CVD (Chemical Vapor Deposition) and PVD (Physical Vapor Deposition) are two prominent thin-film deposition techniques used in MEMS (Micro-Electro-Mechanical Systems) fabrication. These methods are essential for creating thin films of materials on substrates, which are critical for the functionality of MEMS devices. CVD involves chemical reactions to produce a thin film on a substrate, while PVD relies on physical processes like sputtering or evaporation to deposit materials. Both techniques have unique advantages and are chosen based on the specific requirements of the MEMS application, such as film quality, uniformity, and material compatibility.
Key Points Explained:
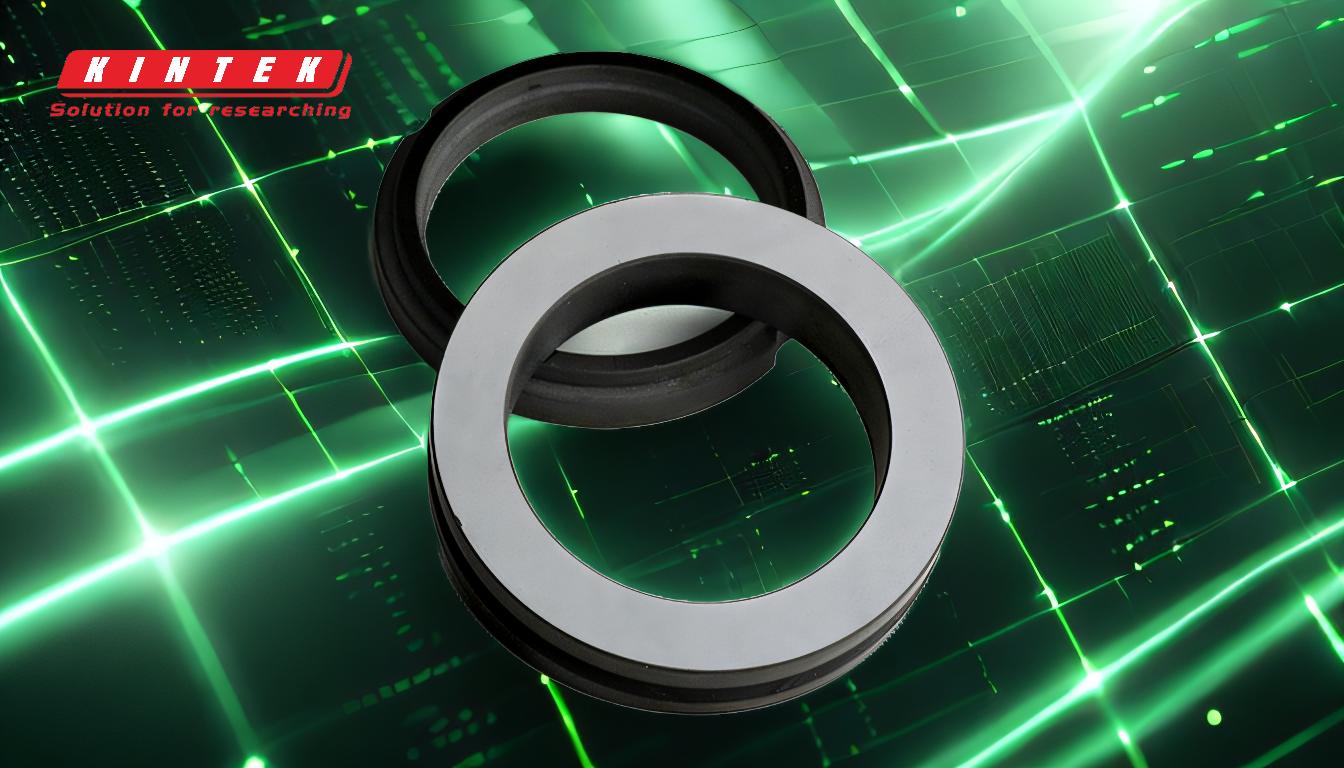
-
What is CVD?
- Definition: CVD is a process where a substrate is exposed to volatile precursors, which react or decompose on the substrate surface to produce a thin film.
- Process: The process typically involves heating the substrate to high temperatures in a vacuum chamber, where gaseous reactants are introduced. These reactants undergo chemical reactions to form a solid film on the substrate.
- Applications in MEMS: CVD is widely used for depositing materials like silicon dioxide, silicon nitride, and polysilicon, which are essential for MEMS structures. It is particularly valued for its ability to produce high-quality, uniform films with excellent step coverage.
-
What is PVD?
- Definition: PVD is a process where material is physically removed from a target source and deposited onto a substrate.
- Process: Common PVD techniques include sputtering and evaporation. In sputtering, ions bombard a target material, causing atoms to be ejected and deposited onto the substrate. In evaporation, the target material is heated until it vaporizes, and the vapor condenses on the substrate.
- Applications in MEMS: PVD is used for depositing metals and alloys, such as aluminum, gold, and titanium, which are crucial for electrical interconnects and contacts in MEMS devices. PVD is favored for its ability to deposit a wide range of materials with good adhesion and purity.
-
Comparison of CVD and PVD in MEMS:
- Film Quality: CVD generally produces films with better uniformity and step coverage, making it suitable for complex MEMS structures. PVD, on the other hand, is better for depositing metals and alloys with high purity and adhesion.
- Temperature Requirements: CVD often requires higher temperatures, which can limit its use with temperature-sensitive substrates. PVD can be performed at lower temperatures, making it more versatile for various substrate materials.
- Deposition Rate: PVD typically has a higher deposition rate compared to CVD, which can be advantageous for high-throughput manufacturing.
- Material Compatibility: CVD is more suitable for depositing compound materials like oxides and nitrides, while PVD is preferred for elemental metals and alloys.
-
Advantages and Disadvantages:
- CVD Advantages: Excellent film uniformity, high-quality films, good step coverage, and ability to deposit a wide range of materials.
- CVD Disadvantages: High temperature requirements, potential for hazardous by-products, and slower deposition rates.
- PVD Advantages: Lower temperature processing, high deposition rates, good adhesion, and ability to deposit a wide range of metals and alloys.
- PVD Disadvantages: Limited step coverage, potential for film stress, and less suitable for depositing compound materials.
-
Choosing Between CVD and PVD:
- The choice between CVD and PVD depends on the specific requirements of the MEMS application. Factors to consider include the type of material to be deposited, the desired film properties, substrate compatibility, and process constraints such as temperature and deposition rate.
In summary, both CVD and PVD are indispensable techniques in MEMS fabrication, each with its own set of advantages and limitations. Understanding the specific requirements of the MEMS application is crucial for selecting the appropriate deposition method.
Summary Table:
Aspect | CVD | PVD |
---|---|---|
Definition | Chemical reactions produce thin films on a substrate. | Physical processes (e.g., sputtering, evaporation) deposit materials. |
Process | High-temperature chemical reactions in a vacuum chamber. | Sputtering or evaporation of target material onto a substrate. |
Applications | Silicon dioxide, silicon nitride, polysilicon for MEMS structures. | Metals/alloys (e.g., aluminum, gold, titanium) for electrical interconnects. |
Film Quality | High uniformity, excellent step coverage. | High purity, good adhesion. |
Temperature | Higher temperatures required. | Lower temperatures suitable for sensitive substrates. |
Deposition Rate | Slower deposition rate. | Faster deposition rate. |
Material Compatibility | Ideal for compound materials (e.g., oxides, nitrides). | Preferred for elemental metals and alloys. |
Need help choosing the right thin-film deposition technique for your MEMS application? Contact our experts today!