Chemical Vapor Deposition (CVD) coating of solids in a fluidized bed is a specialized process used to deposit thin, uniform coatings on particulate materials. This technique combines the principles of fluidization—where solid particles are suspended in a gas stream to behave like a fluid—with CVD, a method that uses chemical reactions to deposit materials onto a substrate. The fluidized bed ensures that all particles are evenly exposed to the reactive gas mixture, resulting in a consistent and high-quality coating. This process is particularly useful for applications requiring precise control over coating thickness, uniformity, and material properties, such as in the production of catalysts, advanced ceramics, and protective coatings.
Key Points Explained:
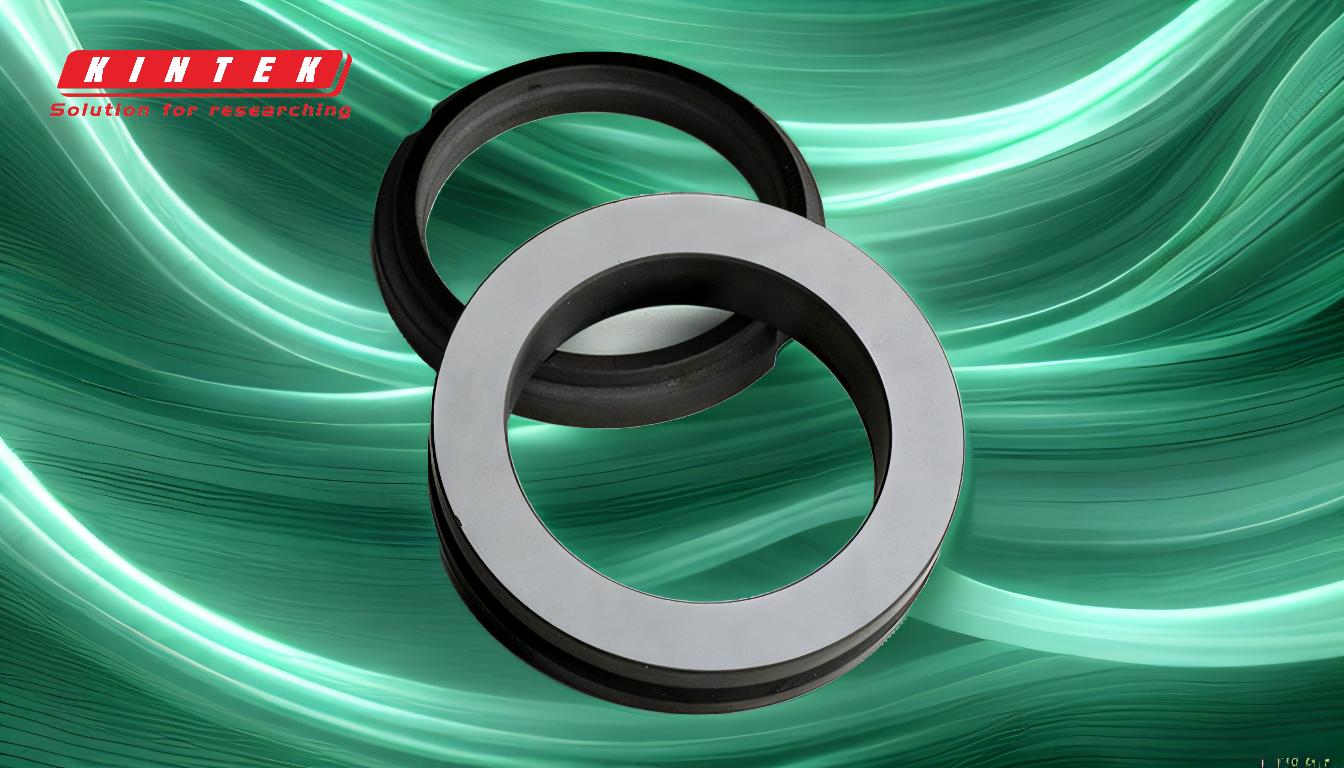
-
Principle of Fluidized Bed CVD:
- In a fluidized bed, solid particles are suspended in an upward-flowing gas stream, creating a dynamic, fluid-like state. This allows for excellent heat and mass transfer, ensuring uniform exposure of particles to the reactive gases used in CVD.
- The fluidized bed setup is ideal for coating small particles because it prevents agglomeration and ensures that each particle is individually coated.
-
Chemical Vapor Deposition (CVD) Process:
- CVD involves the decomposition or reaction of gaseous precursors on the surface of the solid particles to form a solid coating. The process typically occurs at elevated temperatures.
- Common precursors include metal halides, hydrides, or organometallic compounds, which react to form materials like silicon carbide, silicon nitride, or metallic coatings.
-
Advantages of Fluidized Bed CVD:
- Uniform Coating: The fluidized bed ensures that all particles are evenly coated, which is difficult to achieve with other methods.
- Scalability: This method is scalable and can be used for both small-scale laboratory applications and large-scale industrial production.
- Versatility: It can be used to coat a wide range of materials, including metals, ceramics, and polymers.
-
Applications of Fluidized Bed CVD:
- Catalysts: Coating catalyst particles with thin layers of active materials can enhance their performance and longevity.
- Protective Coatings: Used to apply corrosion-resistant or wear-resistant coatings on industrial components.
- Advanced Ceramics: Producing high-performance ceramics with tailored properties for electronics, aerospace, and energy applications.
-
Challenges and Considerations:
- Precursor Selection: The choice of precursor gases is critical, as they must decompose or react at the desired temperature without forming unwanted byproducts.
- Temperature Control: Precise temperature control is necessary to ensure consistent coating quality and avoid thermal degradation of the particles.
- Particle Size and Shape: The size and shape of the particles can affect fluidization behavior and coating uniformity, requiring careful optimization.
-
Comparison with Other Coating Methods:
- Compared to traditional CVD, fluidized bed CVD offers better particle-to-particle uniformity and is more suitable for coating small or irregularly shaped particles.
- Unlike physical vapor deposition (PVD), which is limited to line-of-sight coating, fluidized bed CVD can coat all surfaces of the particles, including internal pores.
By combining the benefits of fluidization and CVD, this process provides a powerful tool for creating high-performance coatings on particulate materials, making it indispensable in many advanced manufacturing and research applications.
Summary Table:
Aspect | Details |
---|---|
Principle | Combines fluidization and CVD for uniform particle coating. |
Advantages | Uniform coating, scalability, versatility for metals, ceramics, and polymers. |
Applications | Catalysts, protective coatings, advanced ceramics. |
Challenges | Precursor selection, temperature control, particle size optimization. |
Comparison | Better uniformity than traditional CVD; coats all surfaces unlike PVD. |
Discover how fluidized bed CVD can enhance your material coatings—contact our experts today!