Chemical Vapor Deposition (CVD) is the most widely used method for the preparation of carbon nanotubes (CNTs) due to its cost-effectiveness, scalability, and ability to produce high-quality CNTs with controlled structures. Unlike traditional methods like laser ablation and arc discharge, CVD involves thermal treatments and gas-phase reactions to deposit carbon atoms onto a substrate, often using a catalyst to guide the growth of nanotubes. The process is versatile, allowing for the use of various feedstocks, including green or waste materials, which aligns with sustainability goals. However, the synthesis process must be optimized to minimize environmental impacts, such as energy consumption and greenhouse gas emissions.
Key Points Explained:
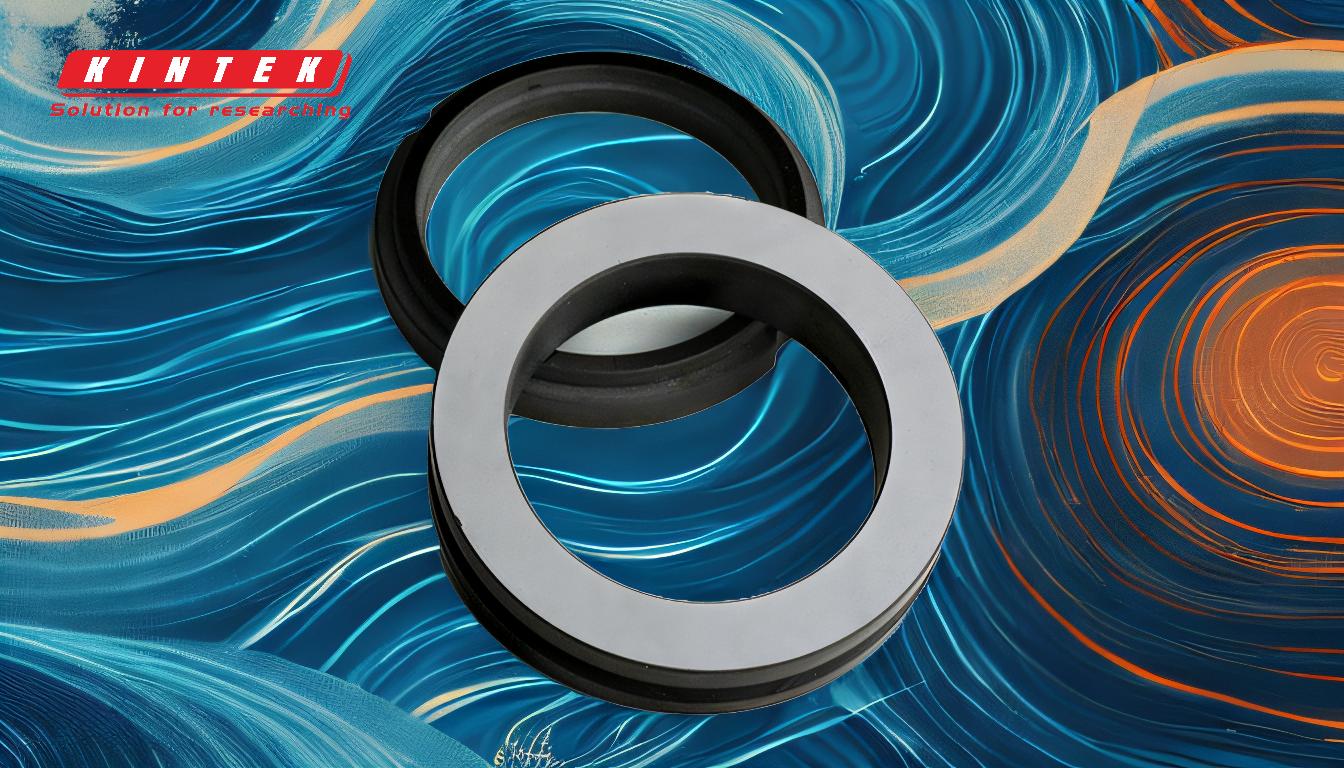
-
Overview of CVD for CNT Preparation:
- CVD is a thin film deposition technique that uses thermally or plasma-induced chemical reactions to produce high-quality coatings or materials, including carbon nanotubes.
- It is the dominant commercial method for CNT production due to its scalability, cost-effectiveness, and ability to control the structural properties of the nanotubes.
-
CVD Process Mechanism:
- The CVD process involves the decomposition of a carbon-containing gas (e.g., methane, ethylene, or carbon dioxide) at high temperatures in the presence of a catalyst (e.g., iron, nickel, or cobalt).
- The carbon atoms are deposited onto a substrate, where they rearrange and grow into nanotubes under the influence of the catalyst.
-
Catalytic Chemical Vapor Deposition (CCVD):
- CCVD is the most common variant of CVD used for CNT synthesis. It employs a catalyst to lower the activation energy required for the growth of nanotubes.
- The catalyst particles act as nucleation sites, guiding the formation of CNTs with specific diameters and structures.
-
Advantages of CVD:
- Scalability: CVD can be easily scaled up for industrial production, making it suitable for large-scale manufacturing of CNTs.
- Structural Control: The process allows for precise control over the diameter, length, and chirality of the nanotubes, which is crucial for tailoring their properties for specific applications.
- Cost-Effectiveness: Compared to other methods like laser ablation and arc discharge, CVD is more economical due to lower energy requirements and the use of readily available feedstocks.
-
Environmental Considerations:
- The synthesis of CNTs via CVD involves significant energy consumption and greenhouse gas emissions, which contribute to its life cycle ecotoxicity.
- Efforts are being made to reduce the environmental impact by using green or waste feedstocks, such as carbon dioxide captured by electrolysis in molten salts or methane pyrolysis.
-
Emerging Trends in CVD for CNTs:
- Researchers are exploring the use of sustainable feedstocks, such as carbon dioxide and methane, to produce CNTs with reduced environmental impact.
- Innovations in catalyst design and process optimization are also being pursued to enhance the efficiency and sustainability of CVD-based CNT production.
-
Applications of CVD-Grown CNTs:
- CVD-grown CNTs are used in a wide range of applications, including electronics, energy storage, composites, and biomedical devices, due to their exceptional mechanical, electrical, and thermal properties.
In summary, CVD is a versatile and efficient method for the preparation of carbon nanotubes, offering significant advantages in terms of scalability, structural control, and cost-effectiveness. However, ongoing research is focused on making the process more sustainable by reducing its environmental impact and exploring alternative feedstocks.
Summary Table:
Aspect | Details |
---|---|
Process Overview | Thermal/plasma-induced chemical reactions deposit carbon atoms on substrates. |
Key Mechanism | Decomposition of carbon-containing gases at high temperatures with catalysts. |
Main Variant | Catalytic Chemical Vapor Deposition (CCVD) for controlled CNT growth. |
Advantages | Scalability, structural control, and cost-effectiveness. |
Environmental Impact | High energy consumption; efforts to use green/waste feedstocks underway. |
Applications | Electronics, energy storage, composites, and biomedical devices. |
Interested in leveraging CVD for carbon nanotube production? Contact our experts today to learn more!