Chemical vapor deposition (CVD) is a widely used technique for depositing thin films of inorganic materials onto substrates. The process involves introducing gaseous precursors into a chamber, where they react or decompose to form a solid material that deposits onto a substrate. CVD is versatile and can be used to create high-quality, durable coatings for various applications, including electronics, optics, and solar energy. The choice of substrate material is critical, as it directly influences the quality and properties of the deposited film. Common substrate materials include silicon, glass, and metals, which are chosen based on their compatibility with the deposition process and the intended application.
Key Points Explained:
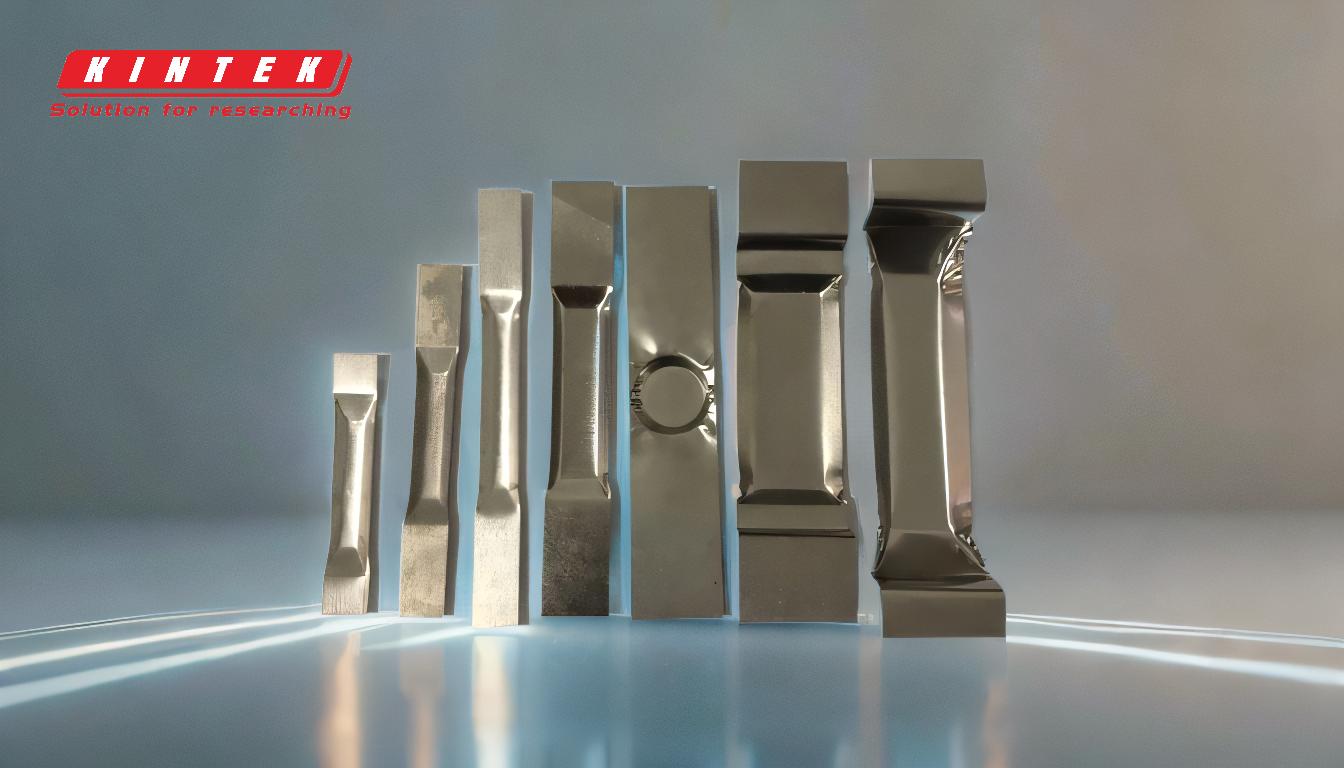
-
Definition of Chemical Vapor Deposition (CVD):
- CVD is a process used to deposit thin films of inorganic materials onto a substrate. It involves the introduction of gaseous precursors into a chamber, where they react or decompose to form a solid material that adheres to the substrate. This method is known for producing high-quality, durable coatings.
-
Types of CVD Processes:
- Aerosol-Assisted CVD: This method uses an aerosol as the precursor, which is then deposited onto the substrate. It is useful for materials that are difficult to vaporize.
- Direct Liquid Injection CVD: In this process, a liquid precursor is injected into a heated chamber, where it vaporizes and deposits onto the substrate. This method is suitable for materials that are liquid at room temperature.
- Plasma-Based CVD: Instead of using heat, this method employs plasma to activate the precursors, leading to deposition on the substrate. Plasma-based CVD is particularly useful for depositing materials at lower temperatures.
-
Common Materials Deposited via CVD:
- Polysilicon: Widely used in the solar photovoltaic (PV) supply chain, polysilicon is a key material in the production of solar cells.
- Silicon Dioxide: Often found in nature as quartz, silicon dioxide is typically deposited using low-pressure chemical vapor deposition (LPCVD). It is used in various applications, including as an insulating layer in electronic devices.
-
Importance of Substrate Material:
- The substrate material plays a crucial role in the CVD process. It must be compatible with the deposition conditions and the intended application. Common substrate materials include:
- Silicon: Widely used in the semiconductor industry due to its excellent electrical properties.
- Glass: Often used in optical applications due to its transparency and smooth surface.
- Metals: Used in various applications where mechanical strength and conductivity are required.
- The substrate material plays a crucial role in the CVD process. It must be compatible with the deposition conditions and the intended application. Common substrate materials include:
-
Applications of CVD:
- Electronics: CVD is used to deposit thin films in the fabrication of semiconductors, integrated circuits, and other electronic components.
- Optics: CVD is employed to create anti-reflective coatings, mirrors, and other optical components.
- Solar Energy: CVD is crucial in the production of solar cells, where it is used to deposit materials like polysilicon.
-
Advantages of CVD:
- High-Quality Films: CVD produces films with excellent uniformity, purity, and adhesion.
- Versatility: CVD can deposit a wide range of materials, including metals, ceramics, and semiconductors.
- Scalability: CVD processes can be scaled up for industrial production, making it suitable for large-scale manufacturing.
-
Challenges and Considerations:
- Cost: CVD equipment and precursors can be expensive, making the process costly for some applications.
- Complexity: The process requires precise control of temperature, pressure, and gas flow rates, which can be challenging.
- Substrate Compatibility: The substrate must be able to withstand the deposition conditions without degrading or reacting with the precursors.
In summary, chemical vapor deposition is a versatile and powerful technique for depositing thin films of inorganic materials onto substrates. The choice of substrate material is critical, as it directly affects the quality and properties of the deposited film. Common substrate materials include silicon, glass, and metals, which are chosen based on their compatibility with the deposition process and the intended application. CVD is widely used in electronics, optics, and solar energy, offering high-quality, durable coatings for a variety of applications.
Summary Table:
Aspect | Details |
---|---|
Common Substrates | Silicon, Glass, Metals |
Key Properties | Compatibility, thermal stability, surface smoothness |
Applications | Electronics, Optics, Solar Energy |
Material Examples | Polysilicon, Silicon Dioxide |
Process Types | Aerosol-Assisted CVD, Direct Liquid Injection CVD, Plasma-Based CVD |
Advantages | High-quality films, versatility, scalability |
Challenges | Cost, complexity, substrate compatibility |
Discover how the right substrate material can enhance your CVD process—contact our experts today!