Thin film coatings are specialized layers applied to surfaces to enhance their properties or add new functionalities. These coatings are typically thin, ranging from nanometers to micrometers in thickness, and are used across various industries for purposes such as protection, decoration, and performance enhancement. They can improve surface hardness, corrosion resistance, electrical conductivity, optical properties, and more. Thin film coatings are versatile and can be tailored to meet specific needs, making them essential in applications ranging from industrial tools to advanced electronics and decorative finishes.
Key Points Explained:
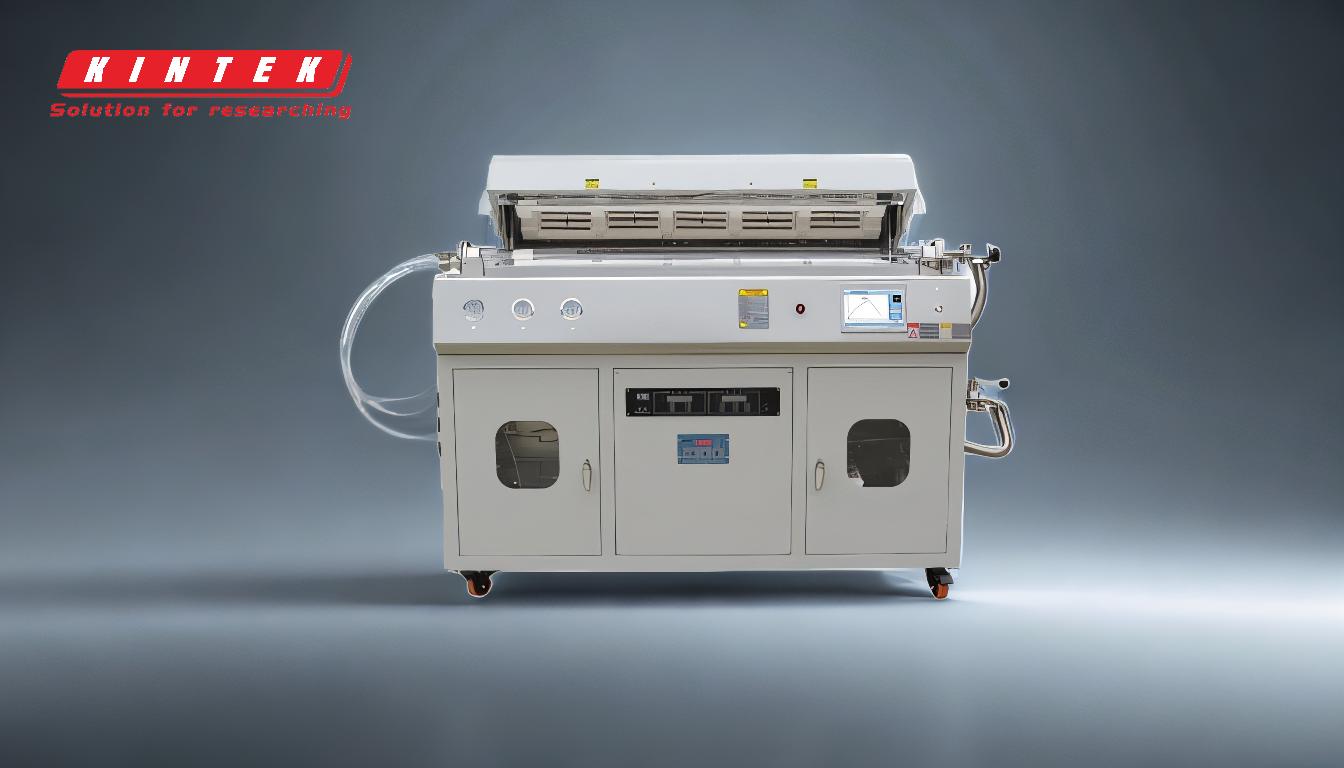
-
Definition and Purpose of Thin Film Coatings:
- Thin film coatings are ultra-thin layers applied to surfaces to modify their properties or add new functionalities.
- They serve multiple purposes, including protection (e.g., from wear, scratches, corrosion), decoration (e.g., altering color or glossiness), and performance enhancement (e.g., improving conductivity or hardness).
-
Characteristics of Thin Film Coatings:
- Transparency: Some coatings are designed to be transparent, making them suitable for optical applications like lenses or displays.
- Durability: Coatings can enhance the durability of surfaces, making them resistant to wear, scratches, and environmental factors.
- Electrical and Optical Properties: Thin films can increase or decrease electrical conductivity or modify the transmission of signals and light, making them useful in electronics and photonics.
- Corrosion Resistance: Many coatings are applied to protect surfaces from corrosion, extending the lifespan of materials.
-
Types of Thin Film Coatings:
-
Functional Coatings: These are designed to improve specific properties like hardness, wear resistance, or thermal resistance. Examples include:
- Ti-Al-N: Increases hardness and reduces friction, commonly used in cutting tools.
- Al-Cr-N: Enhances tool life and thermal resistance, ideal for high-temperature applications.
- Cr-N and Ti-C-N: Improve corrosion resistance and cutting performance.
- Decorative Coatings: These are applied for aesthetic purposes, such as metallic coatings on plastic substrates to create a shiny or textured appearance.
-
Functional Coatings: These are designed to improve specific properties like hardness, wear resistance, or thermal resistance. Examples include:
-
Applications of Thin Film Coatings:
- Industrial Tools: Coatings like Ti-Al-N and Al-Cr-N are used to enhance the performance and lifespan of cutting tools and machinery.
- Electronics: Thin films are used in devices to convert light energy into electrical power (e.g., solar panels) and in advanced memory storage technologies.
- Optics: Transparent coatings are applied to lenses, mirrors, and displays to improve optical performance and durability.
- Decorative Finishes: Thin films are used to create reflective surfaces, alter surface textures, and add color to products.
-
Benefits of Thin Film Coatings:
- Enhanced Performance: Coatings can significantly improve the performance of substrate materials by adding properties like hardness, conductivity, or resistance to environmental factors.
- Versatility: Thin film coatings can be tailored to meet specific requirements, making them suitable for a wide range of applications.
- Surface Protection: They protect surfaces from wear, scratches, fingerprints, and corrosion, extending the lifespan of materials.
- Aesthetic Appeal: Decorative coatings can enhance the visual appeal of products, making them more attractive to consumers.
-
Coating Properties and Substrate Interaction:
- Thin film coatings are extremely adherent, meaning they bond strongly to the substrate, ensuring long-lasting performance.
- The interaction between the coating and the substrate is critical, as it determines the effectiveness of the coating in achieving desired properties like hardness, conductivity, or optical transmission.
-
Examples of Prominent Coatings:
- Ti-Al-N: Known for its high hardness and low friction, it is widely used in cutting tools and industrial applications.
- Al-Cr-N: Offers excellent thermal resistance and tool life, making it suitable for high-temperature environments.
- Cr-N and Ti-C-N: These coatings are valued for their corrosion resistance and cutting performance, often used in harsh environments.
In summary, thin film coatings are a critical technology that enhances the functionality, durability, and appearance of materials across various industries. Their ability to be customized for specific applications makes them indispensable in modern manufacturing and technology.
Summary Table:
Key Aspect | Details |
---|---|
Purpose | Modify surface properties, add functionality, protect, decorate, enhance. |
Thickness | Nanometers to micrometers. |
Key Characteristics | Transparency, durability, electrical/optical properties, corrosion resistance. |
Types | Functional (e.g., Ti-Al-N, Al-Cr-N) and decorative coatings. |
Applications | Industrial tools, electronics, optics, decorative finishes. |
Benefits | Enhanced performance, versatility, surface protection, aesthetic appeal. |
Learn how thin film coatings can transform your products—contact our experts today!