Chemical deposition is a process where a fluid precursor undergoes a chemical reaction on a solid surface, resulting in the formation of a solid layer. This technique is widely used to create thin films that are conformal, meaning they evenly coat all surfaces of the substrate. Chemical deposition methods are categorized based on the phase of the precursor, including plating, chemical solution deposition (CSD), chemical vapor deposition (CVD), and plasma-enhanced CVD (PECVD). These methods are crucial in industries like semiconductors, where high-purity and high-performance materials are required. The process is versatile, allowing for the deposition of coatings with precise control over thickness and composition.
Key Points Explained:
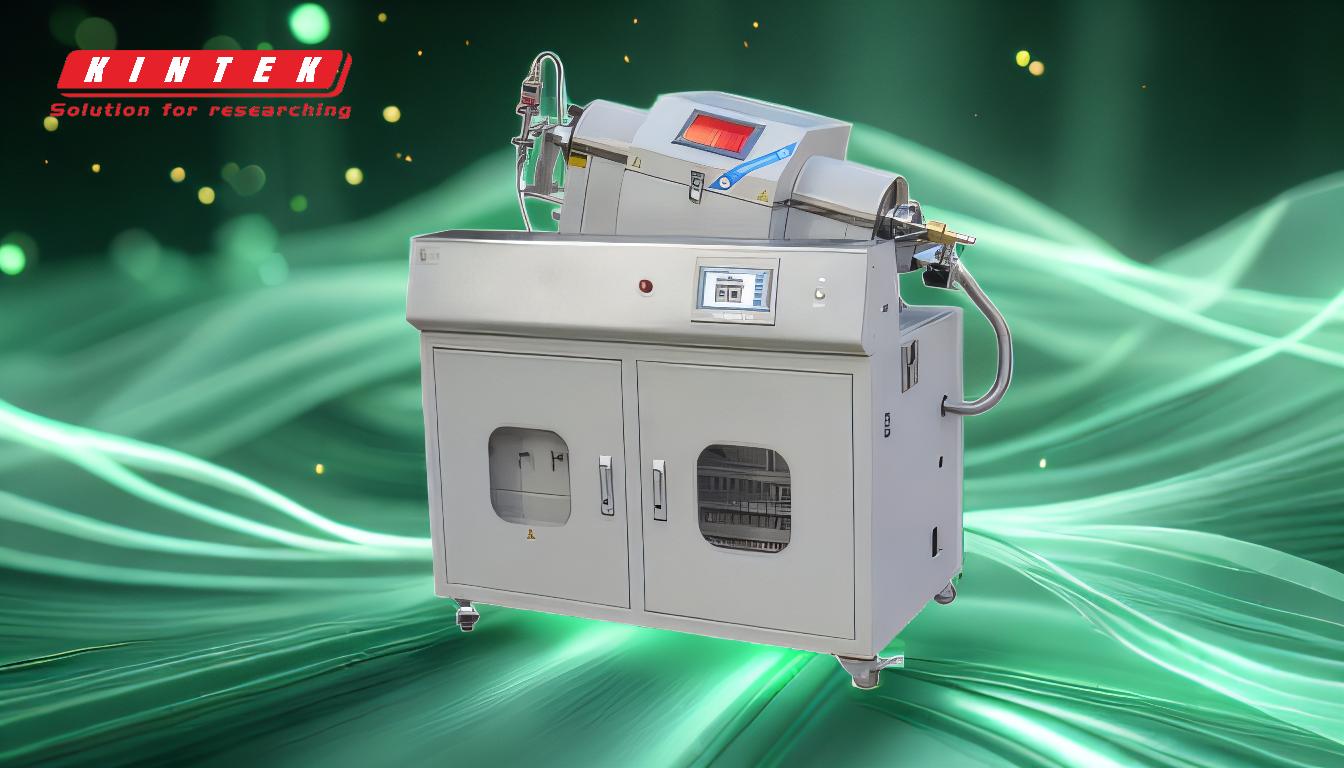
-
Definition of Chemical Deposition:
- Chemical deposition involves a fluid precursor that undergoes a chemical change at a solid surface, leaving behind a solid layer. This process is used to create thin films that are conformal, meaning they evenly coat all surfaces of the substrate, rather than being directional.
-
Types of Chemical Deposition:
- Plating: This involves the deposition of a metal layer onto a substrate through an electrochemical process. It is commonly used for decorative purposes, corrosion resistance, and improving surface properties.
- Chemical Solution Deposition (CSD): This method involves submerging the substrate in a chemical solution, which then deposits a coating on the surface. CSD is often used for creating thin films in electronics and optics.
- Chemical Vapor Deposition (CVD): CVD is a process where a volatile fluid precursor undergoes a chemical reaction on the substrate surface, resulting in the deposition of a solid material. CVD is widely used in the semiconductor industry to produce high-purity, high-performance materials.
- Plasma-Enhanced CVD (PECVD): This is a variation of CVD where plasma is used to enhance the chemical reaction at lower temperatures. PECVD is particularly useful for depositing thin films on temperature-sensitive substrates.
-
Applications of Chemical Deposition:
- Semiconductor Industry: CVD and PECVD are essential for producing high-purity materials used in semiconductor devices. These methods allow for the precise control of film thickness and composition, which is critical for the performance of electronic components.
- Optics and Coatings: Chemical deposition techniques are used to create anti-reflective coatings, protective layers, and other functional coatings on optical components.
- Corrosion Resistance: Plating and other chemical deposition methods are used to apply protective coatings that prevent corrosion on metal surfaces.
-
Advantages of Chemical Deposition:
- Conformal Coating: Chemical deposition techniques produce thin films that evenly coat all surfaces of the substrate, including complex geometries and fine features.
- High Purity: Methods like CVD and PECVD can produce materials with very high purity, which is essential for applications in the semiconductor industry.
- Versatility: Chemical deposition can be used to deposit a wide range of materials, including metals, ceramics, and polymers, making it a versatile technique for various industries.
-
Challenges and Considerations:
- Process Control: Achieving the desired film properties requires precise control over the deposition parameters, such as temperature, pressure, and precursor concentration.
- Cost: Some chemical deposition methods, particularly CVD and PECVD, can be expensive due to the need for specialized equipment and high-purity precursors.
- Substrate Compatibility: The choice of deposition method must consider the compatibility of the substrate material with the deposition process, especially in terms of temperature sensitivity.
In summary, chemical deposition is a versatile and essential technique for creating thin films and coatings with precise control over their properties. Its applications span across various industries, from semiconductors to optics, and it offers significant advantages in terms of conformal coating and material purity. However, it also presents challenges related to process control, cost, and substrate compatibility that must be carefully managed.
Summary Table:
Aspect | Details |
---|---|
Definition | Fluid precursor undergoes a chemical reaction on a solid surface, forming a solid layer. |
Types | Plating, CSD, CVD, PECVD |
Applications | Semiconductors, optics, corrosion resistance |
Advantages | Conformal coating, high purity, versatility |
Challenges | Process control, cost, substrate compatibility |
Discover how chemical deposition can enhance your industry applications—contact our experts today!