CVD, or Chemical Vapor Deposition, is a process used to create thin films or coatings on a substrate by exposing it to volatile precursors that react or decompose on the surface. It is widely used in industries such as semiconductor manufacturing, optics, and even in producing lab-grown diamonds. Polymerization, in the context of CVD, refers to the chemical reaction where two or more monomer precursors combine to form polymer chains, which then deposit as a uniform coating on the substrate. This process is controlled by factors like temperature, pressure, and reaction duration to achieve the desired film properties.
Key Points Explained:
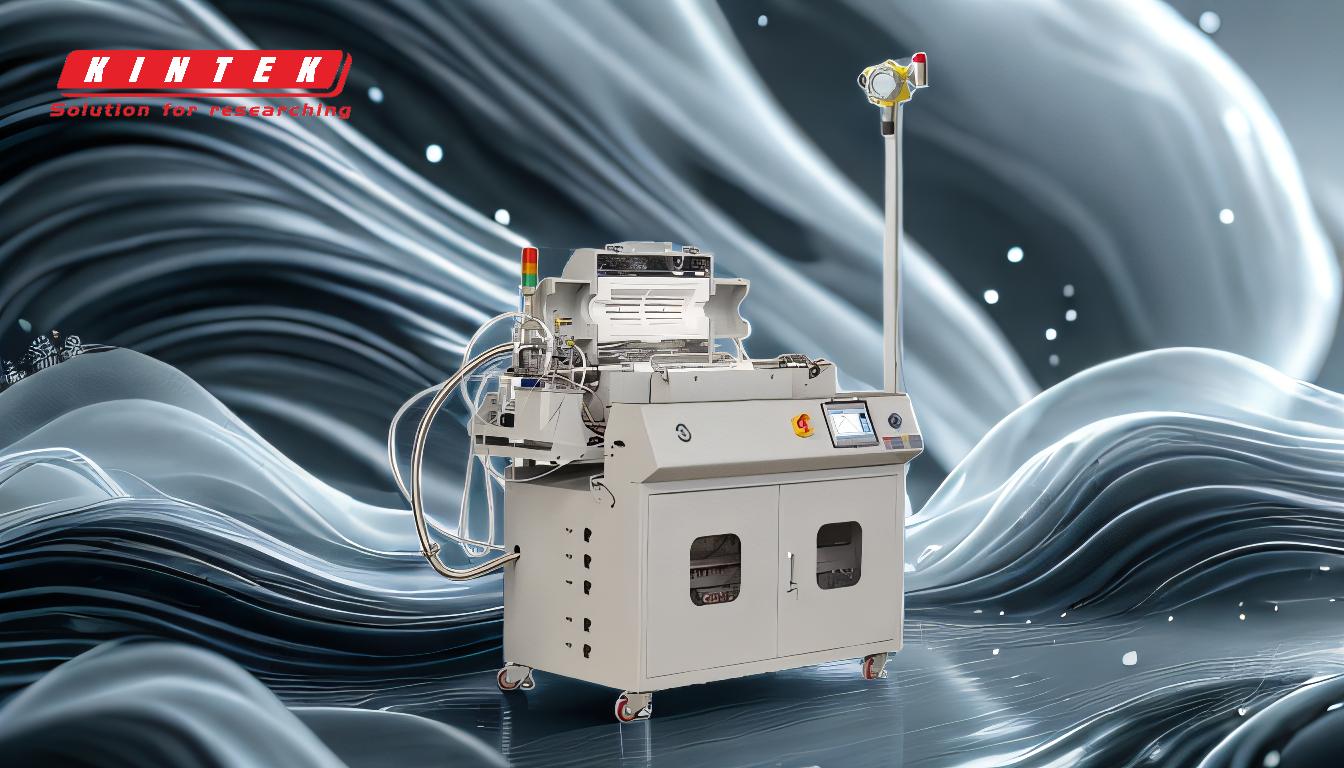
-
What is CVD?
- CVD stands for Chemical Vapor Deposition.
- It is a process where a substrate is exposed to one or more volatile precursors in a vacuum chamber.
- The precursors react or decompose on the substrate surface to form a thin film or coating.
- Applications include semiconductor manufacturing, optics, and lab-grown diamond production.
-
How does CVD work?
- The substrate is placed in a vacuum chamber.
- Precursor gases are introduced into the chamber.
- Under controlled temperature and pressure, the gases react or decompose on the substrate surface.
- The reaction products deposit as a thin film on the substrate.
-
What is polymerization in CVD?
- Polymerization refers to the chemical reaction where monomers (small molecules) combine to form polymers (long-chain molecules).
- In polymer-based CVD, two or more monomer precursors are introduced into the chamber.
- These monomers react to form polymer chains, which then deposit on the substrate as a uniform coating.
-
Key factors in CVD and polymerization:
- Temperature: Controls the rate of reaction and the quality of the deposited film.
- Pressure: Affects the density and uniformity of the coating.
- Duration: Determines the thickness of the deposited film.
- Precursor composition: Influences the chemical and physical properties of the final film.
-
Applications of CVD and polymerization:
- Semiconductors: Used to deposit thin films of silicon, silicon dioxide, and other materials.
- Optics: Creates anti-reflective coatings and other optical layers.
- Lab-grown diamonds: Produces diamonds by decomposing hydrocarbon gases in a controlled environment.
- Protective coatings: Provides wear-resistant and corrosion-resistant layers on various materials.
-
Advantages of CVD:
- High purity and uniformity of deposited films.
- Ability to coat complex shapes and large areas.
- Versatility in materials that can be deposited (metals, ceramics, polymers).
- Environmentally friendly compared to some other deposition methods.
-
Challenges in CVD and polymerization:
- Requires precise control of process parameters (temperature, pressure, gas flow).
- High equipment and operational costs.
- Limited deposition rates compared to other methods like physical vapor deposition (PVD).
By understanding CVD and polymerization, equipment and consumable purchasers can make informed decisions about the materials and processes needed for specific applications, ensuring optimal performance and cost-effectiveness.
Summary Table:
Aspect | Details |
---|---|
What is CVD? | Process to create thin films by exposing substrates to volatile precursors. |
How CVD works | Precursors react/decompose on a substrate in a vacuum chamber. |
Polymerization in CVD | Monomers combine to form polymer chains, depositing as uniform coatings. |
Key Factors | Temperature, pressure, duration, and precursor composition. |
Applications | Semiconductors, optics, lab-grown diamonds, protective coatings. |
Advantages | High purity, uniform coatings, versatility, eco-friendly. |
Challenges | Precise control, high costs, limited deposition rates. |
Discover how CVD and polymerization can enhance your applications—contact our experts today!