Cold isostatic pressing (CIP) is a manufacturing process that involves applying uniform hydrostatic pressure to a powder material enclosed in a flexible mold, typically made of rubber or plastic. This pressure is transmitted through the mold to compact the powder into a desired shape. CIP is widely used in various industries, including the production of refractory materials, cemented carbides, ceramic insulators, and even food processing. The process is particularly beneficial for creating large or complex shapes that are difficult to achieve with traditional uniaxial pressing methods. The uniform pressure ensures consistent density and strength throughout the compacted material, making it ideal for applications requiring high precision and durability.
Key Points Explained:
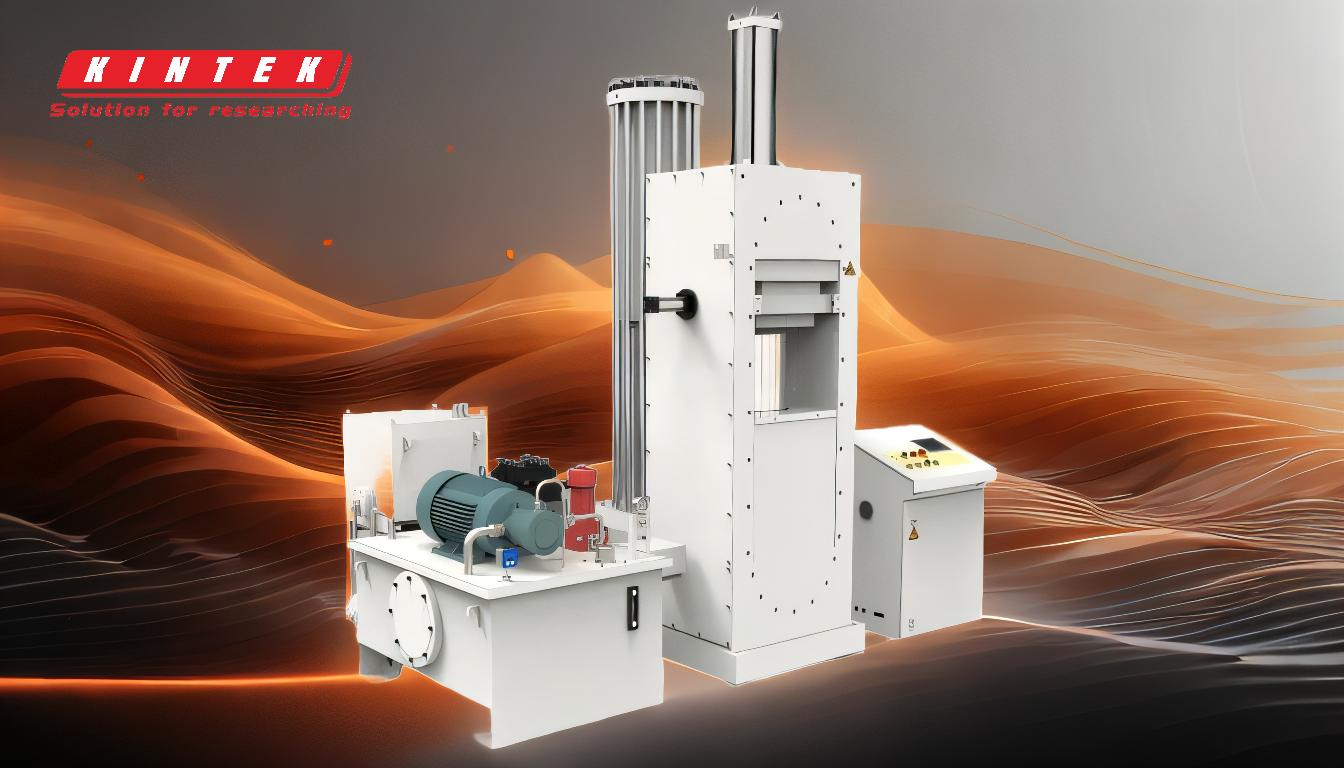
-
Definition of Cold Isostatic Pressing (CIP):
- Cold isostatic pressing is a powder-forming technique where a uniform hydrostatic pressure is applied to a powder material enclosed in a flexible mold. The pressure is transmitted through the mold to compact the powder into a solid shape. This process is called "cold" because it is typically performed at room temperature or slightly above, without the use of heat.
-
How CIP Works:
- In the CIP process, the powder material is placed inside a flexible mold, which is then inserted into a high-pressure chamber. A liquid medium, often an oil-water mixture, is pumped into the chamber and pressurized uniformly from all directions. This creates a hydrostatic pressure that compacts the powder into a dense, uniform shape. The pressure in the chamber can reach up to 100,000 psi, ensuring thorough compaction.
-
Applications of CIP:
- CIP is used in a wide range of industries to produce various components, including:
- Refractory materials: Such as nozzles, blocks, and crucibles.
- Cemented carbides: Used in wear-resistant tools and metal-forming applications.
- Isotropic graphite: For applications requiring uniform properties in all directions.
- Ceramic insulators: Used in electrical and electronic applications.
- Food processing: For compacting food products without significant temperature rise.
- Artificial bones and medical implants: Where uniform density and strength are critical.
- Plastic tubes and rods: For industrial and consumer applications.
- CIP is used in a wide range of industries to produce various components, including:
-
Advantages of CIP:
- Uniform Density: The hydrostatic pressure ensures that the powder is compacted uniformly, resulting in consistent density and strength throughout the product.
- Complex Shapes: CIP is ideal for producing large or complex shapes that are difficult to achieve with traditional pressing methods.
- Versatility: The process can be used with a wide range of materials, including metals, ceramics, and plastics.
- Minimal Temperature Rise: The process is performed at or near room temperature, making it suitable for materials that are sensitive to heat.
-
Comparison with Other Pressing Methods:
- Unlike uniaxial pressing, where pressure is applied from one or two directions, CIP applies pressure uniformly from all directions. This results in a more uniform density and eliminates the risk of density gradients that can occur in uniaxial pressing. CIP is particularly useful for parts that are too large or complex for uniaxial presses.
-
Materials Suitable for CIP:
- CIP is suitable for a wide range of materials, including:
- Refractory materials: Such as alumina, zirconia, and silicon carbide.
- Metals: Including high-melting-point metals like tungsten and molybdenum.
- Ceramics: Used in insulators, filters, and other industrial applications.
- Plastics and resins: For forming tubes, rods, and other components.
- Food products: For compacting powders into solid forms.
- CIP is suitable for a wide range of materials, including:
-
Limitations of CIP:
- Precision: While CIP is excellent for producing large or complex shapes, it may not achieve the same level of precision as other methods like hot isostatic pressing (HIP) or machining.
- Cost: The equipment and molds required for CIP can be expensive, making it less suitable for small-scale production.
- Material Limitations: Some materials may not compact well under cold isostatic pressure and may require additional processing steps.
-
Future Trends in CIP:
- Advanced Materials: As new materials are developed, CIP is likely to play a key role in their processing, particularly for materials that require uniform density and strength.
- Automation: Advances in automation and control systems are expected to improve the efficiency and precision of the CIP process.
- Sustainability: There is growing interest in using CIP for sustainable materials, such as recycled metals and biodegradable plastics.
In summary, cold isostatic pressing is a versatile and effective method for compacting powders into uniform, dense shapes. Its ability to produce complex shapes and work with a wide range of materials makes it a valuable tool in various industries. For more detailed information on the equipment used in this process, you can refer to the isostatic press topic.
Summary Table:
Key Aspect | Details |
---|---|
Definition | Powder-forming technique using uniform hydrostatic pressure at room temperature. |
Process | Powder in a flexible mold is pressurized uniformly using a liquid medium. |
Applications | Refractory materials, cemented carbides, ceramic insulators, food processing, medical implants. |
Advantages | Uniform density, complex shapes, versatility, minimal temperature rise. |
Materials Suitable | Metals, ceramics, plastics, food products, refractory materials. |
Limitations | Lower precision, higher cost, material-specific limitations. |
Future Trends | Advanced materials, automation, sustainability. |
Learn how cold isostatic pressing can transform your manufacturing process—contact our experts today!