A calcination furnace is a specialized piece of equipment used in various industrial and laboratory processes to thermally treat materials. Its primary purpose is to drive off absorbed moisture, remove volatile constituents like carbon dioxide, and oxidize part or all of the substance being processed. This furnace is essential in applications such as material purification, decomposition, and transformation, making it a critical tool in industries like metallurgy, ceramics, and chemical processing. The furnace operates at high temperatures and is designed to ensure precise control over heating rates and temperature uniformity, enabling efficient and consistent results.
Key Points Explained:
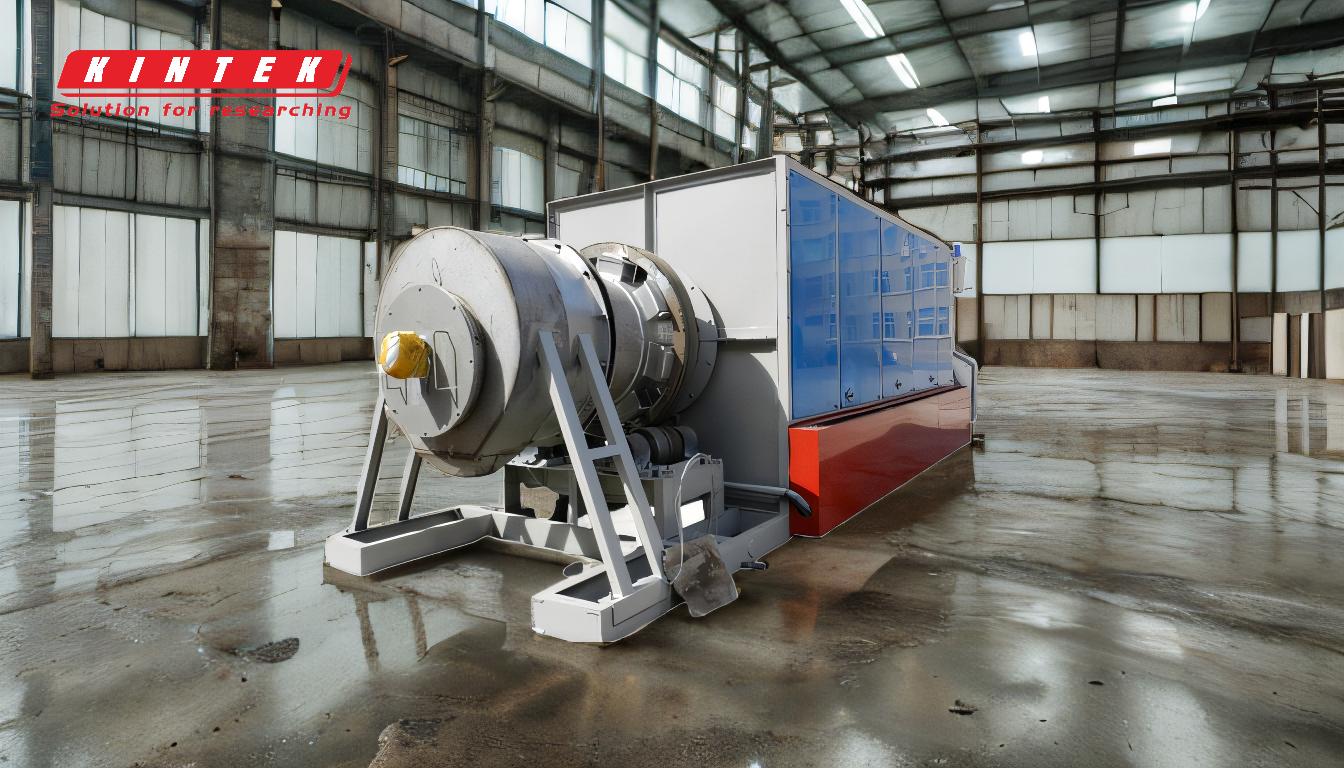
-
Purpose of a Calcination Furnace:
- The primary objective of a calcination furnace is to thermally treat materials to achieve specific chemical or physical changes. This includes:
- Driving off absorbed moisture: Removing water from the material to ensure dryness.
- Removing volatile constituents: Eliminating substances like carbon dioxide or sulfur dioxide that may be present in the material.
- Oxidizing the substance: Facilitating chemical reactions that alter the composition of the material, often to produce oxides.
- The primary objective of a calcination furnace is to thermally treat materials to achieve specific chemical or physical changes. This includes:
-
General Applications:
- Calcination furnaces are widely used in industries and laboratories for processes such as:
- Dehydration: Removing water from materials like gypsum or hydrated minerals.
- Decomposition: Breaking down carbonates or sulfates into oxides and gases.
- Oxidation: Transforming metals or other compounds into their oxide forms.
- These applications are critical in fields like metallurgy, ceramics, and chemical manufacturing.
- Calcination furnaces are widely used in industries and laboratories for processes such as:
-
Key Features:
- Calcination furnaces are designed with features that ensure efficient and precise operation:
- High-temperature capability: Capable of reaching temperatures necessary for calcination processes.
- Temperature uniformity: Heating elements on all sides of the chamber ensure even heat distribution.
- Programmable controls: Advanced systems like PID automatic control and programmable segments allow precise control over heating rates and temperatures.
- Energy efficiency: Insulation materials like high-purity alumina fiber and ceramic fiber chambers reduce heat loss and save energy.
- Safety features: Double-layer steel casings and fan cooling systems ensure operator safety by maintaining low external temperatures.
- Calcination furnaces are designed with features that ensure efficient and precise operation:
-
Comparison with Other Furnaces:
- While calcination furnaces share some similarities with other types of furnaces, they are specifically designed for calcination processes:
- Carbonization furnaces: Focus on converting organic materials into carbon, often with smokeless and energy-saving features.
- Sintering furnaces: Used for compacting and forming materials through heat and pressure, with precise temperature control.
- Burnout furnaces: Designed for high-temperature applications like wax burnout in investment casting, with fast heating and cooling capabilities.
- Laboratory furnaces: Compact and versatile, ideal for small-scale experiments and samples.
- While calcination furnaces share some similarities with other types of furnaces, they are specifically designed for calcination processes:
-
Design and Construction:
- The design of a calcination furnace typically includes:
- Heating chamber: Surrounded by heating elements and insulation to maintain high temperatures.
- Insulation materials: High-purity alumina fiber or ceramic fiber to minimize heat loss.
- Control systems: PID controllers and programmable segments for precise temperature regulation.
- Mobility and compactness: Some models feature frames with casters for easy movement and require minimal operating space.
- The design of a calcination furnace typically includes:
-
Operational Considerations:
- When using a calcination furnace, key operational factors include:
- Temperature range: Ensuring the furnace can reach the required temperatures for the specific process.
- Heating rate: Controlling the rate at which the material is heated to achieve the desired chemical or physical changes.
- Safety measures: Ensuring proper ventilation, cooling systems, and protective casings to prevent accidents.
- Maintenance: Regular inspection and maintenance of heating elements, insulation, and control systems to ensure consistent performance.
- When using a calcination furnace, key operational factors include:
In summary, a calcination furnace is a versatile and essential tool for processes that require high-temperature treatment of materials. Its design and features are tailored to meet the specific needs of calcination, ensuring efficiency, precision, and safety in various industrial and laboratory applications.
Summary Table:
Aspect | Details |
---|---|
Purpose | Thermally treat materials to remove moisture, volatiles, and oxidize substances. |
Applications | Dehydration, decomposition, oxidation in industries like metallurgy, ceramics. |
Key Features | High-temperature capability, uniform heating, programmable controls, safety. |
Design | Heating chamber, insulation, PID control systems, compact and mobile frames. |
Operational Factors | Temperature range, heating rate, safety measures, regular maintenance. |
Discover how a calcination furnace can optimize your processes—contact us today!