CVD graphene, or Chemical Vapor Deposition graphene, is a high-quality, single-layer graphene material produced through a chemical vapor deposition process. This method involves the growth of graphene on surfaces like copper or nickel at high temperatures, enabling the production of large-scale, pure, and defect-free graphene. CVD graphene is highly versatile, with applications spanning electronics, optoelectronics, energy storage, and more. Its unique properties, such as high conductivity, mechanical strength, and transparency, make it a promising material for advanced technologies like transparent conductive films, sensors, and photoelectric devices. However, challenges related to cost, scalability, and uniformity need to be addressed for widespread adoption.
Key Points Explained:
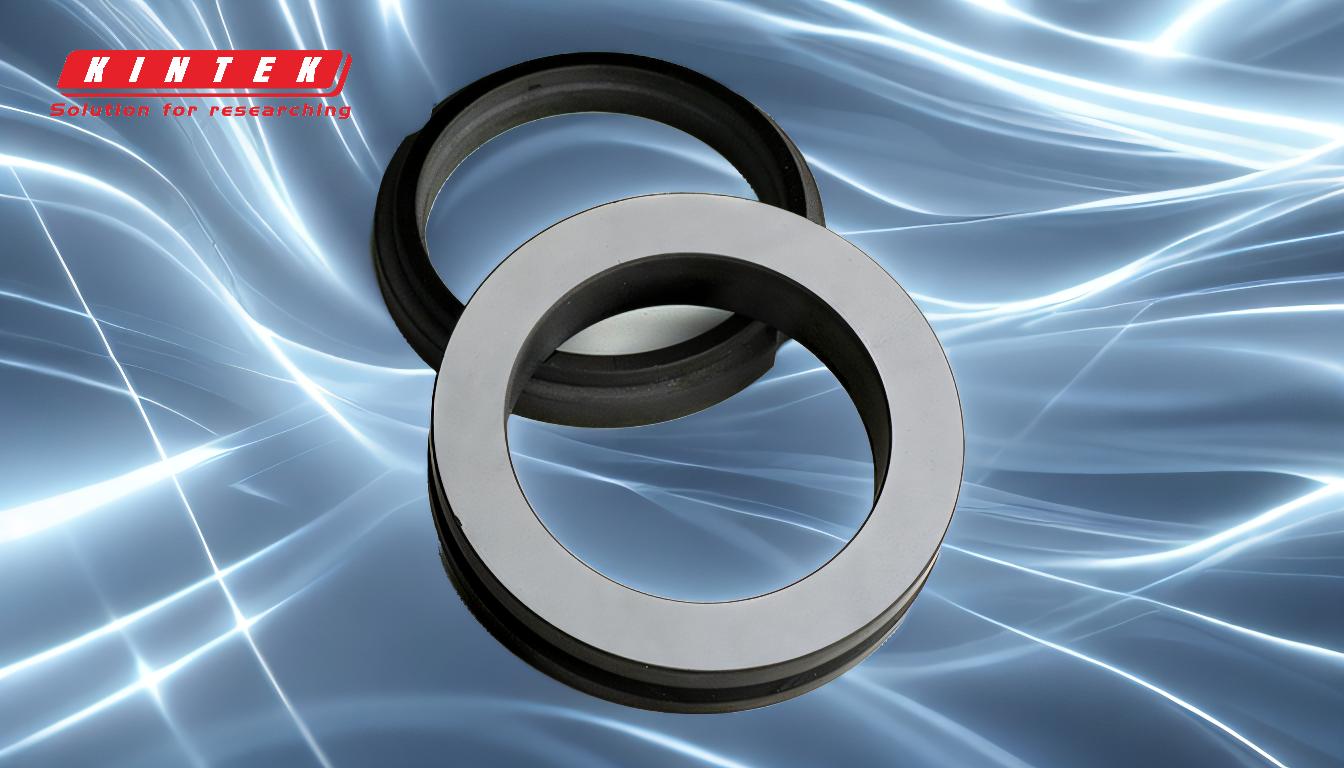
-
What is CVD Graphene?
- CVD graphene is a two-dimensional material grown using the Chemical Vapor Deposition (CVD) process. It involves depositing carbon atoms onto a substrate, typically copper or nickel, at high temperatures (around 1000 °C). This method allows for the production of large-area, high-quality, single-layer graphene with minimal defects.
-
How is CVD Graphene Produced?
- The CVD process involves mixing a carbon-containing source material with volatile precursors. These precursors chemically react and break down the source material, releasing carbon atoms. The carbon atoms are then transported to the substrate via gas flow, where they form a graphene layer. The by-products of the reaction are removed through the gas flow, ensuring a clean and efficient process.
-
Key Properties of CVD Graphene
- High Conductivity: CVD graphene exhibits excellent electrical conductivity, making it ideal for electronic applications.
- Mechanical Strength: Despite being only one atom thick, CVD graphene is incredibly strong, with a tensile strength much higher than steel.
- Transparency: Its high optical transparency makes it suitable for use in transparent conductive films, such as those used in touch screens and solar cells.
- Large Surface Area: The large surface area of CVD graphene is beneficial for applications in sensors and energy storage devices.
-
Applications of CVD Graphene
- Electronics: CVD graphene is used in designing heterostructures with semiconductors, enabling advancements in high-performance electronics and nonvolatile memories.
- Optoelectronics: Its transparency and conductivity make it ideal for use in photodetectors, light-emitting diodes (LEDs), and solar cells.
- Sensors: The large surface area and sensitivity of CVD graphene make it suitable for bioelectronics and chemical sensors.
- Thermal Management: Its high thermal conductivity is beneficial for applications in thermal management systems.
- Transparent Conductive Films: CVD graphene is a promising material for replacing indium tin oxide (ITO) in transparent conductive films, which are used in displays and touch screens.
-
Challenges and Future Prospects
- Cost: The high cost of producing CVD graphene is a significant barrier to its widespread adoption. Efforts are ongoing to develop more cost-effective production methods.
- Uniformity: Achieving uniform graphene layers over large areas remains a challenge, especially for industrial-scale production.
- Handling: Graphene is delicate and requires careful handling to prevent damage, which can complicate its integration into devices.
- Future Applications: Despite these challenges, CVD graphene holds immense potential for future applications in high-performance electronics, sensors, touch screens, and other advanced technologies.
In summary, CVD graphene is a revolutionary material with a wide range of applications in electronics, optoelectronics, and energy storage. While challenges remain in terms of cost and scalability, ongoing research and development are expected to unlock its full potential in the coming years.
Summary Table:
Aspect | Details |
---|---|
Definition | High-quality, single-layer graphene produced via Chemical Vapor Deposition. |
Production Process | Growth on copper/nickel substrates at high temperatures (~1000 °C). |
Key Properties | High conductivity, mechanical strength, transparency, large surface area. |
Applications | Electronics, optoelectronics, sensors, thermal management, conductive films. |
Challenges | High cost, uniformity issues, delicate handling. |
Future Prospects | Potential in advanced electronics, sensors, and touch screens. |
Unlock the potential of CVD graphene for your projects—contact us today to learn more!