Chemical Vapor Deposition (CVD) is a critical process in the fabrication of Micro-Electro-Mechanical Systems (MEMS) and the broader semiconductor industry. It involves the deposition of thin films of materials onto a substrate through chemical reactions of volatile precursors. This method is favored for its ability to produce high-quality, high-performance solid materials with excellent conformality, selectivity, and process flexibility. CVD is widely used in the production of integrated circuits, sensors, optoelectronic devices, and solar cells, making it indispensable in modern microelectronics and MEMS manufacturing.
Key Points Explained:
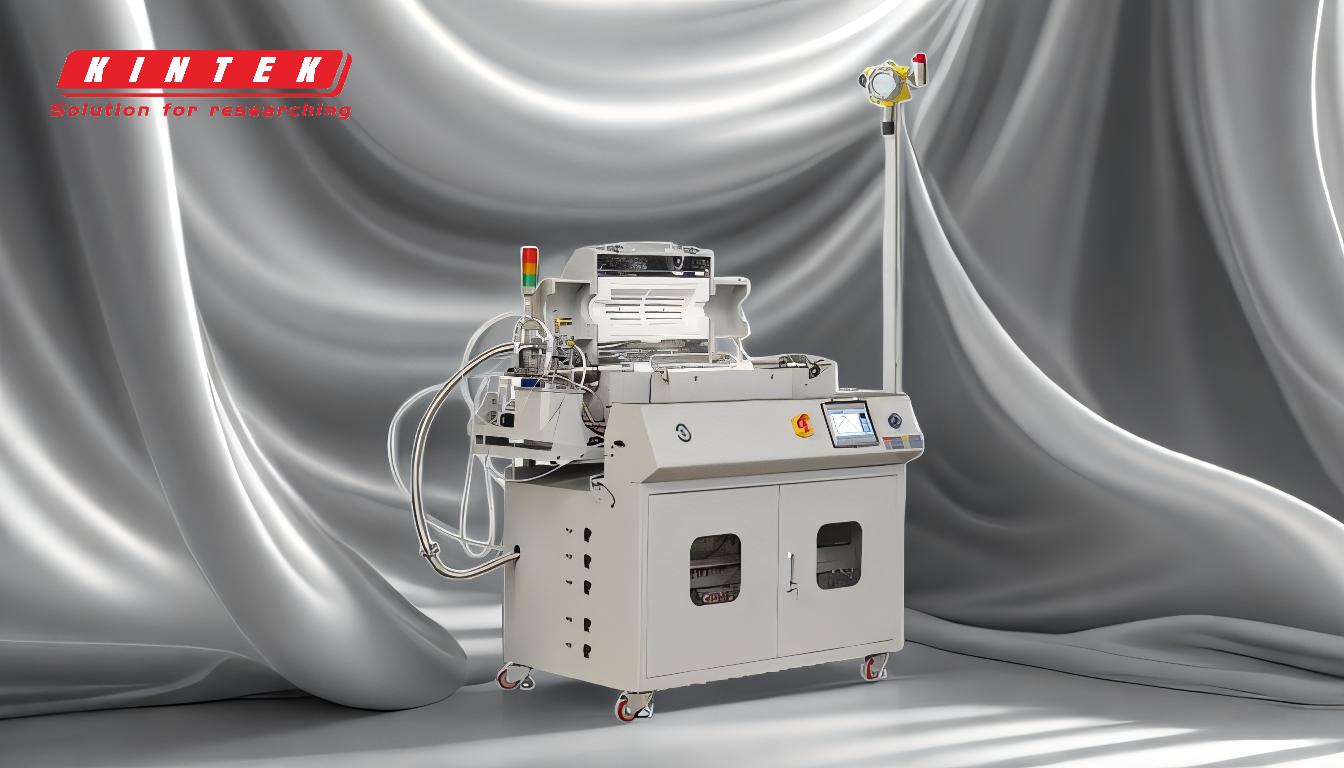
-
Definition of CVD in MEMS:
- CVD stands for Chemical Vapor Deposition, a process used to deposit thin films of materials onto a substrate in MEMS and semiconductor manufacturing.
- It involves exposing the substrate to volatile precursors that react or decompose on the substrate surface to form the desired material.
-
How CVD Works:
- Precursor Introduction: Volatile chemical precursors are introduced into a reaction chamber.
- Chemical Reaction: These precursors react or decompose on the heated substrate surface.
- Film Deposition: The reaction products form a thin film on the substrate, which can be a single crystal, polycrystalline, or amorphous material.
-
Applications of CVD in MEMS:
- Integrated Circuits: CVD is used to deposit various layers, such as silicon dioxide, silicon nitride, and polysilicon, which are essential for building integrated circuits.
- Sensors: Thin films deposited by CVD are used in the fabrication of sensors, including pressure sensors, accelerometers, and biosensors.
- Optoelectronic Devices: CVD is crucial for depositing materials used in optoelectronic devices, such as light-emitting diodes (LEDs) and photodetectors.
- Solar Cells: CVD is employed in the deposition of materials like crystalline silicon and thin-film layers in solar cell manufacturing.
-
Advantages of CVD in MEMS:
- Conformality: CVD can uniformly coat complex geometries and high-aspect-ratio structures, which is essential for MEMS devices with intricate designs.
- Selectivity: The process can be tailored to deposit materials selectively on specific areas of the substrate.
- Process Flexibility: CVD can deposit a wide range of materials, including metals, semiconductors, and insulators, with precise control over film properties.
- High-Quality Films: CVD produces high-purity, dense, and defect-free films, which are critical for the performance and reliability of MEMS devices.
-
Comparison with Other Deposition Methods:
- Molecular Beam Epitaxy (MBE): While MBE offers excellent control over film composition and structure, it is generally slower and more expensive than CVD. CVD's better scalability and process flexibility make it more suitable for large-scale MEMS manufacturing.
- Physical Vapor Deposition (PVD): PVD techniques, such as sputtering and evaporation, are limited in their ability to coat complex geometries uniformly. CVD's superior conformality makes it the preferred choice for MEMS applications.
-
Challenges and Considerations:
- Precursor Toxicity: Some CVD precursors are toxic or hazardous, requiring careful handling and disposal.
- Process Complexity: CVD processes can be complex, requiring precise control over temperature, pressure, and gas flow rates.
- Cost: While CVD is generally cost-effective for large-scale production, the initial setup and maintenance of CVD equipment can be expensive.
-
Future Trends in CVD for MEMS:
- Atomic Layer Deposition (ALD): A variant of CVD, ALD offers even greater control over film thickness and uniformity, making it increasingly popular for advanced MEMS applications.
- Low-Temperature CVD: Developing CVD processes that operate at lower temperatures is crucial for integrating MEMS with temperature-sensitive materials, such as polymers or biological components.
- Green CVD: Research is ongoing to develop more environmentally friendly CVD processes, using less toxic precursors and reducing waste.
In summary, CVD is a versatile and essential technique in MEMS and semiconductor manufacturing, offering numerous advantages in terms of film quality, conformality, and process flexibility. Despite some challenges, its benefits make it the preferred method for depositing thin films in a wide range of applications, from integrated circuits to sensors and solar cells.
Summary Table:
Aspect | Details |
---|---|
Definition | CVD deposits thin films on substrates using volatile precursors. |
Process | Precursor introduction → Chemical reaction → Film deposition. |
Applications | Integrated circuits, sensors, optoelectronic devices, solar cells. |
Advantages | Conformality, selectivity, process flexibility, high-quality films. |
Challenges | Precursor toxicity, process complexity, equipment cost. |
Future Trends | Atomic Layer Deposition (ALD), low-temperature CVD, green CVD. |
Learn how CVD can revolutionize your MEMS processes—contact our experts today!