Cold isostatic pressing (CIP) is a manufacturing process used to compact powdered materials into a desired shape using uniform pressure applied from all directions. The mold material used in CIP is crucial as it must withstand high pressures while maintaining the shape of the powder being compacted. Unlike axial pressing, which typically uses steel molds, CIP molds are made from elastomers, silicone, and polyurethanes. These materials are chosen for their flexibility, durability, and ability to transmit pressure uniformly. The selection of mold material is critical to achieving high-quality, dense, and uniform compacts.
Key Points Explained:
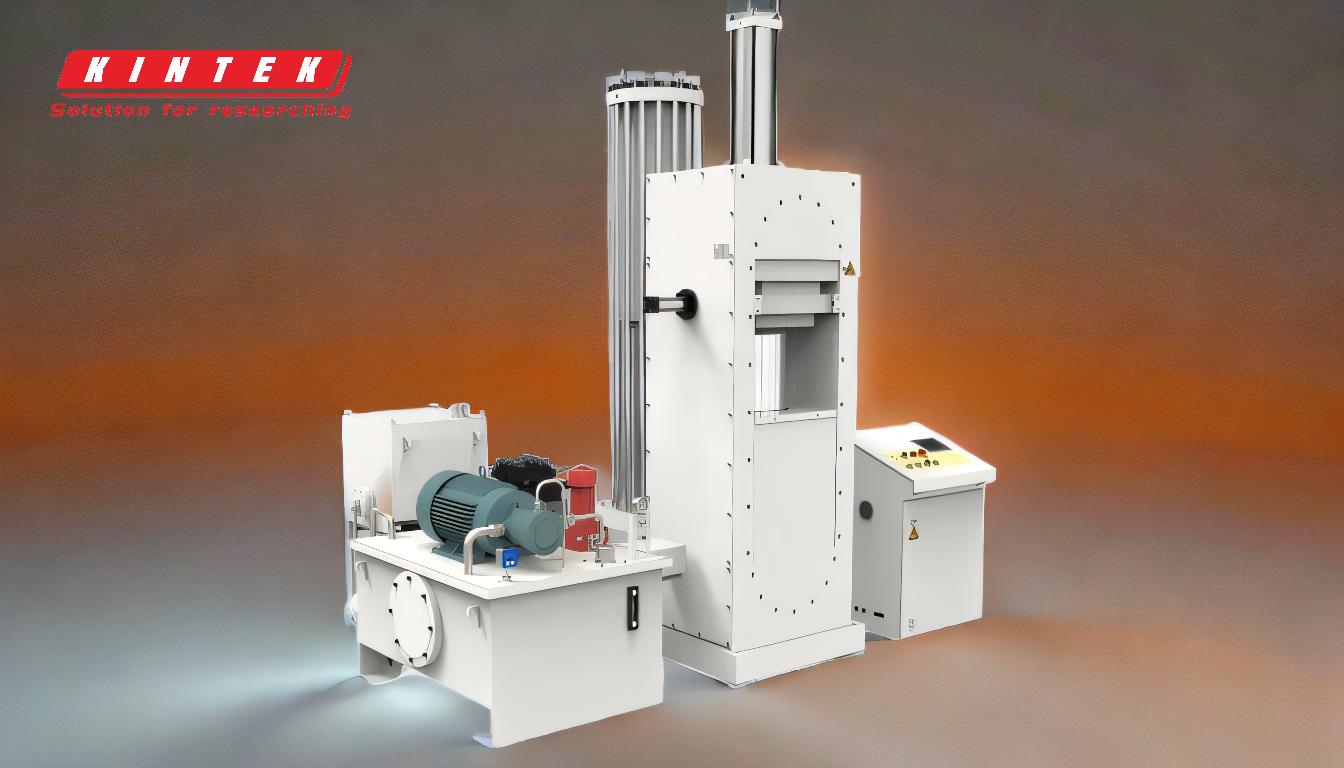
-
Cold Isostatic Pressing (CIP) Overview:
- CIP is a process that applies uniform pressure from all directions to compact powdered materials into a specific shape.
- It is commonly used for materials that are difficult to shape using traditional methods, such as ceramics, metals, and composites.
- The process is performed at room temperature, distinguishing it from warm or hot isostatic pressing.
-
Role of Mold Materials in CIP:
- The mold in CIP must be flexible yet durable to withstand high pressures and maintain the shape of the powder.
- Unlike axial pressing, which uses rigid steel molds, CIP molds are made from elastomeric materials like silicone and polyurethanes.
- These materials allow the mold to deform under pressure and transmit that pressure uniformly to the powder.
-
Common Mold Materials:
- Elastomers: Known for their flexibility and resilience, elastomers are ideal for CIP molds as they can withstand repeated pressure cycles without degrading.
- Silicone: Silicone is a popular choice due to its excellent thermal stability, chemical resistance, and ability to maintain shape under high pressure.
- Polyurethanes: These materials offer a balance of flexibility and durability, making them suitable for CIP molds that require high precision and longevity.
-
Advantages of Elastomeric Mold Materials:
- Uniform Pressure Distribution: Elastomers ensure that pressure is applied evenly across the powder, resulting in compacts with consistent density and minimal defects.
- Ease of Demolding: The flexibility of elastomeric molds allows for easy removal of the compacted part without damaging it.
- Cost-Effectiveness: Compared to steel molds, elastomeric molds are often more affordable and easier to manufacture.
-
Considerations for Mold Material Selection:
- Pressure Requirements: The mold material must be able to withstand the specific pressure levels used in the CIP process.
- Powder Characteristics: The type of powder being compacted may influence the choice of mold material, especially if the powder is abrasive or chemically reactive.
- Durability: The mold material should be resistant to wear and tear, especially for high-volume production.
-
Comparison with Warm and Hot Isostatic Pressing:
- Unlike CIP, warm and hot isostatic pressing involve elevated temperatures, which can affect the choice of mold material.
- In warm or hot isostatic pressing, the mold material must also withstand high temperatures without degrading, which may limit the use of certain elastomers.
-
Applications of CIP Mold Materials:
- CIP is widely used in industries such as aerospace, automotive, and medical devices for producing complex-shaped components.
- The choice of mold material is critical in these applications to ensure the final product meets stringent quality and performance standards.
In summary, the mold material used in cold isostatic pressing machine plays a vital role in determining the quality and consistency of the final product. Elastomers, silicone, and polyurethanes are the preferred materials due to their flexibility, durability, and ability to transmit pressure uniformly. Understanding the properties and advantages of these materials is essential for optimizing the CIP process and achieving high-quality compacts.
Summary Table:
Aspect | Details |
---|---|
Process Overview | Uniform pressure from all directions to compact powdered materials. |
Common Mold Materials | Elastomers, silicone, and polyurethanes. |
Key Advantages | Flexibility, durability, uniform pressure distribution, and cost-effectiveness. |
Applications | Aerospace, automotive, and medical device manufacturing. |
Key Considerations | Pressure requirements, powder characteristics, and durability. |
Interested in optimizing your cold isostatic pressing process? Contact our experts today for tailored solutions!