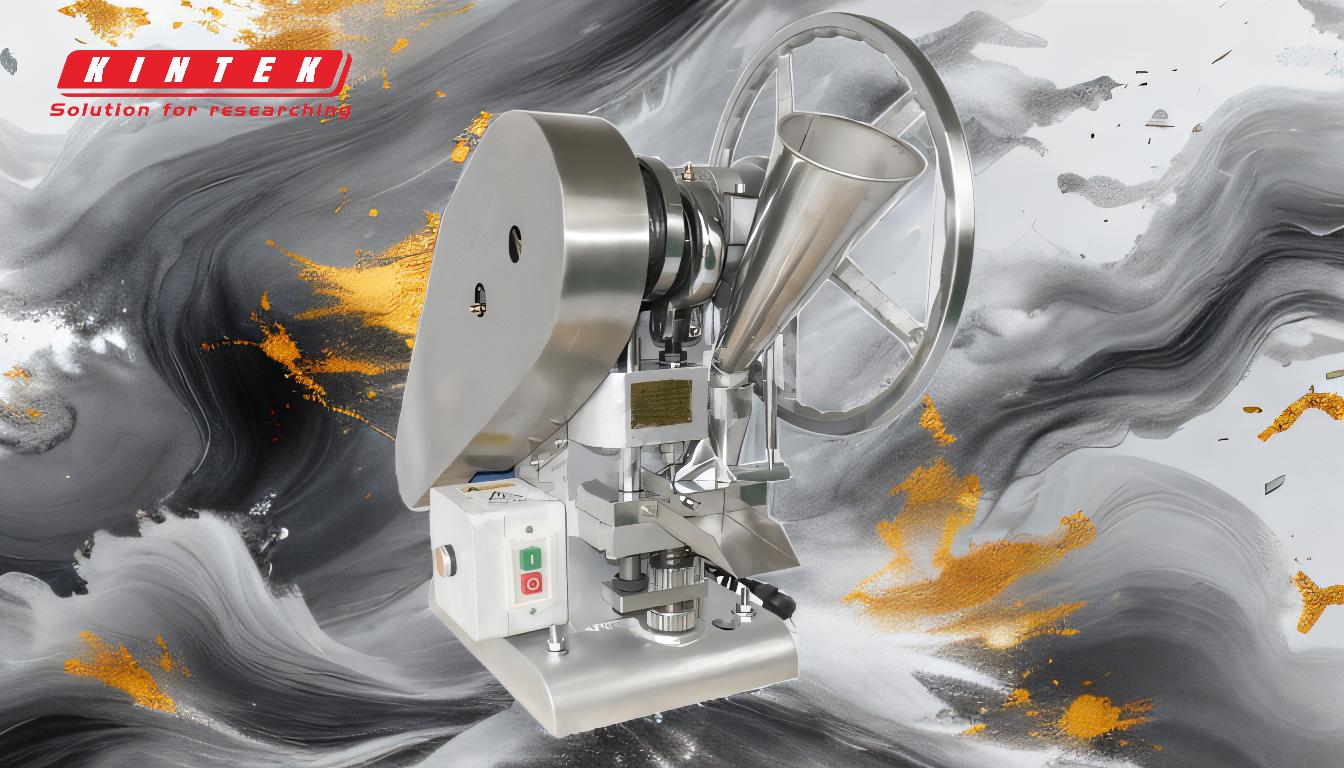
-
Definition of Calcination
- Calcination is a heat treatment process where materials are heated to high temperatures, typically below their melting point, in the absence or limited supply of air or oxygen.
- It is used to achieve thermal decomposition, remove volatile substances, or induce phase transitions in solid materials.
-
How Calcination Differs from Burning
- Burning involves combustion, a chemical reaction with oxygen that releases heat and light.
- Calcination does not involve combustion. Instead, it relies on thermal energy to break chemical bonds, leading to dissociation or decomposition of materials.
- For example, burning coal produces heat and carbon dioxide through combustion, while calcining limestone (CaCO₃) releases carbon dioxide (CO₂) without combustion, forming calcium oxide (CaO).
-
Purpose of Calcination
- Thermal Decomposition: Breaking down compounds into simpler substances. For example, heating calcium carbonate (CaCO₃) produces calcium oxide (CaO) and carbon dioxide (CO₂).
- Removal of Volatile Substances: Eliminating moisture, carbon dioxide, or other volatile components from materials. For instance, borax loses its bound water during calcination.
- Phase Transition: Changing the physical or chemical state of a material, such as converting ores into oxides.
-
Applications of Calcination
- Production of Lime: Heating limestone (CaCO₃) to produce lime (CaO), a key material in construction and chemical industries.
- Metal Extraction: Calcining metal ores to remove impurities and extract pure metals. For example, heating bauxite to produce alumina (Al₂O₃) for aluminum production.
- Ceramics and Refractories: Preparing raw materials for ceramic production by removing volatile components and improving material properties.
-
Conditions for Calcination
- Temperature: Materials are heated to high temperatures but below their melting point to avoid liquefaction.
- Atmosphere: Calcination typically occurs in the absence or limited supply of air or oxygen to prevent combustion.
- Duration: The process may take minutes to hours, depending on the material and desired outcome.
-
Examples of Calcination
- Limestone to Lime: CaCO₃ → CaO + CO₂. This is a classic example of thermal decomposition.
- Borax Dehydration: Heating borax to remove bound water molecules.
- Bauxite to Alumina: Heating bauxite to produce alumina for aluminum extraction.
-
Equipment Used in Calcination
- Rotary Kilns: Commonly used for large-scale calcination processes, such as lime production.
- Muffle Furnaces: Used for smaller-scale calcination in laboratories or specialized industries.
- Fluidized Bed Reactors: Employed for efficient heat transfer and uniform heating of materials.
-
Advantages of Calcination
- Purity: Removes impurities and volatile substances, yielding high-purity products.
- Controlled Process: Allows precise control over temperature and atmosphere to achieve desired outcomes.
- Versatility: Applicable to a wide range of materials, including ores, carbonates, and hydrates.
-
Challenges in Calcination
- Energy Consumption: Requires significant energy input due to high temperatures.
- Environmental Impact: Releases gases like CO₂, contributing to greenhouse gas emissions.
- Material Loss: Volatile substances are lost during the process, which may reduce the overall mass of the material.
-
Comparison with Other Thermal Processes
- Calcination vs. Roasting: Roasting involves heating ores in the presence of air or oxygen, often to oxidize sulfides. Calcination, on the other hand, typically occurs in the absence of air.
- Calcination vs. Sintering: Sintering involves heating materials to just below their melting point to fuse particles without decomposition. Calcination focuses on decomposition or phase transitions.
In summary, calcination is a critical thermal process used in various industries to achieve chemical dissociation, remove volatile substances, or induce phase transitions. It is distinct from burning, as it does not involve combustion but relies on controlled heating in specific atmospheric conditions. Understanding its principles and applications is essential for industries involved in material processing and metal extraction.
Summary Table:
Aspect | Details |
---|---|
Definition | Heating materials below melting point in limited air/oxygen. |
Purpose | Thermal decomposition, removal of volatiles, phase transitions. |
Applications | Lime production, metal extraction, ceramics, and refractories. |
Equipment | Rotary kilns, muffle furnaces, fluidized bed reactors. |
Advantages | High purity, controlled process, versatile material application. |
Challenges | High energy use, CO₂ emissions, material loss. |
Key Examples | Limestone to lime, borax dehydration, bauxite to alumina. |
Discover how calcination can transform your material processing—contact our experts today!