The Chemical Vapor Deposition (CVD) process is a widely used technique for depositing thin films and coatings onto substrates. It involves the chemical reaction of gaseous precursors on a substrate surface to form a solid material. The process is highly controllable, allowing for precise adjustments in film thickness, composition, and properties. CVD is used in various industries, including semiconductor manufacturing, optics, and materials science, due to its ability to produce high-quality, uniform coatings. The process typically involves steps such as reactant introduction, activation, surface reaction, and byproduct removal, with factors like temperature, pressure, and gas flow rates playing critical roles in determining the final product's characteristics.
Key Points Explained:
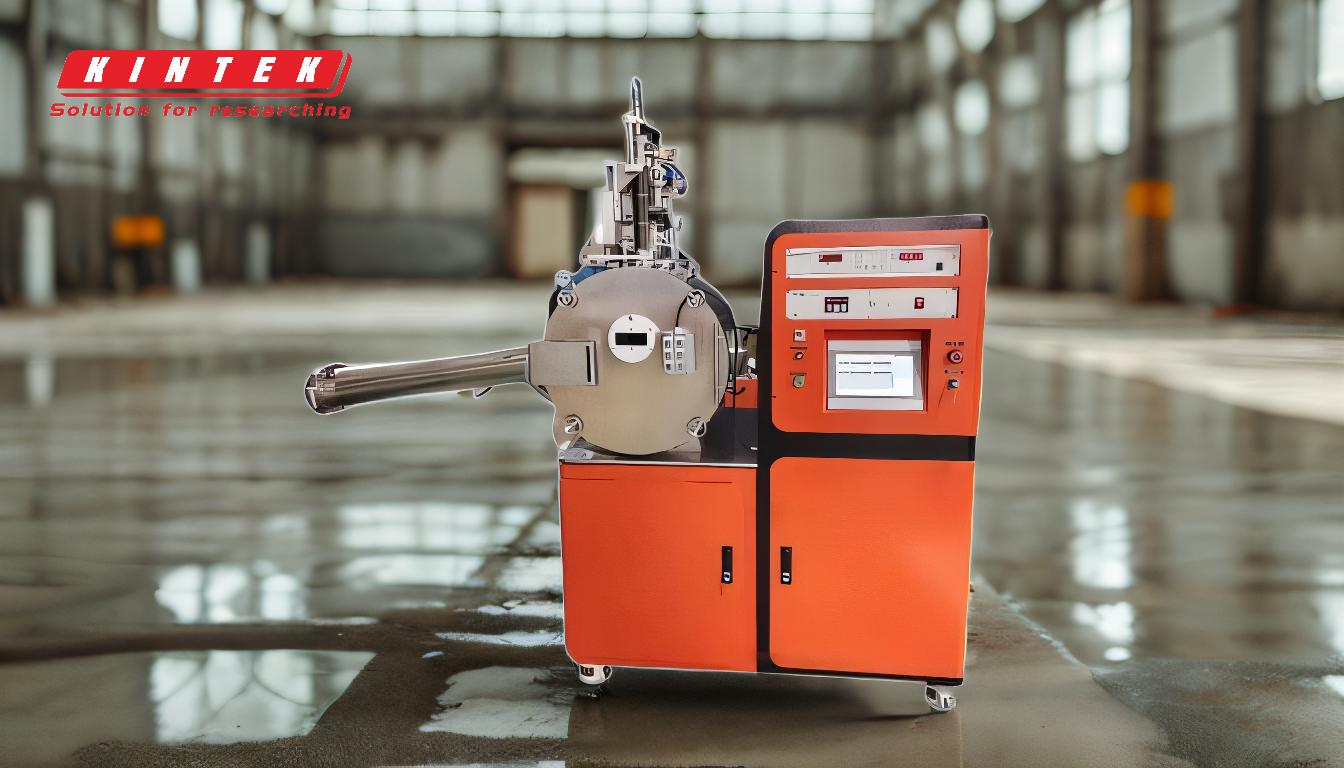
-
Introduction of Reactants:
- Gaseous precursors are introduced into a reaction chamber containing the substrate.
- These precursors are chosen based on the desired material to be deposited.
- The gas mixture is carefully controlled to ensure uniform deposition.
-
Activation of Reactants:
- Precursors are activated through methods such as thermal energy, plasma, or catalysts.
- Activation breaks down the precursors into reactive species that can participate in the deposition process.
- This step is crucial for initiating the chemical reactions necessary for film formation.
-
Surface Reaction and Deposition:
- Activated precursors react at the substrate surface to form the desired material.
- The reaction can involve multiple steps, including adsorption, diffusion, and chemisorption.
- The surface reaction is influenced by factors such as temperature, pressure, and substrate material.
-
Removal of Byproducts:
- Volatile or non-volatile byproducts are eliminated from the reaction chamber.
- This step ensures that the deposition process remains efficient and that the final film is free of impurities.
- Byproducts are typically removed through gas flow or vacuum systems.
-
Influence of Process Parameters:
- Temperature: High temperatures are often required to activate the precursors and drive the surface reactions.
- Pressure: Low pressures are typically used to enhance gas diffusion and reduce unwanted reactions.
- Gas Flow Rates: Controlled gas flow ensures uniform deposition and efficient removal of byproducts.
-
Applications of CVD:
- Semiconductor Manufacturing: CVD is used to deposit thin films of materials like silicon dioxide, silicon nitride, and polysilicon.
- Optics: CVD is employed to create anti-reflective coatings and other optical films.
- Materials Science: CVD is used to produce advanced materials such as graphene, carbon nanotubes, and ceramic coatings.
-
Advantages of CVD:
- High-Quality Films: CVD produces films with excellent uniformity, density, and purity.
- Versatility: The process can be adapted to deposit a wide range of materials.
- Scalability: CVD is suitable for both small-scale research and large-scale industrial production.
-
Challenges and Considerations:
- Cost: CVD equipment and precursors can be expensive.
- Complexity: The process requires precise control of multiple parameters.
- Safety: Handling reactive gases and high temperatures necessitates strict safety protocols.
In summary, the CVD process is a versatile and powerful technique for depositing thin films and coatings. By carefully controlling the introduction, activation, and reaction of gaseous precursors, along with the removal of byproducts, high-quality materials can be produced for a wide range of applications. Understanding the influence of process parameters and the specific steps involved is crucial for optimizing the CVD process and achieving the desired results.
Summary Table:
Key Aspect | Details |
---|---|
Steps | Reactant Introduction, Activation, Surface Reaction, Byproduct Removal |
Key Parameters | Temperature, Pressure, Gas Flow Rates |
Applications | Semiconductors, Optics, Materials Science |
Advantages | High-Quality Films, Versatility, Scalability |
Challenges | Cost, Complexity, Safety Protocols |
Discover how the CVD process can enhance your production—contact our experts today for tailored solutions!