CVD, or Chemical Vapor Deposition, is a process used to deposit thin films of materials onto a substrate through chemical reactions in a vapor phase. It is a critical technology in modern manufacturing, enabling the production of incredibly small, powerful, and useful devices across nearly all industries. CVD is widely used to create various thin films and nanomaterials, with graphene being the most notable product. It is also used to fabricate thin film semiconductor materials, which are essential in technologies like solar cells. As technology advances and devices become smaller, CVD is increasingly used to produce advanced semiconductor thin films instead of bulkier materials.
Key Points Explained:
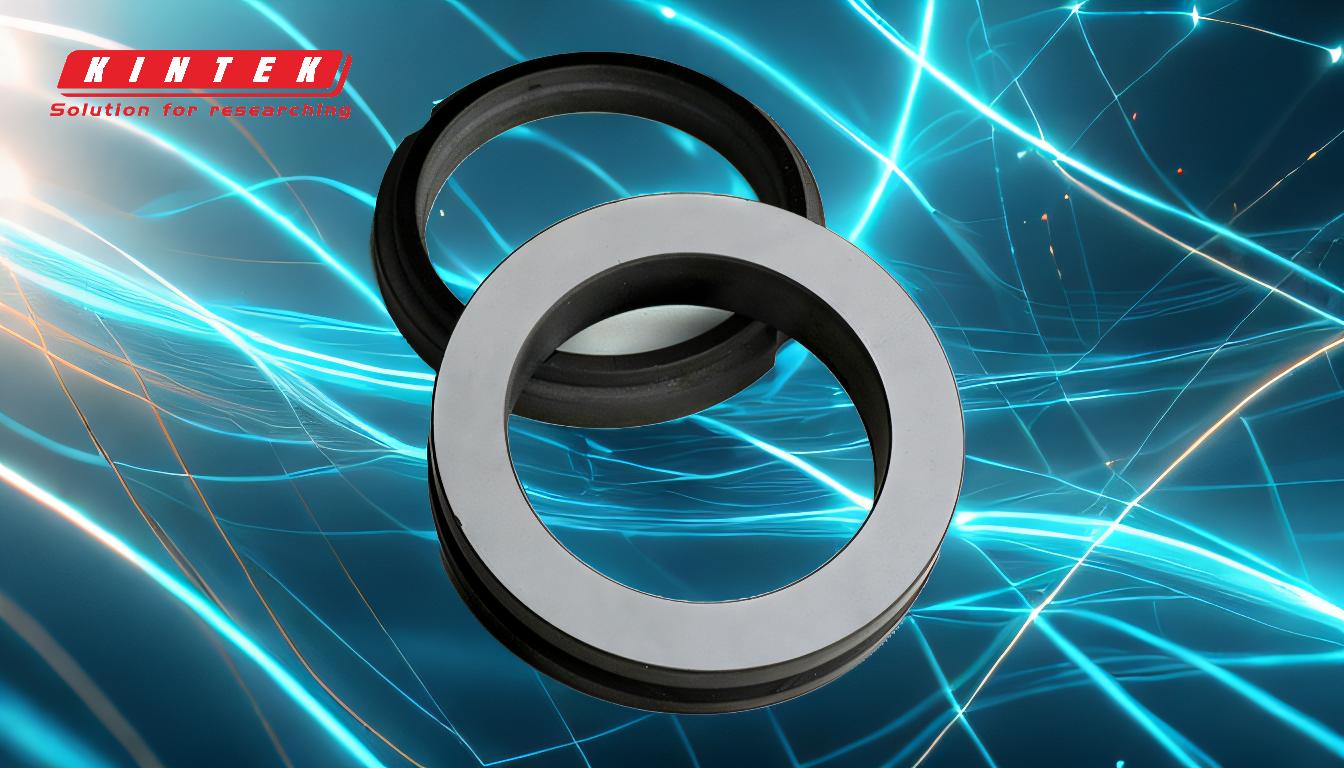
-
Definition of CVD:
- CVD stands for Chemical Vapor Deposition, a process used to deposit thin films of materials onto a substrate through chemical reactions in a vapor phase.
- The process involves the reaction of gaseous precursors to form a solid material on the substrate surface.
-
Applications of CVD:
- CVD is used in semiconductor manufacturing, flat panel display manufacturing, cutting tools or wear component manufacturing, optical coatings, magnetic storage, medical applications, and research and surface analysis.
- It processes materials such as metals, dielectrics, ceramics, aluminum, silicon, diamond-like carbon (DLC), dopants, germanium, silicides, compound semiconductors (GaAs), nitrides (TiN), and refractory metals.
-
Significance in Graphene Production:
- CVD is significant in graphene production as it allows for the growth of two-dimensional graphene material on surfaces, typically copper or nickel.
- The goal of CVD is to produce low-cost, pure, and perfect single-layer graphene through continuous roll-to-roll (R2R) production processes.
-
Role in Thin Film Deposition:
- Thin film deposition is a crucial process in making semiconductor devices, integrated circuits, and is paving the way for the development of nanotechnology.
- CVD is used to deposit diamond films on substrates, often at pressures lower than 1 atm. Researchers have demonstrated the use of intermediate layers, such as TiC, to improve the deposition of diamond films on titanium substrates.
-
Enhancing Properties and Applications:
- These films enhance tribological properties and biocompatibility, making them suitable for various applications.
- Thin films play a significant role in modern technology by enhancing efficiency in solar energy systems, enabling high-performance photovoltaic cells, and improving mechanical properties in nanotechnology.
-
Impact on Modern Technology:
- CVD is a critical technology in modern manufacturing, enabling the production of incredibly small, powerful, and useful devices across nearly all industries.
- Without CVD, the semiconductor industry and other sectors would be significantly less productive. It is used in applications ranging from depositing aluminum on potato chip bags to creating advanced artificial intelligence components.
-
Future Trends:
- As technology advances and devices become smaller, CVD is increasingly used to produce advanced semiconductor thin films instead of bulkier materials.
- The continuous development of CVD techniques is expected to further enhance the capabilities and applications of thin films in various industries.
Summary Table:
Aspect | Details |
---|---|
Definition | CVD deposits thin films via chemical reactions in a vapor phase. |
Applications | Semiconductors, graphene, solar cells, optical coatings, and more. |
Significance | Enables production of small, powerful devices across industries. |
Future Trends | Increasing use in advanced semiconductor thin films and nanotechnology. |
Learn how CVD can transform your manufacturing process—contact our experts today!